Цемент т: Т-Цемент, ООО, ИНН 7733652803 | Реквизиты, юридический адрес, КПП, ОГРН, схема проезда, сайт, e-mail, телефон
«Сибцем» в 2014 г увеличил выпуск цемента на 1% — до 4,35 млн т
https://realty.ria.ru/20150127/404228493.html
«Сибцем» в 2014 г увеличил выпуск цемента на 1% — до 4,35 млн т
«Сибцем» в 2014 г увеличил выпуск цемента на 1% — до 4,35 млн т — Недвижимость РИА Новости, 29.02.2020
«Сибцем» в 2014 г увеличил выпуск цемента на 1% — до 4,35 млн т
ОАО «Холдинговая компания «Сибирский цемент» в 2014 году увеличило производство цемента по сравнению с предыдущим годом на 1,3% — до 4,347 миллиона тонн, говорится в сообщении компании.
2015-01-27T14:23
2015-01-27T14:23
2020-02-29T13:50
/html/head/meta[@name=’og:title’]/@content
/html/head/meta[@name=’og:description’]/@content
https://cdnn21.img.ria.ru/images/realty/39631/72/396317236_0:275:3067:2000_1920x0_80_0_0_452c38927b15791c0eabf56bde448501.jpg
москва
россия
Недвижимость РИА Новости
internet-group@rian.ru
7 495 645-6601
ФГУП МИА «Россия сегодня»
https://xn--c1acbl2abdlkab1og. xn--p1ai/awards/
2015
Недвижимость РИА Новости
internet-group@rian.ru
7 495 645-6601
ФГУП МИА «Россия сегодня»
https://xn--c1acbl2abdlkab1og.xn--p1ai/awards/
Новости
ru-RU
https://realty.ria.ru/docs/about/copyright.html
https://xn--c1acbl2abdlkab1og.xn--p1ai/
Недвижимость РИА Новости
internet-group@rian.ru
7 495 645-6601
ФГУП МИА «Россия сегодня»
https://xn--c1acbl2abdlkab1og.xn--p1ai/awards/
https://cdnn21.img.ria.ru/images/realty/39631/72/396317236_116:0:2783:2000_1920x0_80_0_0_9bb05b0c578506b041772245d17273e1.jpgНедвижимость РИА Новости
internet-group@rian.ru
7 495 645-6601
ФГУП МИА «Россия сегодня»
https://xn--c1acbl2abdlkab1og.xn--p1ai/awards/
Недвижимость РИА Новости
internet-group@rian.ru
7 495 645-6601
ФГУП МИА «Россия сегодня»
https://xn--c1acbl2abdlkab1og.xn--p1ai/awards/
новости — недвижимость, москва, стройматериалы, цемент, сибцемент, производство, россия
14:23 27.
ОАО «Холдинговая компания «Сибирский цемент» в 2014 году увеличило производство цемента по сравнению с предыдущим годом на 1,3% — до 4,347 миллиона тонн, говорится в сообщении компании.
Линия по производству цемента сухим способом (50 т/сутки)
Производительность клинкера | 50 т/сутки | |
Вращающаяся | Модель | Φ1.6/1.9×36м |
Производительность | 2 т/ч | |
Температура (℃) | 1450 | |
Сырьевая | Модель | Φ1.5×5.7м |
Производительность | 4.5 т/ч | |
Мощность | 130кВт | |
Цементная
| Модель | Φ1. Незамкнутая цепь |
Производительность | 3.5 т/ч | |
Мощность | 130 кВт |
1.1.Дробление и складирование известняка, железной руды и т.д. :
На данном участке, поступающее на завод сырье обрабатывается с помощью дробилок до определенной фракции и транспортируется на склады;
1.2.Дробление, сушение и складирование глины и т.д. :
На данном участке, поступающее на завод сырье обрабатывается с помощью дробилок до определенной фракции и транспортируется на склады;
1.3.Шихтовка сырья :
После дробления сырье шихтуется по определенной пропорции и готовится к помолу;
1.4.Гомогенизация сырья :
Гомогенизация сырья требуется для стабильности качества выпускаемой продукции, данная работа поможет уменьшить влияние сырья от различных источников на стабильность качества цемента.
1.5.Помол сырья :
На данном участке сырье размельчается в порошок и транспортируется на обжиг;
1.6.Подготовка угля :
Уголь размельчается в порошок, сушится, собирается и подается на горелку;
1.7.Обжиг клинкера :
Сырье в данном участке обжигается до получения клинкера и охлаждается с помощью тепловых агрегатов, транспортируется на склад;
1.8.Дробление гипса и др. добавок :
Дробление добавок для цемента;
1.9.Шихтовка цемента :
Перемешивается клинкер с добавками по определенной пропорции, готовится к помолу;
1.10.Помол цемента :
Клинкер с добавками размельчаются в порошок ( цемент ) и подаются на участок упаковки;
1.11.Упаковка цемента :
Цемент упаковывается и готовится к отгрузке;
Тротуарная плитка Старый Город Альпин верхний прокрас mix основа — серый цемент набор на м2 t=60мм Фабрика Готика Поставщик№ 74 Подолино
1. На время распутицы вводится временное ограничение движения транспортных средств с грузом, следующим по автомобильным дорогам общего пользования (закрытие дорог в связи с весенним паводком)
В период временного ограничения действуют следующие допустимые нагрузки:
- 5-ти осное ТС 25т — нагрузка 13 тонн,
- 4-х осное ТС 20т — нагрузка 8 тонн,
- 3-х осное ТС 10т — нагрузка 4 тонны.
2. Въезд в пределы МОЖД (Московская окружная железная дорога) транспортного средства грузоподъемностью свыше 3,5 тонн по согласованию.
3. Въезд в пределы ТТК (Третье транспортное кольцо) транспортного средства грузоподъемностью свыше 1 тонны по согласованию.
5. Время доставки заказа в течение дня:
- с 8.00 до 22.00 в период с апреля по сентябрь
- с 8.00 до 19.00 в период с октября по март
6. В случае поставки заказа большим или меньшим количеством автомашин перерасчет заказа не производится.
7. Покупатель обязан обеспечить наличие подъезда от автомобильных дорог общего пользования с асфальтобетонным покрытием к месту разгрузки (твердое покрытие, ширина дороги не менее 3 метров, радиус разворота не менее 15 метров) с отсутствием по маршруту подъезда к месту разгрузки дорожных знаков, запрещающих движение данному виду транспорта, в противном случае оплатить все дополнительные расходы, возникшие из-за невыполнения данных условий по расценкам Поставщика.
8. Покупатель обязан обеспечить место для разгрузки Товара, позволяющее беспрепятственно и быстро осуществить разгрузку. Покупатель обязан обеспечить строповку (обвязку) Товара для производства разгрузочных работ, в том числе манипулятором. Если разгрузка Товара осуществляется силами Поставщика, а Покупатель просит выгрузить Товар через какие-либо препятствующие разгрузочным работам объекты (заборы, ограды, столбы освещения, ЛЭП, деревья и прочее), затраты, связанные с повреждением и восстановлением указанных обектов, полностью ложатся на Покупателя.
9. Покупатель обязан обеспечить разгрузку транспортного средства грузоподъемностью 1,5 — 5 тонн в течение 1 часа, свыше 5 тонн — в течение 2 часов.
10. В случае простоя транспортного средства с товаром в месте выгрузки свыше времени, указанного в п.9 Покупатель обязан оплатить водителю простой в размере 1000 р. за каждый последующий час.
11. Приемка Товара по количеству, ассортименту и качеству (внешнему виду) осуществляется во время передачи Товара Покупателю или его уполномоченному представителю. При обнаружении недостатков Товара во время его приемки Покупатель обязан приостановить разгрузку и немедленно известить Поставщика о выявленных дефектах. В одностороннем порядке составить акт с указанием подробного перечня выявленных дефектов и отметить это в товарной накладной. После приемки и подписания документов на Товар Покупатель лишается права в дальнейшем предъявлять претензии Поставщику по количеству, ассортименту и качеству Товара.
12. В случае не предоставления доверенностей на уполномоченное лицо выгрузка Товара не производится.
13. Поставщик не принимает претензии по качеству при неправильной разгрузке заказа (сбрасыванием).
14. При отказе Покупателем от заказа после его оплаты Покупатель возмещает Поставщику расходы, понесенные в связи с совершением действий по выполнению Договора.
15. При оплате Заказа на условиях предоплаты (менее 100%) Покупатель обязан произвести окончательный расчет до момента поставки.
Цемент отвечает за 8% глобальных выбросов, но есть решение
30 миллиардов тонн бетона, которые ежегодно производятся в мире, имеют огромный углеродный след. Цемент, основной ингредиент, отвечает за около 8% глобальных выбросов, а это означает, что если бы это была страна, она была бы третьим по величине загрязнителем климата на планете.
Калифорнийский стартап под названием Brimstone Energy запатентовал новый процесс, который снижает выбросы портландцемента (наиболее часто используемый тип) до нуля. При использовании с возобновляемыми источниками энергии этот процесс на самом деле является углеродно-отрицательным, а это означает, что цемент может превратиться из климатической проблемы в решение.
