Вакуумирование холодильных машин: Средства вакуумирования и зарядки холодильной машины хладагентом
Практические советы по монтажу и обслуживанию современной холодильной техники
Практические советы по монтажу и обслуживанию современной холодильной техники
Статья из журнала «Холодильная техника»
Монтаж любого холодильного контура и послемонтажные операции осуществляются в такой последовательности:
- разработка монтажной схемы;
- собственно монтаж;
- вакуумирование холодильного контура;
- промывка;
- опрессовка и проверка герметичности;
- заправка хладагентом и маслом;
- настройка приборов защитной автоматики.
Это, прежде всего определение мест размещения компонентов холодильной установки и схемы обвязки трубопроводов. При этом следует исходить из того, чтобы:
- количество сквозных отверстий в стенах было минимальным;
- к компонентам холодильной установки был обеспечен удобный доступ для технического обслуживания при эксплуатации;
- к компрессору, конденсатору и воздухоохладителю свободно поступал воздух;
- длина трубопроводов была минимально возможной;
- компрессор располагался на горизонтальном основании с использованием антивибрационных амортизаторов (если они имеются).
Рис.1. Маслоподъемные петли
Монтаж холодильной системы
Сборку контура необходимо осуществить как можно быстрее, чтобы избежать попадания в него влаги, воздуха, загряз нений. Если возник перерыв в работе, все отверстия в контуре следует заглушить. Компрессор и фильтр-осушитель подключаются к контуру в последнюю очередь, т.е. непосредственно перед вакуумированием и заправкой системы.
Трубы должны быть расположены горизонтально или вертикально, за исключением всасывающих и нагнетательных патрубков. Их устанавливают с небольшим уклоном: всасывающие — в сторону компрессора, нагнетательные — в сторону маслоотделителя.
Крепления труб располагаются на одинаковом расстоянии. Это зависит от диаметра труб и массы деталей, которые на них монтируются.
На магистралях всасывания перед вертикальным участком и после него необходимо делать масло подъемные петли (рис. 1). В случае особенно значительного изменения скорости хладагента при различных режимах работы вертикальные участки выполняются в виде сдвоенной магистрали. Для обеспечения гарантированного возврата масла в компрессор скорость хладагента во всасывающих трубопроводах должна быть не менее 3,5 м/с (на горизонтальных участках) и не более 15 м/с (во избежание производственного шума).Второстепенные элементы надо располагать так, чтобы к ним был доступ для проведения ремонтных операций. Расположение системы автоматического управления и приборов защитной автоматики должно обеспечивать проведение проверок и регулировок с применением обычного инструмента.
Компрессор должен быть закреплен анкерными болтами. Конденсатор и воздухоохладитель монтируются с использованием соответствующего крепежа согласно инструкции изготовителя.
Компрессоры, работающие параллельно, устанавливают на одном уровне в горизонтальной плоскости, и их масляные картеры соединяют уравнительной линией для выравнивания в них уровня масла. Если уравнительная линия состоит из одного трубопровода, то его диаметр должен быть достаточным для прохождения суммарного количества масла и паров хладагента. Если уравнительная линия состоит из двух трубопроводов (рис. 2,а), то их диаметры рассчитываются исходя из того, что один служит для выравнивания уровня масла, а другой — для выравнивания давления в картерах.
Для выравнивания уровня масла можно установить регуляторы уровня (рис. 2,6). В этом случае появляется возможность монтировать компрессоры на разных уровнях. Применение регуляторов уровня по сравнению с уравнительными трубопроводами более дорогостоящий способ, так как требуются еще сепаратор масла, клапан выравнивания давления, масляный резервуар, фильтр. При этом следует помнить, что каждый компрессор должен быть защищен прессостатом высокого давления, например КР5.
Послемонтажные операции
По окончании монтажных работ выполняются следующие операции:
- вакуумирование холодильного контура;
- проверка герметичности;
- заправка хладагентом и маслом;
- пуск и наладка.
Для проведения указанных работ необхо-димы: вакуумный насос, мановакуумметр, заправочная емкость или баллон с хлад-агентом, шланги, течеискатель.
Вакуумный насос и заправочная емкость могут поставляться объединенными в один агрегат, именуемый заправочной станцией (рис. 3).
Вакуумный насос удаляет из холодильно-го контура атмосферный воздух, влагу, инер-тный газ.
Вакуумный насос должен обеспечивать быстрое снижение давления в холодильном контуре до 0,05 миллибар. Поэтому производительность насоса должна быть не менее 20 л/мин, шланги должны иметь большой диаметр и малую длину. Рекомендуются шланги диаметром не менее 1/4″ и максимальной длиной не более 1 м. Использование ниппельных клапанов Шредера при вакуумировании нежелательно. Для компрессоров с заправочным штуцером следует применять быстроразъемное соединение, а для остальных компрессоров — запорные вентили на магистралях всасывания и нагнетания компрессоров. Шток вентиля при этом должен быть в среднем положении.