Энергия является одной из проблем традиционного производства цемента, поскольку оно работает на ископаемом топливе и требует нагрева печи до более чем 2500 градусов по Фаренгейту. Но даже если бы цементные компании обеспечивали весь процесс возобновляемой энергией, из-за химии все еще остается фундаментальная проблема. «Вы начинаете с породы, называемой известняком, а известняк — это, по сути, затвердевший CO2», — говорит Коди Финке, соучредитель и генеральный директор Brimstone, среди финансовых спонсоров которой — Breakthrough Energy Ventures Билла Гейтса.Когда известняк или карбонат кальция нагревают до высоких температур, образуется известь, компонент цемента. Но при этом выделяется огромное количество CO2.
[Фото: Brimstone Energy] Вместо этого Brimstone использует другой тип горной породы, силикат кальция, который не выделяет CO2 при нагревании для производства извести. Он создает диоксид кремния, побочный продукт, который можно использовать для замены летучей золы, отходов, образующихся на угольных электростанциях, который является еще одним ингредиентом обычного цемента.«Этот процесс был изобретен вокруг пикового угля, чтобы соответствовать энергетической системе», — говорит Финке. С исчезновением угольных электростанций материал становится менее доступным, и это еще один источник выбросов в стандартном продукте (хотя учет углерода обычно не включает летучую золу при расчете общего следа производства цемента).
[Фото: Brimstone Energy] В то время как несколько других стартапов работают над созданием новых типов цемента, которые также сокращают выбросы, Brimstone хотела создать промышленный стандарт портландцемента, который имеет определенный химический состав.Финке говорит, что инженеры не склонны рисковать новыми материалами по очевидным причинам. «Вы можете построить свое здание из того же материала, что и все здания на планете, или вы можете построить свое здание из нового материала, из которого раньше не строился ни один небоскреб», — говорит он. Поскольку риск того, что что-то пойдет не так, очень велик — потенциальные смерти и сотни миллионов долларов затрат на строительство больших зданий, — инженеры хотят продолжать выбирать то, что проверено.
«Предприниматели десятилетиями боролись за разработку рецептур цемента, которые улавливают больше CO2, или обеспечивают равную прочность при меньшей массе, или смешивают ингредиенты цемента в менее загрязняющих пропорциях», — говорит Закари Бог, соучредитель и управляющий партнер DCVC, который только что инвестировал в начальный раунд финансирования Brimstone вместе с Breakthrough Energy Ventures. «Ни одна из альтернатив не работала очень хорошо: секвестрация улавливала лишь часть CO2, а нарушение рецептуры цемента обеспокоило регулирующие органы, обеспокоенные структурной целостностью.
Когда Brimstone переработает силикат кальция, стартап также получит груды магния, породы, которая естественным образом поглощает CO2 из воздуха. Это означает, говорит Финке, что даже если цемент будет производиться с использованием ископаемого топлива, он все равно будет углеродно-нейтральным. Если это будет сделано с использованием возобновляемых источников энергии, это «будет очень углеродно-отрицательным», говорит он.
В настоящее время компания проектирует свою первую пилотную установку и будет сотрудничать с существующими производителями цемента и бетона. Ожидается, что когда продукт появится на рынке, он будет стоить столько же, сколько традиционный портландцемент, или даже меньше.Это единственный способ быстро получить признание, говорит Финке, отмечая: «Моя теория изменений заключается в том, что вещи никогда не становились дешевле и дороже. Они всегда идут от более дорогих к более дешевым».
Построение лучшего мира с помощью зеленого цемента | Наука
Novacem планирует протестировать свой экспериментальный цемент (вверху: образцы блоков) сначала в таких конструкциях, как собачьи будки и патио. Алекс Маси «Вы знаете, цемент повсюду», — говорит Николаос Власопулос, инженер-эколог из Имперского колледжа в Лондоне, сидя в ярко освещенном конференц-зале колледжа в громадном семиэтажном здании, поддерживаемом темой разговора.
В прошлом году в мире было произведено 3,6 миллиарда тонн цемента — минеральной смеси, которая затвердевает в бетон при добавлении к воде, песку и другим материалам, — и к 2050 году это количество может увеличиться на миллиард тонн. из бетона в общем объеме составляет вода.
Достоинства цемента, говорит Власопулос, уже давно очевидны: «Он недорогой, сыпучий и, по некоторым необъяснимым причинам, становится твердым, как камень. Но редко признается еще одна важная деталь: цемент грязный.Не грязный, потому что не стирается с одежды, хотя эта проблема веками преследовала строителей. Ключевым ингредиентом является известняк, в основном карбонат кальция, останки морских существ в панцирях. Рецепт изготовления цемента требует нагревания известняка, для чего требуется ископаемое топливо. А при нагревании известняк выбрасывает углекислый газ в атмосферу, где он удерживает тепло, способствуя глобальному потеплению. На производство цемента приходится 5 процентов мировых выбросов углекислого газа, производимых человеком; в Соединенных Штатах только потребление ископаемого топлива (для транспорта, электричества, химического производства и других целей) и металлургическая промышленность выделяют больше парниковых газов.
Если широкая общественность в значительной степени игнорирует огромный вклад цемента в загрязнение воздуха, 31-летний Власопулос уже давно знает об этом. Он вырос в Патрах, греческом порту. Его отец был инженером, а мать работала в банке, а летом Власопулос возвращался из колледжа Dimokrition Panepistimion Thrakis, где он изучал экологическую инженерию, вместе с дядей работал на цементном заводе.Это было случайно. Его работа заключалась в сборке оборудования для измерения уровня выбросов углекислого газа. Они были высокими; как правило, завод производит почти тонну углекислого газа на каждую тонну цемента. Власопулос считал работу интересной, но не видел цемента в своем будущем. Это было скучно, это было старо, это было грязно.
Затем один из его профессоров Имперского колледжа, где он работал над получением степени магистра инженерии, получил финансирование на исследование нового типа цемента, производимого австралийской компанией. Профессор Кристофер Чизман убедил Власопулоса принять участие в проекте и получить степень доктора философии. «Это был шанс проделать хорошую работу», — сказал Власопулос в своей типично сдержанной манере.
Люди пытались построить лучший цемент с самого начала истории. Более 2000 лет назад римляне изобрели смесь извести, вулканического пепла и кусков камня для изготовления бетона, который использовался для строительства гаваней, памятников и зданий — клея для ранних городов, включая Пантеон и Колизей.В 1820-х годах в Лидсе, Англия, примерно в 200 милях от Имперского колледжа, каменщик по имени Джозеф Аспдин изобрел современный цемент. Аспдин подогрел смесь из мелкоизмельченного известняка и глины на своей кухне. После добавления воды смесь затвердела. Voilà — родился строительный блок промышленной революции. Поскольку этот материал был похож на популярный строительный камень с острова Портленд, Аспдин назвал свое изобретение портландцементом. Патент, выданный в 1824 году, предназначался для «улучшения способа производства искусственного камня.
Австралийские разработчики опробовали новый рецепт, смешав портландцемент с оксидом магния. Они надеялись сократить выбросы углерода, потому что оксид магния может заменить часть известняка, а оксид магния не нужно нагревать до такой высокой температуры. Известняк должен быть нагрет до 2600 градусов по Фаренгейту, но оксид магния может быть приготовлен для цемента при 1300 градусах, температура, которая может быть достигнута с биомассой и другими видами топлива, которые выделяют меньше углерода, сокращая потребление ископаемого топлива.
Но Власопулос быстро обнаружил, что смесь не снижает общий выброс углекислого газа. В некоторых тестах выбросы почти удвоились, потому что сам оксид магния производится путем нагревания карбонатов магния, в процессе которого выделяется углекислый газ.
«Помню, я был очень разочарован, потому что, когда вы видите, что проект, над которым вы работаете, на самом деле не такой, каким вы его себе представляли, вы теряете мотивацию», — сказал он. «Но мы чувствовали, что это очень стоящий проект, стоящая идея, поэтому мы попытались найти другой способ решить проблему.
В то время, когда Власопулос поднял этот вопрос в 2004 году, крупные цементные компании по всему миру искали новые способы сделать портландцемент более приемлемым для окружающей среды. Производители добавили побочные продукты стали, такие как шлак; угольные остатки, такие как летучая зола; и другие материалы, такие как оксид магния, для увеличения объема цементной смеси, что требует меньшего количества портландцемента. Они экспериментировали с минеральными добавками, чтобы снизить температуру, необходимую для подготовки материалов.
Но трудно модифицировать продукт, химический состав которого недостаточно изучен.«На самом деле мы никогда не знали точного химического состава того, как этот материал затвердевает», — сказал Хэмлин Дженнингс, эксперт по химии цемента и глава Центра устойчивого развития бетона Массачусетского технологического института, одной из нескольких академических инициатив по созданию «зеленого» цемента. «Я не думаю, что сегодня в мире используется какой-либо строительный материал, который менее изучен, чем портландцемент».
Пока цементные компании возились с оригиналом, Власопулос пошел другим путем. «Вы можете сделать так много с портландцементом, чтобы сделать его лучше», — сказал он.»Что есть, то есть. Это материал, с которого вы начинаете. Мы должны были придумать что-то еще». Власопулосу понравилась идея использовать оксид магния вместо известняка для формирования цемента, но для придания ему твердости требовался другой материал. Смешивание только оксида магния с водой не поможет — смесь станет слякотной. И ему нужно было найти источник оксида магния, который бы не выделял столько углекислого газа. Класс материала, на котором он остановился, — это силикаты магния, не содержащие углерода соединения, полученные из талька, серпентина, оливина или других минералов.Мировые запасы этих полезных ископаемых составляют около 10 миллиардов тонн, что является важным фактором, потому что, если у кого-то закончится мука, больше нельзя будет испечь пирогов.
Власопулос не очень хочет объяснять, как работает его экспериментальный состав. Его секретный соус, возможно, очень прибыльный секрет. Зарегистрировано несколько патентов. Он многое расскажет: несколько лет назад он начал смешивать оксид магния с другими созданными им химическими соединениями и водой. Смесь затвердела в маленький шарик. Он принес его в офис Чизмана.«Можно было почувствовать жар, исходящий от этого маленького шарика, — сказал Чизман. — Что-то явно происходило. Химические реакции шли огнем; энергия высвобождалась. Они не слишком возбуждались. «Я имею в виду, что мы говорим о цементе — это не самая сексуальная вещь в мире», — сказал Чизман. «Я не бегал туда-сюда по коридорам, крутя колеса, но это было интересно».
Химические вещества, которые Власопулос смешивает с оксидом магния и водой для затвердевания цемента, представляют собой карбонаты магния, которые он производит путем добавления углекислого газа к другому сырью.Это означает, что в некоторых сценариях цемент не просто углеродно-нейтрален, он углеродно-отрицательный. На каждую тонну произведенного Власопулосом цемента может быть поглощена одна десятая тонны углекислого газа.
В конце концов Власопулос с помощью Чизмана основал компанию Novacem для разработки нового цемента. Фирма с более чем дюжиной сотрудников и партнерскими отношениями с некоторыми из крупнейших цементных компаний мира расположена в бизнес-инкубаторе для высокотехнологичных стартапов Имперского колледжа.В то время как некоторые другие компании на объекте являются стартапами в области наук о жизни, с микробиологическими лабораториями, полными машин для секвенирования генов и коллекций пробирок, лаборатория Novacem представляет собой просторный завод, который производит громкие звуки, много пыли и ведро за ведром цемента. Это первый цементный завод в центре Лондона со времен римлян.
Рабочие в касках, защитных очках, масках и белых лабораторных халатах работают на миниатюрной версии цементного завода, мало чем отличающегося от того, на котором Власопулос работал во время летних каникул.
Несмотря на то, что Novacem все еще совершенствует свои процедуры, он соревнуется по крайней мере с пятью другими компаниями и университетскими центрами, чтобы придумать более экологичный цемент. «Учитывая все внимание к углероду в наши дни, появилось много предпринимателей», — сказал Дженнингс из Массачусетского технологического института. «Они видят сторону возможностей». Поскольку производство цемента приносит 170 миллиардов долларов в год, инвестиции в него текут рекой.
Калифорнийская компания Calera использует, пожалуй, самый необычный подход: она использует углекислый газ, выбрасываемый электростанцией, и смешивает его с морской водой или рассолом для создания карбонатов, которые используются для производства цемента.Их можно добавлять в портландцемент, чтобы заменить часть или весь известняк. Calera поддерживается инвестициями в размере 50 миллионов долларов от Винода Хосла, компьютерного инженера, который, возможно, является самым уважаемым и богатым инвестором в «зеленые» технологии в Силиконовой долине. «На самом деле мы производим наш цемент из CO2», — сказал основатель компании Брент Констанц. «Мы берем CO2, который попал бы в атмосферу, и превращаем его в цемент». Технология все еще находится в разработке: демонстрационный завод в Мосс-Лендинге, Калифорния, и партнерство с китайской группой по строительству завода рядом с угольной шахтой во Внутренней Монголии, где они планируют использовать выбросы углекислого газа для производства цемента.
Calix, австралийская компания, производит цемент с использованием перегретого пара, который модифицирует частицы цемента и делает их более чистыми и химически активными. Этот процесс также выделяет углекислый газ, что упрощает его улавливание и не допускает попадания в атмосферу.
Технический университет Луизианы, как и Novacem и Calera, полностью отказывается от известняка; он использует пасту под названием геополимер, которая состоит из летучей золы, гидроксида натрия и гидроксида калия.
«В конце концов пыль уляжется, и одна из этих идей сработает», — сказал Дженнингс.
Вначале одним из самых больших скептиков Novacem была крупнейшая частная строительная компания Великобритании Laing O’Rourke. Руководитель, отвечающий за отслеживание многообещающих университетских работ, Дирадж Бхардвадж, узнал о продукте Novacem благодаря своим научным связям. Он посмотрел на химию, подумал, что все проверено, и несколько лет назад представил эту идею председателю, у которого было много сомнений.По его словам, цемент никак не мог быть достаточно прочным для коммерческого использования. Нужен известняк. Когда материал Novacem достигнет 40 мегапаскалей — минимального количества прочности, необходимого для структурной стабильности — тогда он может заинтересоваться.
Семь дней спустя небольшой кусок цемента Novacem, помещенный в инструмент, похожий на тиски, попал в эту отметку. Двадцать восемь дней спустя он достиг 60 мегапаскалей. Затем Бхардвадж передал результаты председателю, который сказал: «Давайте сделаем это». Laing O’Rourke теперь является крупным партнером Novacem. Сегодня, после долгих доработок, цемент приближается к 80 мегапаскалям. Бетон, изготовленный из цемента Novacem, по прочности сравним с некоторыми стандартными бетонами.
Другими партнерами Novacem являются Lafarge в Париже, крупнейший в мире производитель строительных материалов, и Rio Tinto, глобальная горнодобывающая компания со штаб-квартирой в Лондоне, стремящаяся помочь Novacem в добыче силикатов магния.
«Сейчас цементная промышленность набирает обороты в финансовом и научном отношении», — сказал Дженнингс, имея в виду все различные экспериментальные подходы.«Мир меняется. Все, включая все цементные компании, должны быть как можно более экологичными и немного лучше заботиться о мире».
Дженнингс отказался одобрить какой-либо конкретный новый цемент. «Если Novacem работает, — сказал он, — это очень привлекательная идея».
Бхардвадж более предан делу. Он сказал, что недавно ходил к своей команде инженеров. «Честно говоря, не будьте вежливы», — сказал он им. «Отложите любые вопросы об углероде. Как вы думаете, это что-то близкое к портландцементу?» Ответ удивил его: они сказали, что так лучше.Почему? Он был не только сильным, но и чисто белым. Портландцемент имеет слегка серый цвет. «Вы можете добавить красок в этот цемент», — сказал Бхардвадж. «Представьте, что в вашем доме есть цементная стена любого цвета, который вы хотели».
Цемент приятного белого оттенка, как отметил Власопулос, демонстрируя прототип цементного завода своей компании. Говоря о соседних биологических лабораториях, он сказал: «Мы громче», добавив: «Там лечат людей; мы лечим что-то другое». Неповоротливая машина перед ним, в данный момент простаивающая, имеет длинные трубы, которые грохочут и лязгают, срабатывает сигнализация и миксеры, которые взбивают и выплевывают ведра творения Власопулоса.
Власопулос был в приподнятом настроении, накануне сделав предложение своей девушке. (Она сказала «да».) В углу комнаты располагалось то, что он называл «нашим музеем». На маленьком столике лежали первые куски цемента Novacem — они выглядели как детские кубики, только более пыльные. «Это было не так уж хорошо», — сказал он, поднимая хрупкую на вид треснувшую. — Теперь мы знаем, что делаем. Завод может производить около пяти тонн цемента в год. Компания также работает над другим объектом, который будет производить 200 тонн в год.Если все пойдет хорошо, компания намерена предоставить лицензию на свой рецепт производителям цемента по всему миру.
Главным препятствием, которое еще предстоит преодолеть компании, является история. Портландцемент работает . Так было всегда, с того дня в 1824 году на кухне Джозефа Аспдина. «Цемент существует уже очень давно, — сказал Бхардвадж. «Люди этому верят. Они могут окинуть взглядом все постройки, пережившие сотни лет. Так что для Novacem доказательство долговечности потребует времени. Им придется идти медленно.Если мне нужно построить мост или здание с использованием цемента Novacem, как мне убедить людей, что это нормально? Это вызов. Никто не хочет, чтобы мост рухнул».
На вопрос, пойдет ли он по мосту, построенному из цемента Novacem, Бхардвадж ответил: «У меня с этим проблем не будет». Но этот мост еще не построен.
Майкл Розенвальд написал о нанотехнологиях и охотниках за гриппом для Smithsonian . Джон Риттер живет в Пенсильвании.
Николаос Власопулос мечтает разработать новый материал, производство которого, в отличие от традиционного цемента, поглощает углекислого газа. В случае успеха он поможет уменьшить основной фактор изменения климата и претендует на смелый шаг вперед в области строительных технологий.Джон Риттер Пилотный завод Novacem — первый цементный завод в центре Лондона со времен Римской империи..jpg)
Рекомендуемые видео
Как цемент еще может помочь замедлить глобальное потепление
T HE ROMANS усовершенствованный бетон, и их наследие до сих пор сохранилось в виде великолепной крыши Пантеона, самого большого в мире неармированного бетонного купола.С тех пор, как он был завершен примерно в 125 году года нашей эры императором Адрианом, было залито намного больше бетона — около 30 миллиардов тонн ежегодно, на данный момент, для возведения зданий, дорог, мостов, плотин и других сооружений. Серый материал стал самым широко используемым строительным материалом на планете, и спрос на него растет.