Вакуумирование системы проводится дважды:
- сначала для проверки герметичности подсоединения вакуумного насоса,
- а затем уже для подготовки системы к заполнению хладагентом.
Для проверки герметичности подсоединения вакуумного насоса необходимо:
- после соединения заправочной станции с компрессором перекрыть входные вентили компрессора;
- включить вакуумный насос и снизить давление в шлангах до минимально возможного, после чего перекрыть входной вентиль насоса;
- выключить насос и зафиксировать показания мановакуумметра: давление должно быть не выше 0,05 миллибар;
- если давление до указанного значения не снижается, заменить негерметичные шланги или вентили или поменять масло в насосе.
Вакуумирование системы выполняется либо со стороны всасывания, либо со стороны нагнетания, а для больших систем — с двух сторон одновременно. Последовательность вакуумирования:
- соединяют шлангами заправочную станцию с компрессором;
- открывают все вентили и клапаны, в том числе электроклапаны, автоматические клапаны устанавливаются в положение максимального открытия;
- холодильный контур вакуумируют по возможности до давления, отмеченного на мановакуумметре при предварительном вакуумировании.
В случае пропуска воздуха надо действовать следующим образом:
- приблизительно локализовать это место, изолировав его от соседних участков;
- подтянуть резьбовые и/или фланцевые соединения;
- повторить Вакуумирование;
- контролировать герметичность до тех пор, пока не будет сохраняться вакуум в холодильном контуре.
Заполнение контура системы хладагентом осуществляется под давлением около 2 бар. После заполнения надо проверить все соединения с помощью течеискателя (рис. 4). В случае обнаружения утечек хладагента следует опорожнить контур с помощью сливного устройства и вакуумного насоса, устранить утечки и повторить данную операцию, добиваясь полной герметичности системы.

Для слива хладагента всегда следует использовать сливное устройство (рекуператор).
Слишком малый перегрев на выходе испарителя во время операции заправки может вызвать в компрессоре гидроудар.
Необходимо проверить кабельные и проводные электрические трассы, пусковые приборы при отключенном компрессоре, а также направление вращения электродвигателей, при необходимости поменяв две фазы.
Настройка приборов защитной автоматики (прессостат высокого давления, автомат защиты по току и др. ) осуществляется на работающей установке.
Для настройки реле высокого давления повышают давление конденсации до максимального значения, после чего настраивают реле с помощью манометра. Для настройки реле низкого давления уменьшают давление всасывания до минимального значения и настраивают реле с помощью манометра. Аналогично настраивают все остальные приборы защиты.
Во время настройки необходимо постоянно контролировать работу установки.
Особенности монтажа и заправки оборудования, работающего на хладагенте R134a
Использование хладагента R134a в холодильных установках выдвигает множество различных требований к их монтажу и дальнейшей эксплуатации. Ниже приводится несколько общих рекомендаций, позволяющих решить возможные проблемы.
При монтаже и техническом обслуживании оборудования, предназначенного для работы на новом хладагенте, необходимо соблюдать особую чистоту.
В компрессоре, работающем на R134a, должно быть использовано смазочное масло на основе эфира. Эфирные масла легко смешиваются с R134a, обеспечивая хорошую смазку компрессора, что значительно продлевает срок его службы. Смесь R134a и эфирного масла поглощает влагу гораздо интенсивнее, чем смесь R12 и минерального масла. Поэтому в установке должен быть смонтирован специальный влагоотделитель с молекулярном ситом, рассчитанным на структуру молекул R134a. Маркировка терморегулирующего вентиля должна однозначно указывать на то, что он предназначен для R134a (рис. 6).
Подавляющее большинство применяемых регулирующих приборов, например прессостаты, термостаты, а также смотровые стекла, можно использовать и в установках на хладагенте R134a. Учитывая, что R134a более текуч, чем R12, регулирующие приборы должны быть преимущественно с паяными соединениями.
Перед заправкой хладагентом R134a систему нужно полностью отвакуумировать до абсолютного давления 0,03…0,04 миллибар. Наилучшего результата можно добиться с помощью двухступенчатого вакуумного насоса.
Внимание!
Вакуумный насос должен подходить для хладагента R134a. Запрещается использовать насосы, служившие ранее для вакуумирования контуров с другими хладагентами. Заправочные емкости и принадлежности для слива должны быть новыми и чистыми. Нельзя пользоваться инструментом, имевшим хоть малейший контакт с R 12 и минеральным маслом.