Послушайте эту историюВаш браузер не поддерживает элемент
Наслаждайтесь большим количеством аудио и подкастов на iOS или Android.
Это плохие новости для глобального потепления.Проблема в том, что важнейший компонент бетона, цемент, который смешивают с песком, гравием и водой, ответственен за огромное количество выбросов парниковых газов. Принимая во внимание различные этапы производства, 5 миллиардов тонн цемента, производимого каждый год, составляют 8% мировых антропогенных выбросов CO 2 . Если бы цементная промышленность была страной, она была бы третьим по величине источником выбросов в мире после Китая и Америки.
Пока у бетона мало практических альтернатив.Разработка кросс-ламинированной, «инженерной» древесины, которая, будучи произведенной из древесины, может быть возобновляемым ресурсом, вызывает интерес даже для некоторых высотных зданий. Но по сравнению с бетоном инженерная древесина пока остается новинкой. Крупнейшие потребители бетона, особенно Китай, производящий более половины цемента в мире, не собираются прекращать его использование. Следовательно, очистка отрасли может показаться безнадежной задачей. Но это не так, поскольку разрабатываются технологии, позволяющие сделать бетон более экологичным.Возможно, достаточно зеленый, чтобы перейти от добавления CO 2 в атмосферу к его вычитанию.
Начать следует с места, где больше всего выбросов. Производство цемента начинается с добычи известняка, основным компонентом которого является карбонат кальция (CaCO 3 ). Его смешивают с глиной и пропускают через вращающуюся печь при температуре более 1400ºC в процессе, называемом прокаливанием. Тепло удаляет углерод и часть кислорода, которые объединяются, образуя CO 2 .Остальные куски, называемые клинкером, состоят из молекулярных комплексов оксида кальция и кремнезема, известных под общим названием силикаты кальция. Затем клинкер охлаждают и перемалывают в цемент. Более половины выбросов, связанных с производством цемента, являются следствием кальцинирования, а большая часть остальных – результатом сжигания угля и других ископаемых видов топлива для обеспечения процесса (см. диаграмму). В целом на каждую тонну свежего цемента выделяется почти одна тонна CO 2 . По данным исследования Пола Феннелла из Имперский колледж в Лондоне и его коллеги, опубликованные ранее в этом году в Джоулей. Захваченный CO 2 может храниться под землей или использоваться в других отраслях, например, для производства синтетического топлива (см. статью). Но его также можно вводить обратно в бетон в тот момент, когда он смешивается с водой для отверждения. Вода способствует химическим реакциям, в результате которых цемент затвердевает. CO 2 имеет аналогичный эффект и в процессе запирается в виде карбоната кальция.
На самом деле, реверсивное прокаливание таким образом делает бетон более прочным, чем если бы использовалась только вода.Таким образом, не только устраняется часть первоначальных выбросов, но и требуется меньше цемента для данной работы, что еще больше снижает общие выбросы. McKinsey, консалтинговая компания, считает, что обратное кальцинирование в настоящее время может улавливать до 5% выбросов цемента. Ожидается, что по мере совершенствования технологии этот показатель может возрасти до 30%.
Несколько компаний начинают движение по этому маршруту. Канадская фирма CarbonCure установила оборудование для впрыска CO 2 в товарный бетон на более чем 400 заводах по всему миру.Его система использовалась для строительства зданий, в том числе нового кампуса в Арлингтоне, штат Вирджиния, для Amazon, интернет-магазина (а также акционера CarbonCure) и завода по сборке электромобилей для General Motors в Спринг-Хилл, штат Теннесси. .
В настоящее время CO 2 , используемый CarbonCure, перехвачен компаниями, производящими промышленные газы. Но фирмы разрабатывают оборудование, предназначенное для сбора газа непосредственно из цементных печей. А компания Calix, базирующаяся в Сиднее, Австралия, работает над системой с электрическим приводом, которая косвенно нагревает известняк снаружи печи, а не внутри.Это позволяет улавливать чистый CO 2 без необходимости очистки дымовых газов от топлива, сжигаемого внутри печи, поэтому, если само электричество поступает из экологически чистых источников, полученный цемент будет полностью зеленым.
Пилотный завод, использующий эту технологию, успешно работает в рамках исследовательского проекта Европейского Союза на площадке в Бельгии, управляемой Heidelberg Cement, немецкой фирмой, которая является одним из крупнейших в мире производителей цемента. Более крупный демонстрационный завод должен открыться в 2023 году в Ганновере, чтобы помочь масштабировать технологию.
Энергетический мусор
Другой подход — менее экологичный, но все же лучше, чем использование ископаемого топлива, — заменить часть сжигаемого в печах угля бытовыми и промышленными отходами. Несколько фирм уже этим занимаются. Cemex, мексиканский гигант по производству строительных материалов, например, производит топливо для печей под названием Climafuel из бытовых отходов, очищенных от перерабатываемых веществ. Он богат в виде растительного материала («биомасса») углеродом, который недавно был в атмосфере и просто возвращается туда, а не был выкопан в качестве ископаемого топлива.До 60% угля, используемого некоторыми британскими цементными заводами Cemex, было заменено на Climafuel.
Компании также ищут способы заменить часть цемента в бетоне другими материалами. Многие добавляют летучую золу, побочный продукт угольных электростанций, или дробленый шлак из доменных печей, используемых для производства чугуна. Но ни один из этих подходов не является устойчивым в долгосрочной перспективе. Как отмечает Питер Харроп, руководитель ID TechEx, аналитической фирмы в Кембридже, Англия, и соавтор нового отчета о будущем бетона и цемента, использование угля сокращается, а производство стали стремится перейти на более новые, чистые технологии.
По мнению доктора Харропа, важной частью ответа является «технологическое усовершенствование» бетона таким образом, чтобы его меньше требовалось для выполнения определенных работ. Это означает добавление таких вещей, как синтетические и натуральные волокна или даже графен, вещество, более прочное, чем сталь, которое состоит из однослойных слоев атомов углерода. Для получения положительных результатов необходимы лишь небольшие количества.
Графен и другие армирующие материалы позволят получить новые сверхвысококачественные бетоны, которые, по мнению доктора Харропа, будут особенно подходящими для печати 3 D .Это создает точные слои материала под контролем робота и значительно снижает количество отходов. «Использование гораздо меньшего количества цемента — очень важная часть ответа», — добавляет он, тем более что производство цемента, по всей видимости, удвоится в течение следующих 20 лет.
Добавки также могут увеличить срок службы бетона и снизить потребность в техническом обслуживании. В Мичиганском университете Виктор Ли и его коллеги используют синтетические и натуральные волокна вместе с инъекцией CO 2 для производства гибкого бетона, который они называют Engineered Cementitious Composite ( ECC ).Внутренняя структура этого материала была вдохновлена перламутром, гибким материалом, обычно называемым «перламутром», который покрывает внутреннюю часть раковин моллюсков, таких как морские ушки и устрицы.
Придание бетону такой гибкости позволяет мостам и дорогам легче справляться с интенсивным движением и повышает сейсмостойкость высотных зданий. ECC по мере старения образует только крошечные поверхностные трещины. Доктор Ли говорит, что таким образом лучше удерживает воду и предотвращает коррозию стальных арматурных стержней внутри.Такая коррозия может привести к разрушению железобетонных конструкций в течение нескольких лет после их возведения, что иногда приводит к их разрушению.
До нуля и выше
Замена материалов может пойти еще дальше. Solidia, фирма в Нью-Джерси, производит цемент, содержащий силикаты кальция с более высоким соотношением кремнезема и оксида кальция, чем стандартный «портлендский» сорт. Это имеет два последствия. Во-первых, процесс Solidia требует меньше тепла (и, следовательно, меньше ископаемого топлива), чем обычное прокаливание, и поэтому, во-первых, выделяется меньше CO 2 .Во-вторых, при смешивании с бетоном силикаты Solidia, богатые кремнеземом, могут затвердевать быстрее, чем обычный цемент, за счет использования уловленного CO 2 вместо воды. Solidia работает над заявками на свой цемент с одним из своих инвесторов, LafargeHolcim, швейцарским гигантом строительных материалов.
Принимая во внимание все эти разработки, насколько зеленым может стать бетон? Д-р Феннелл говорит, что было бы достаточно легко сократить выбросы CO 2 в отрасли примерно до 80% от нынешних уровней на тонну производимого бетона за счет более эффективного использования энергии и модификации материалов.Но компании действительно могли бы выйти из-под контроля, если бы они перешли на печи, работающие в основном или полностью на биомассе, такой как древесина. Углерод в нем до недавнего времени был бы CO 2 в воздухе. Если бы после того, как он снова превратился в этот газ при сжигании в печи, он был бы сохранен и не высвобожден, следствием того, что новые деревья выросли бы вместо потребленных, был бы чистый поток углерода из атмосферы.
Такого рода система, называемая биоэнергетикой с улавливанием и хранением углерода ( BECCS ), является одним из способов, который разработчики моделей климата представляют себе для обеспечения «отрицательных выбросов», необходимых для нулевых или чистых отрицательных выбросов. Часто говорят о выработке электроэнергии на основе BECCS , но BECCS на самом деле может лучше подходить для производства цемента, потому что в мире, заботящемся об углероде, оборудование для улавливания CO 2 уже будет там, имея дело с результатами прокаливания. . И если бы это произошло, один из парий глобального потепления мог бы таким образом искупить свою вину, помогая смягчить ущерб, наносимый планете, и таким образом оставить после себя столь же впечатляющее наследие, как и наследие римлян. ■
Для получения более подробной информации об изменении климата зарегистрируйтесь в The Climate Issue, нашем двухнедельном информационном бюллетене, или посетите наш центр изменения климата
Любопытный мир? Чтобы получать удовольствие от нашего расширяющего кругозор научного освещения, подпишитесь на нашу еженедельную рассылку Simply Science.
Ранняя версия этой статьи была опубликована в Интернете 2 ноября 2021 г.
Эта статья появилась в разделе «Наука и технологии» печатного издания под заголовком «Установка в зеленый бетон»
LafargeHolcim в США — Цемент , бетон, заполнители
Чикаго, Иллинойс, 1 декабря 2021 г. – Сегодня компания LafargeHolcim в США представила новый продукт ECOPlanet, TerCem™, цемент со сверхнизким углеродным следом. TerCem, трехкомпонентная цементная смесь, обеспечивает сокращение выбросов CO2 до 65%.Специально разработанный на нашем цементном заводе Lafarge Whitehall в Пенсильвании, он обеспечивает улучшенные характеристики ранней прочности бетона, которые производители готовых смесей не могут воспроизвести даже при использовании дорогих добавок.
Поскольку Соединенные Штаты удваивают свои обязательства по снижению углеродного следа застроенной среды и улучшению национальной инфраструктуры, цементные продукты ECOPlanet вместе с TerCem позволят масштабировать низкоуглеродное строительство. TerCem был разработан для строительного сектора и конструкций из бетона с натяжением в городских районах, с потенциалом для использования во многих областях, где требуется низкий углеродный след.
«Мы возглавляем трансформацию рынка и делаем шаг к будущему с нулевыми выбросами», — сказал Патрик Клири, старший вице-президент по продажам цемента в США в LafargeHolcim. «Наша компания по производству цемента вложила значительные средства в расширение ассортимента экологически чистых продуктов высшего качества, предназначенных для снижения нашего углеродного следа без ущерба для качества и долговечности».
Ассортимент продуктов ECOPlanet обеспечивает минимальный углеродный след на 30% по сравнению со стандартными цементами за счет использования инновационного сырья с низким уровнем выбросов и широкого использования альтернативных видов топлива в производственном процессе.
Завод Lafarge Whitehall, один из старейших действующих цементных заводов в США, долгое время был инновационным центром низкоуглеродных продуктов и решений, включая цемент Solidia.
Внедрение ECOPlanet в США является важным шагом в национальных усилиях по совершенствованию физической инфраструктуры и поддержке улучшений, которые стимулируют экономику и создают рабочие места, а также способствуют созданию более «зеленых» городов и «умной» инфраструктуры.
###
О Holcim
Holcim способствует прогрессу для людей и планеты.Являясь мировым лидером в области инновационных и экологичных строительных решений, Holcim делает города более экологичными, создает более интеллектуальную инфраструктуру и повышает уровень жизни во всем мире. С учетом устойчивого развития в основе своей стратегии Holcim становится компанией с нулевым уровнем выбросов, в основе успеха которой лежат ее сотрудники и сообщества. Компания продвигает экономику замкнутого цикла как мировой лидер в области вторичной переработки, чтобы строить больше с меньшими затратами. Holcim является компанией, стоящей за некоторыми из самых надежных мировых брендов в строительном секторе, включая ACC, Aggregate Industries, Ambuja Cement, Disense, Firestone Building Products, Geocycle, Holcim и Lafarge. Holcim — это 70 000 человек по всему миру, которые увлечены достижением прогресса для людей и планеты в четырех бизнес-сегментах: цемент, товарный бетон, заполнители и решения и продукты. Более подробная информация доступна на сайте www.Holcim.com.
В Соединенных Штатах LafargeHolcim в США, дочерняя компания Holcim, включает около 350 площадок в 43 штатах и насчитывает 7000 человек. Наши клиенты полагаются на нас, когда мы помогаем им проектировать и строить лучшие сообщества с помощью инновационных решений, обеспечивающих структурную целостность и экологическую эффективность.
Контакт
Джоселин Герст
Тел.: +1 (773) 355-4701
Электронная почта: jocelyn.gerst@lafargeholcim.com
Влияние степени заполнения цементом на расшатывание тазобедренных имплантатов
Биоматерия. 1 апреля 2012 г .; 2(2): 87–93.
Биомедицинская, промышленная и инженерная инженерия человеческого фактора; Государственный университет Райта; Dayton, OH USA
Это статья с открытым доступом под лицензией Creative Commons Attribution-NonCommercial 3. 0 Unported License. Статья может распространяться, воспроизводиться и повторно использоваться в некоммерческих целях при условии правильной ссылки на первоисточник.
Abstract
Расшатывание бедренной кости является одной из наиболее частых причин ревизионных ортопедических операций. Толщина цементной мантии прямо коррелирует с расшатыванием бедренной кости. Если мантия слишком толстая, существует повышенный риск появления рентгенопрозрачных линий и непостоянной плотности. Кроме того, большее количество кости, рассверливаемой во время процедуры, может привести к нестабильности, особенно если качество кости нарушено из-за остеопороза.Слишком тонкая мантия может привести к более высокой вероятности разрушения цемента, что приведет к еще большему ослаблению протеза. Это исследование показало, что существует идеальный диапазон толщины от двух до пяти, который следует соблюдать. По рентгенографическим изображениям можно измерить толщину цементного чехла, показывающую характеристики разрыхления.
Ключевые слова: цемент, бедренный стержень, коэффициент заполнения, тазобедренный имплантат, расшатывание
Введение
Интерфейс цемент-ножка является наиболее распространенным местом, где происходит расшатывание бедренной кости.Это происходит из-за несоответствия материалов и механических свойств на границе раздела, на которую воздействуют колебательные силы во время повседневной деятельности. Именно здесь, где происходит истирание, повторяющиеся относительные движения вызывают деформацию как поверхности стержня, так и более хрупкого цемента. Усталостные бороздки на поверхности трещин показывают, что трещины в цементной оболочке возникли из-за усталостной нагрузки в течение длительного периода времени. 1 Окружные факторы и радиально ориентированные факторы обычно связаны с отслоением цемента от ствола. 1 Такие факторы, как метод цементирования и размер ножки, также влияют на расшатывание бедренного компонента. Достижения в технологии цементирования и улучшенная конструкция ствола снизили скорость рыхления. 2 Большинство трещин в цементной оболочке возникают из-за пор в костном цементе, что приводит к расшатыванию протеза. Метод цементирования, такой как вакуумное смешивание, уменьшает площадь пор на 70–80% по сравнению с невакуумным смешиванием. 3 Было замечено, что с увеличением глубины проникновения также увеличиваются напряжения в соединении кость/костный цемент.Глубина проникновения 2,2–2,9 мм достаточна для достижения начальной стабильности и позволяет избежать значительной потери кости. 4
В тонких образцах наблюдалось ослабление из-за увеличения индуцируемых движений с течением времени, тогда как в толстых образцах индуцируемые движения со временем уменьшались. Хотя средняя длина трещины в обоих случаях сопоставима, на поверхности тонкого образца наблюдался внезапный рост трещины, тогда как на поверхности толстого образца наблюдался стабильный рост трещины. 5 Таким образом, толщина цементного слоя играет эффективную роль в расшатывании протеза тазобедренного сустава. Появление тонкой мантии может быть уменьшено за счет анатомической конструкции ствола и низкого коэффициента раскрытия канала. Использование центраторов показало риск образования тонкой цементной мантии в зонах Груена 8 и 9 (см. , где были выявлены изношенные участки) из-за выталкивания ножки вперед. 6 Толщина цемента влияет не только на напряжение, но и на микродвижение. Толщина цемента 2 мм увеличила напряжение сдвига проксимально и показала микроподвижность на границе цемент-кость. Увеличение толщины более 7 мм показало проскальзывание на границе цемент-кость.Максимальные значения микроотслоения и сжимающего напряжения на различных границах раздела, связанные с толщиной цементного чехла, показаны на и . Отмечено, что оптимальная толщина цемента находится в диапазоне от 3 до 5 мм. 7 При увеличении толщины цементной оболочки с 2,4 мм до 3,7 мм осевые деформации уменьшились на 40 % в дистально-латеральном цементе и на 49 % в дистально-медиальном цементе вдоль ножки бедренной кости при осевой нагрузке 1400 Н.
8 Измеряя толщину цемента и рентгенопрозрачные линии на рентгеновских снимках, можно получить информацию о резорбции кости после имплантации.Собирая эти данные по множеству разных пациентов, можно провести количественную оценку и анализ того, какое соотношение цементной оболочки обеспечивает наилучшее соответствие.
Таблица 1. Открытие зоны износа износа на каждой Грюнской зоны ствола поверхности
9036
0
Стебель поверхности | Ansiory | Медиальный | Боковые | |||||
---|---|---|---|---|---|---|---|---|
Зона 1 | 0 | 60 | 10 | |||||
Зона 2 | 20 | 20 | 90 | |||||
Зона 3 | ||||||||
30 | 30 | 0 9 | 9 | |||||
Zone 4 | 0 | 0 | 0 | 0 | 0 | |||
5 | 10 | 10 | 0 | 9032 9 | ||||
Зона 6 | 30 | 30 | 80329 | 10 | ||||
Zone 7 | 10 |
Рисунок 1. Рисунок, показывающий отслоение на различных границах раздела по отношению к толщине цементного слоя. 7
Рисунок 2. Рисунок, показывающий сжимающее напряжение на различных границах раздела по отношению к толщине цементного слоя. 7
Результаты
Учитывая, что идеальная толщина цемента, окружающего ножку бедренной кости, составляет 2–5 мм, а диаметр ножки бедренной кости составляет 12,7 мм, можно рассчитать следующие соотношения: , R A Была полная развернутая поверхность, которая равна: R A = 2 * Толщина цемента + T S
; Эту процедуру повторяли для диапазона толщины цемента от 1 до 7 мм с шагом в одну десятую миллиметра.Соответствующее уменьшение можно увидеть на , которое показывает, что по мере увеличения толщины коэффициент заполнения цементом уменьшается экспоненциально по уравнению: y = 0,92e — 0,098x . Для идеального случая толщины мантии от 2 до 5 мм коэффициент заполнения должен находиться в диапазоне 0,56–0,76.
Рисунок 3. Соотношение заполнения цементом по отношению к толщине мантии при диаметре бедренного стержня 12,7 мм.
Три случая были проанализированы с использованием набора конечных элементов ANSYS V11 sp1 x64.В первой использовалась установка, включающая минимальный коэффициент заполнения 0,86, что соответствует толщине мантии 1 мм. Другие тесты проводились при соотношениях 0,68 и 0,48 соответственно. Проблема была упрощена за счет исключения компонентов головки и шейки бедра, а статический анализ был выполнен путем приложения эквивалентной нагрузки к ножке бедра. Эта нагрузка состояла из двух компонентов: вертикальной силы -2500 Н, а также момента 62500 Н·мм, чтобы воспроизвести поведение вертикальной нагрузки со смещением. Путем создания сетки ствола и поверхности цемента в форме шестиугольного кирпича был выполнен более точный анализ методом конечных элементов. 9 Упрощенный анализ силы показан на (слева). Было обнаружено, что это напрямую коррелирует с величиной отклонения мантии, наблюдаемой под нагрузкой, как показано в правом столбце (справа).
Рисунок 4. Слева вверху вниз показаны эквивалентные напряжения, приложенные только к цементной оболочке, а справа вниз показаны прогибы, приложенные как к мантии, так и к бедренному стержню. Верхний ряд рисунков соответствует толщине мантии 1 мм, ниже — 3 мм, ниже — 5 мм.
Дальнейшее исследование напряжений, показанных в цементном материале, можно увидеть в левой колонке . При толщине мантии 1 мм напряжения наблюдаются около 9 МПа на границе кости и цемента. Следует отметить, что прогибы, изображенные в правой колонке рисунка, показаны визуально увеличенными в 15 раз, но прогибы, показанные в цементе, напрямую коррелируют с величиной прогиба, показанной в стержне, из-за более мягкого материала. характеристики цемента.
Рентгенографический анализ
Одним из наиболее распространенных методов измерения толщины цементной оболочки in vivo является рентгенография имплантата с разных точек зрения. 10 Важно убедиться, что оба увеличения на рентгенограммах одинаковы, чтобы обеспечить правильное чтение. Если увеличения не совпадают, это можно исправить с помощью поправочного коэффициента. В этом случае боковой вид имплантата имел другое увеличение, чем вид спереди.Измерив длину бедренного стержня, сделали вывод, что длины различались от 21,5 см до 20,0 см. Взяв отношение двух длин, мы нашли поправочный коэффициент 1,075.
Толщина была измерена от проксимального конца до дистального конца на рентгенограммах каждой из видимых бороздок, которые соответствовали кости, толщине цемента, имплантату, толщине цемента и кости в поперечном сечении, как показано на . Первые несколько измерений были отброшены из-за невозможности определить, где расположены границы раздела материалов.Каждое из измерений бокового вида затем нужно было скорректировать с помощью поправочного коэффициента, чтобы оно было более совпадающим при сравнении двух пленок. Рентгенологические измерения в боковой проекции и передней проекции были записаны в и . FG — диаметр ножки бедренной кости, EH — диаметр рассверленного канала. Согласно ранее рассмотренным расчетам, идеальный коэффициент заполнения бедренного имплантата цементом должен составлять от 0,56 до 0,76.
Рисунок 5. Рентгеновское изображение тазобедренного имплантата, используемое для определения коэффициента заполнения.
Таблица 2. Радиографические измерения от бокового просмотра
Таблица 3.

FG | |||||
---|---|---|---|---|---|
FG | EH | Коэффициент заполнения | |||
17.![]() | 26.9 | 0.640 | 6 | ||
16.1 | 16.1 | 25.8 | 0.625 | ||
15.1 | 25.8 | 0.583 | |||
12,9 | 24,2 | 0,533 | |||
12,9 | 25,8 | 0,500 | |||
12,4 | 22,6 | 0,548 | |||
11,8 | 29.![]() | 22.0 | 0.537 | ||
10.8 | 10.8 | 21,5 | 0.500 | ||
10.2 | 21.0 | 0,487 | |||
9.7 | 21,0 | 0,462 | |||
8,6 | 18,8 | 0,457 | |||
8,6 | 19,4 | 0,444 | |||
70304 | 7030306 | 18.![]() | 0.412 | ||
7.5 | 19.4 | 19.4 | 0.389 | ||
6.5 | 19.9 | 0.324 | |||
6.5 | 20.4 | 0.316 |
6 10.5
Radiograph 1 | |||||
---|---|---|---|---|---|
FG | EH | EH | Коэффициент заполнения | ||
18,0 | 24,0 | 24,0 | 0.750 | ||
16.![]() | 22,5 | 0,711 | |||
15,0 | 20,5 | 0,732 | |||
15,0 | 21,0 | 0,714 | |||
13,0 | 18,0 | 0.722 | |||
13.030304 | 13.![]() | 18.0 | 18.0 | 0.722 | |
17,5 | 0.686 | ||||
12.0 | 19,0 | 0,632 | |||
12,0 | 18,0 | 0,667 | |||
11,5 | 17,5 | 0,657 | |||
11,0 | 16,5 | 0.![]() | 6 | ||
11.0 | 11.0 | 18.0 | 0.611 | ||
18.59 | 0.568 | ||||
10.0 | 18,0 | 0,556 | |||
10,0 | 17,0 | 0,588 | |||
9,5 | 19,0 | 0,500 | |||
7,0 | 16,0 | 0,438 |
Вид спереди показывает, что большинство значений попадают в этот диапазон, за исключением дальнего дистального конца имплантата. Однако боковой вид имплантата показывает, что коэффициент заполнения значительно ниже идеального, за исключением того, что он находится в минимальном диапазоне в верхней части имплантата.Это также коррелирует с толщиной цементной мантии передней и задней сторон на латеральном виде, где цемент на передней стороне имплантата был значительно тоньше, чем хотелось бы.
Рисунок 6. (A) Передние рентгенографические данные, где была записана толщина цемента в зависимости от положения как для латеральной, так и для медиальной сторон. (B) Боковые рентгенографические данные, где толщина цемента была записана в зависимости от положения как для задней, так и для передней сторон.
Каждый из коэффициентов заполнения был затем рассчитан из рентгенографических данных по уравнению:
Затем данные были нанесены на и .Поскольку толщина ножки не одинакова по всему имплантату, как предполагалось в предыдущем исследовании, ожидается, что коэффициент заполнения уменьшится по мере уменьшения толщины ножки. Это можно увидеть в том месте, где предполагаемая мантия толщиной 3 мм окружала фактический стержень бедренной кости, что соответствует ранее упомянутым пределам коэффициента заполнения 0,56–0,76, что находится чуть ниже диапазона в конце. показывает, что диаметр ствола линейно коррелирует с коэффициентом заполнения цементом. Таким образом, по мере увеличения диаметра ствола коэффициент заполнения цементом уменьшается, если предположить, что толщина цементного слоя составляет 3 мм с каждой стороны, он будет уменьшаться по следующему уравнению: Коэффициент заполнения (F.R.) = -0,0146(T s ) + 0,7697 Также, сравнивая толщину мантии с коэффициентом заполнения, можно вывести следующее уравнение, где T m — толщина мантии: Коэффициент заполнения (FR) = 0,92e -0,098*Tm
Рисунок 8. Коэффициент заполнения , построенный в зависимости от положения переднего коэффициента заполнения.
Рисунок 9. Идеальный коэффициент заполнения в зависимости от толщины штока.
Обсуждение
Эксперименты 5 , 8 показали, что тонкая цементная оболочка является одной из наиболее важных причин отказа имплантата. В этом исследовании были исследованы три различных сценария толщины цементного слоя с толщиной слоя 1 мм, 3 мм и 5 мм, при этом исследованное значение идеальной толщины цементного слоя должно составлять от двух до пяти миллиметров. Было обнаружено, что коэффициент заполнения находится в пределах 0,56–0,76, что напрямую зависит как от площади рассверливания, так и от диаметра ножки бедренной кости.Коэффициент заполнения цементом по отношению к толщине мантии показан в виде экспоненциальной зависимости y = 0,92e -0,098x . Из него видно, что с увеличением толщины цементного чехла коэффициент заполнения уменьшается. По рентгенографическому анализу расчетный коэффициент заполнения из данного допустимого диапазона толщины цемента был на одном уровне с тем, что видно на пленке с одного ракурса. Однако из и коэффициенты заполнения были слишком низкими по отношению к дистальным измерениям с уменьшением диаметра бедренного стержня при боковой проекции.Это показывает, что толщина цементного чехла велика по направлению к дистальному участку. Та же тенденция к уменьшению коэффициента заполнения наблюдается при передней проекции. показывает напряжения, приложенные к цементной оболочке, которые показывают увеличение распределения напряжений с увеличением толщины и снижением деформации. Эквивалентное напряжение по Мизесу варьировалось от 24,6 МПа при толщине мантии 1 мм до 17,9 МПа при толщине мантии 5 мм. Максимальная деформация варьировалась от 0,03 мм до 0,06 мм при толщине мантии 1 мм и 5 мм соответственно.Это показано в том, что C1 намного больше, чем C2, но значительно тоньше, чем соответствующие измерения в .
Материалы и методы
В стандарте ISO 7206–4:2002 описан метод испытаний, в котором описывается, как следует прикладывать циклическую нагрузку к головке штока, погруженного в твердую среду, как показано на рис. Образец следует также внимательно осмотреть на наличие любых дефектов, вызванных его загрузкой на испытательную машину. Испытательная машина должна иметь приложенную погрешность не более ± 2% от максимальной приложенной нагрузки.Сам бедренный стержень должен быть установлен под углом 9° ± 1 при сгибании, что соответствует углу β в . Угол α должен составлять 10 ° ± 1 при аддукции, что также показано на рис. Эти углы помещают имплантат в более эргономичное положение, что позволяет сопоставить результаты испытаний in vitro и in vivo. Нагрузка должна составлять от 300 до 2300 Н в форме синусоиды, чтобы примерно в три раза превышать среднюю массу тела.
Рисунок 10. Общая ориентация испытуемого образца в соответствии со стандартом ISO 7206–4:2002 (E).
Рисунок 11. Ориентация образца для испытаний по ISO 7206–4:2002 (E).
Экспериментальный проект
Были созданы три различных сценария толщины цементной корки. Тонкая оболочка имела постоянную толщину 1 мм, а также цементная оболочка толщиной 3 мм, что соответствовало желаемой толщине, указанной в нескольких лабораторных исследованиях. 7 Более толстая конструкция была создана с мантией толщиной 5 мм. Для простоты каждая модель была спроектирована как колонна из цементной оболочки из ПММА, которая вставлялась в соответствующий держатель из нержавеющей стали.Затем имплантат был помещен в мантию, достигая середины бедренного стержня. Каждый из этих случаев показан на рис. Если предположить, что диаметр имплантата, а также рассверленная бедренная полость были постоянными на протяжении каждого эксперимента, разница в толщине цементной оболочки может привести к увеличению коэффициента цементной оболочки. Учитывая, что толщина штока составляет T s , а площадь развертывания имеет диаметр R a , можно сделать вывод, что если T s остается постоянным во всех случаях, то R a необходимо больше рассверлить для размещения штока.Если отношение T s /R a дает толщину цементной оболочки T m и R a является возрастающей переменной, коэффициент заполнения (F.
R.) будет уменьшаться.
Рисунок 12. Конструкция цементной оболочки вокруг ножки бедренной кости, заключенная в кожух из нержавеющей стали. Мантия толщиной 1 мм показана в крайнем левом углу, 3 мм — в середине, а 7 мм — справа.
Заключение
Толщина цементной мантии напрямую связана с расшатыванием бедренной кости.Коэффициент заполнения цементом рассчитывается с учетом параметров толщины ствола ( T s ) и площади расширения ( R a ). Можно сделать вывод, что существует средняя область идеального соотношения цементного покрова. По результатам нескольких лабораторных исследований было установлено, что оптимальная толщина цементного слоя находится в диапазоне от 3 до 5 мм. Рентгеновские снимки обеспечивают качественную индикацию степени заполнения. Для оптимальной толщины цементной оболочки мы получили идеальное соотношение цементного заполнения бедренного имплантата между 0.56–0,76, и мы наблюдали экспоненциальное уменьшение коэффициента заполнения цементом с увеличением толщины цементного чехла. Модели FEM способны предсказать напряжение и деформацию на границе раздела ножка/цемент и кость/цемент.
Судя по характерным свойствам материала, более толстая мантия обеспечивает низкое напряжение на поверхности контакта с костным цементом, который также может ослабевать. Повышенная потеря костной массы из-за процесса рассверливания может привести к нестабильности и повышенному риску переломов костей.Если мантия слишком толстая, существует повышенный риск появления рентгенопрозрачных линий и непостоянной плотности. Это было дополнительно исследовано и было обнаружено, что в основном это вызвано размещением имплантата дальше к передней стороне бедренной полости и другими факторами, такими как противодавление кровотечения, разная скорость отверждения и т. д. В качестве альтернативы, если мантия слишком тонкая, это может привести к к более высокой вероятности разрушения цемента, что еще больше ослабляет протез. Кроме того, наличие тазобедренного стержня с более овальным поперечным сечением позволяет сделать мантию более тонкой в одном направлении, когда из кости высверливается участок круглого поперечного сечения. Это обеспечит правильную толщину в медиальном и латеральном направлениях и более тонкую в других направлениях. Более высокие напряжения, наблюдаемые в проксимальном конце, позволяют предположить, что разрушение цемента происходит из-за тонкой цементной оболочки, а плохие механические свойства в дистальной области — из-за толстой цементной оболочки, где уровни напряжения низкие. Из этого исследования видно, что для улучшения стабильности протеза тазобедренного сустава, рассматриваемого в этом исследовании, коэффициент заполнения цементом в пределах 0,56–0,76 устраняет риск расшатывания протеза тазобедренного сустава.
Ссылки
1. Jasty M, Maloney WJ, Bragdon CR, O’Connor DO, Haire T, Harris WH. Инициация отказа в цементированных бедренных компонентах эндопротезирования тазобедренного сустава. J Bone Joint Surg Br. 1991; 73: 551–58. [PubMed] [Google Scholar]2. Барак Р.Л., Малрой Р.Д., младший, Харрис У.Х. Усовершенствованные методы цементирования и расшатывания бедренного компонента у молодых пациентов с эндопротезированием тазобедренного сустава.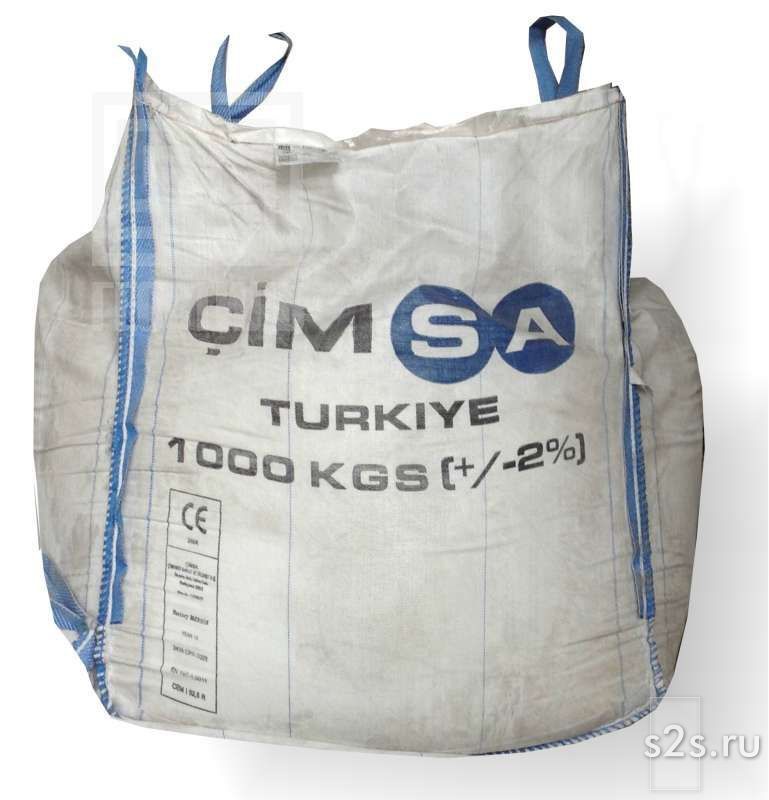


T-Mobile Texas & Cement Hill 2
iPhone 13, iPhone 13 Pro, iPhone 13 Pro Max, iPhone 13 mini, iPhone 12, iPhone 12 Pro, iPhone 12 Pro Max, iPhone 12 mini
Как получить это предложение:
- Приобретите новый iPhone 13, iPhone 13 Pro, iPhone 13 Pro Max, iPhone 13 mini, iPhone 12, iPhone 12 Pro, iPhone 12 Pro Max или iPhone 12 mini с ежемесячной оплатой и уплатите применимый налог с продаж на цена до кредита на момент покупки.
- Создать или активировать новую линию на Magenta® MAX.
- Обмен соответствующим устройством в хорошем состоянии:
- Получите обратно до 800 долл.
США в виде единовременного кредита на счет в зависимости от стоимости вашего предмета обмена и остатка предложения в виде 30 ежемесячных кредитов на счет.
Получите скидку до 800 долларов:
Apple: iPhone X, iPhone XR, iPhone XS, iPhone XS Max, iPhone 11, iPhone 11 Pro, iPhone 11 Pro Max, iPhone 12, iPhone 12 mini, iPhone 12 Pro, iPhone 12 Pro Max, iPhone 13, iPhone 13 мини, iPhone 13 Pro, iPhone 13 Pro Max
Samsung: GS20, GS20+, GS20 Ultra, GS20 FE, GS21, GS21+, GS21 Ultra, Note 10, Note 10+, Note 10 Lite, Note 20, Note 20 Ultra, Z-сгиб, Z-сгиб 2, Z-сгиб 3 , Z-переворот, Z-переворот 3
OnePlus: 9 Pro 5G, 9 5G, 8T, 8T+ 5G, 8 Pro 5G, 8 5G
Google: пиксель 5
LG: Крыло
Motorola: RAZR 4G, RAZR 5G
Получите скидку до 400 долларов:
Apple: iPhone 7, iPhone 7+, iPhone 8, iPhone 8+, iPhone SE 2
Samsung : GS7, GS7 Edge, GS7 Active, GS7 Edge duo, GS8, GS8+, GS8 Active, GS9, GS9+, GS10, GS10 E, GS10+, GS10 5G, Note 8, Note 9, A51, A51 5G, A70 , А71, А71 5G
OnePlus: 7T Pro, 7T Pro McLaren, 7T, 7 Pro 5G, 7 Pro, 7, N10 5G, N100
Google: Pixel 3, Pixel 3 XL, Pixel 3A, Pixel 3A XL, Pixel 4, Pixel 4 XL, Pixel 4A, Pixel 4A 5G
LG: Velvet, V50 ThinQ, V60 ThinQ
Получите скидку до 200 долларов:
iPhone: iPhone 6, iPhone 6 Plus, iPhone 6S, iPhone 6S Plus, iPhone SE (оригинал, iPhone 5, iPhone 5S, iPhone 5c, iPhone 4, iPhone 4S, iPhone 3G, iPhone 3GS, оригинальный iPhone
Если вы отмените до 30 кредитов, кредиты могут быть остановлены и баланс по необходимому финансовому соглашению; связаться с нами. Для квалифицированных клиентов
Свяжитесь с нами, прежде чем отменить услугу, чтобы продолжить оставшиеся кредиты по счетам, или кредиты остановятся и остаток по необходимому финансовому соглашению подлежит оплате (например, 1099,99 долларов США — iPhone 13 Pro Max 128 ГБ / 999,99 долларов США — iPhone 13 Pro 128 ГБ / 699,99 долларов США — iPhone 13 mini 128 ГБ / 799,99 долларов США — iPhone 13 128 ГБ / 999,99 долларов — iPhone 12 Pro Max 128 ГБ / 899 долларов.99 — iPhone 12 Pro 128 ГБ / 629,99 долларов США — iPhone 12 mini 64 ГБ / 729,99 долларов США — iPhone 12 64 ГБ). Налог на цену до кредита, подлежащий уплате при продаже. Ограниченное по времени предложение; подлежит изменению. Соответствующий кредит, обслуживание и сдача устройства (скидка 800 долларов США: Apple: iPhone X, XR, XS, XS Max, 11, 11 Pro, 11 Pro Max, 12, 12 Mini, 12 Pro, 12 Pro Max, 13, 13 mini, 13 Pro, 13 Pro Max; Samsung: Galaxy S20, S20+, S20 Ultra, S20 FE, S21, S21+, S21 Ultra, Note 10, Note 10+, Note 10 Lite, Note 20, Note 20 Ultra, Z Fold , Z Fold 2, Z Fold 3, Z Flip, Z Flip 3; OnePlus: 9 Pro 5G, 9 5G, 8T+ 5G, 8T, 8 Pro 5G, 8 5G; Google: Pixel 5; LG: Wing; Moto: RAZR 5G , RAZR; скидка 400 долларов США: Apple: iPhone 7, 7+, 8, 8+, SE2; Samsung: Galaxy S7, S7 edge, S7 active, S7 edge duo, S8, S8+, S8 active, S9, S9+, S10, S10e , S10+, S10 5G, Note 8, Note 9, A51, A51 5G, A70, A71, A71 5G, OnePlus: 7T Pro, 7T Pro McLaren, 7T, 7 Pro 5G, 7 Pro, 7, N10 5G, N100, Google : Pixel 3, 3 XL, 3A, 3A XL, 4, 4XL, 4A, 4A 5G; LG: Velvet, V50 ThinQ, V60 ThinQ; скидка 200 долларов США: Apple iPhone 6, 6+, 6S, 6S+, SE, 5S, 5c , 4S, 4, 3GS, 3G, оригинальный iPhone).В магазинах и при звонках в службу поддержки может потребоваться помощь в размере 30 долларов США или плата за поддержку обновления.
До 800 долларов США в счет обмена и выставления счетов; должен быть активным и иметь хорошую репутацию, чтобы получать кредиты; разрешить 2 цикла выставления счетов. Максимум 4 устройства со скидкой на аккаунт. Может не сочетаться с некоторыми предложениями или скидками.
Фанера и цементная подложка
Независимо от того, сделана ли она из камня, керамики, фарфора или стеклянной плитки, ее красота и долговечность улучшают множество различных параметров.К сожалению, существует множество причин, по которым укладка плитки может не сработать: от неправильных материалов для укладки до неадекватного смазывания плитки большого формата. Однако одна вещь, которая всегда может помочь установке пройти более гладко, — это использование правильной подложки.
Один из первых вопросов, который возникает у многих перед укладкой – использовать ли фанеру или цементную плиту под плитку. Хотя технически вы можете укладывать большинство плиток на любую гладкую, чистую основу, использование цементной подложки каждый раз будет давать вам превосходные результаты.
Flex and Lippage
В течение многих десятилетий самая большая плитка, которую когда-либо укладывали люди, составляла около 8 дюймов. Это было связано с тем, что все, что больше, могло дать трещины, потому что подложка или подложка под ним часто перемещались. Поскольку плитка не может сгибаться, она в конечном итоге треснула и сломалась.
Решение для фиксации этого движения с помощью фанеры состоит в том, чтобы привинтить его в нескольких местах к основанию пола. Это, однако, создает неровную поверхность, что может привести к выступанию углов плитки над остальной частью пола.
Цементная опорная плита решает обе эти проблемы. При правильной установке с тонким слоем под ним цементная подложка не будет изгибаться, как фанера, и не будет способствовать таким проблемам, как растрескивание. Это делает цементную подложку хорошим выбором для плиточных полов большого формата, а также для старых домов, в которых может быть более неровный пол.
Ровная поверхность
Хотя можно найти очень гладкие, однородные куски фанеры, большинство из них предназначены для использования в мебели и обычно не используются для укладки под плитку, где их не будет видно.Поэтому фанера, обычно продаваемая для этой цели, может быть шероховатой, иметь отверстия от сучков и другие несоответствия, которые могут повлиять на окончательную укладку плитки.
В то время как некоторые плитки могут работать с неровным основанием, другим для достижения наилучших результатов требуется очень гладкая поверхность. Перед укладкой стеклянная плитка, плитка из оникса и другие полупрозрачные материалы должны быть покрыты тонким слоем раствора; Цементная подложка делает это покрытие легким, обеспечивая гладкую, ровную поверхность. Фанера требует более толстой обратной стороны, чтобы сгладить несоответствия, что делает установку более трудоемкой.
Easy Cutting and Fitting
Это редкая установка, позволяющая укладывать целые куски подложки по всему полу; большинство из них необходимо обрезать, прежде чем их можно будет установить. Цементная подложка легко режется; надрежьте его канцелярским ножом и защелкните. Это можно сделать прямо на сайте, на котором он будет установлен, и это займет несколько секунд.
Фанера должна быть измерена на месте, перемещена на стол для резки и распилена, прежде чем она будет доставлена обратно. Пила поднимает опилки и создает беспорядок, который потом нужно убрать, а быстрая резка подложки занимает меньше времени и не производит пыли.
Влажность
Плитку часто укладывают во влажных помещениях или помещениях с высокой влажностью, таких как кухня, прихожая и ванная комната. Когда в качестве подложки используется фанера, она со временем подвергается риску впитывания влаги, что, в свою очередь, заставляет древесину набухать, а затем сжиматься при высыхании. Это, в свою очередь, приводит к таким проблемам, как рассыпание или отсутствие затирки, а также к трещинам на плитке.
Цементная опорная плита более устойчива, чем фанера, в условиях высокой влажности и других влажных средах. Он не набухает и не деформируется, как фанера, поэтому его можно безопасно использовать в прихожих и ванных комнатах, где такие вещи, как разливы и лужи, являются нормальными, а также в местах с высоким уровнем влажности воздуха.
Грузоподъемность
Пол — не единственное место, где укладывается плитка. Окружение камина, стены и столешницы — все это общие области для плитки. Когда вы добираетесь до вертикальных приложений, тяжелые плитки, такие как сланец или крупноформатный фарфор, становятся слишком тяжелыми, чтобы хорошо прилипать к фанере.
Цементная подложка имеет большую грузоподъемность, поэтому можно укладывать любую плитку в любом месте и получать такие же отличные результаты.
Улучшенная адгезия
Лучший аргумент в пользу использования фанеры или цементной плиты под плитку – процесс склеивания.Фанера пористая и не предназначена для использования с большинством современных растворов на латексной основе.