Рис. 6. Маркировка терморегулирующего вентиля для R134a фирмы Danfoss
Рис. 7. Возможные способы маркировки шлангов, приборов и инструментов, применяемых для технического обслуживания холодильного оборудования на R134a
Гибкие шланги для R134a должны иметь повышенную герметичность. При монтаже и демонтаже специальные быстроразъемные соединения обеспечивают сохранение в шлангах хладагента. Шланги, все приборы и инструменты, используемые при техническом обслуживании установок на R134a и эфирных маслах, должны иметь соответствующую маркировку (рис. 7), и их не рекомендуется применять для работы с другими хладагентами.
Для поиска утечек в контурах с R134a существует несколько способов. Многие разработчики поставляют электронные течеискатели, которые при выявлении утечки подают звуковой сигнал. В других течеискателях используются ультрафиолетовые лампы. В хладагент добавляют присадку, которая смешивается с эфирным маслом. В случае утечки вытекающее из контура масло с присадкой в ультрафиолетовых лучах становится видимым. Ультрафиолетовые лампы течеискателей старого образца для R134а не годятся.
Хотя R134a нетоксичен и безвреден для озонового слоя, целесообразны, по экологическим и экономическим соображениям, его рекуперация и повторное использование. В настоящее время изготовляются передвижные агрегаты для извлечения R134a из контуров при их вакуумировании и восстановления хладагента с целью повторного использования. Агрегат содержит встроенный мощный вакуумный насос, обеспечивающий глубокий вакуум.
Вакуумирование малой холодильной машины — Справочник химика 21
Химия и химическая технология
Статьи Рисунки Таблицы О сайте English Для совершенствования технологии и режимов вакуумирования при изготовлении, ремонте и монтаже малых холодильных машин, определения допустимых концентраций, оценки влияния на химическую стабильность системы необходимо знать растворимость и основные закономерности образования неконденсируемых примесей в рабочей среде.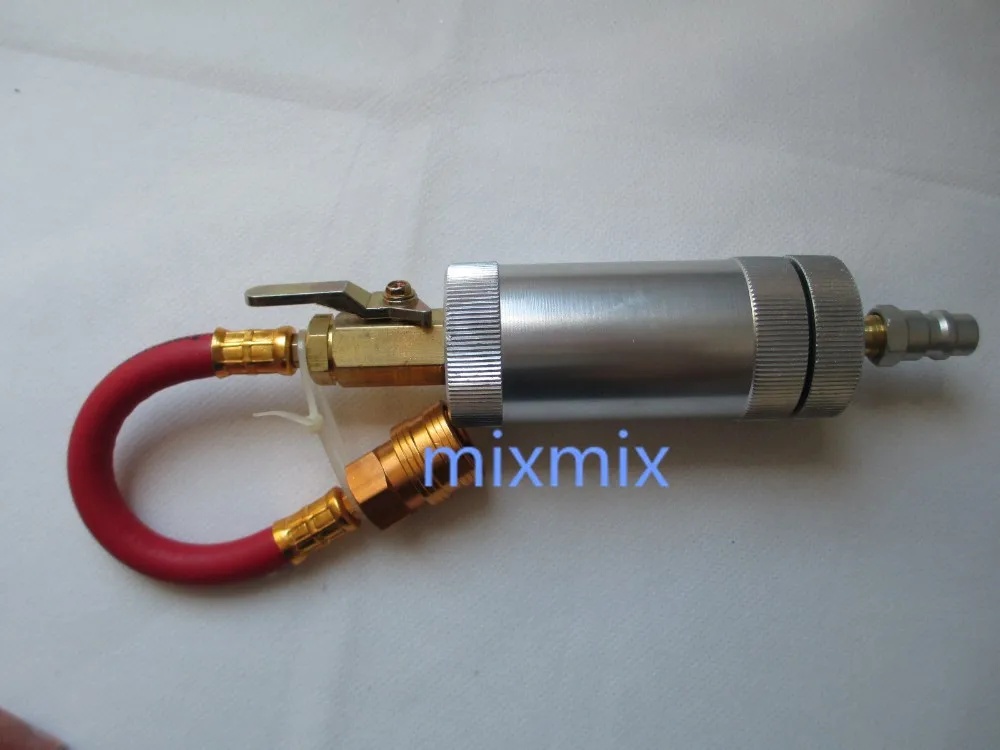
Ремонт герметичных малых холодильных агрегатов, в свою очередь, в значительной степени отличается от ремонта малых открытых холодильных агрегатов. При ремонте герметичных машин наибольшие трудности связаны с процессами очистки, ибо. технологический процесс ремонта этих машин требует повышенной чистоты и тщательности сборки. В герметичных агрегатах механический износ машин мал вследствие того, что пары трения сделаны с большой степенью точности. Обычно на комбинатах не осуществляется ремонт, связанный с механическим износом деталей,, а проводятся лишь технологические операции, гарантирующие качество очистки, осушки и вакуумирование системы. Вообще ремонт герметичных холодильных машин значительно более трудоемок, чем изготовление новой холодильной машины на заводе-изготовителе, ибо загрязнение внутренней системы агрегата, связанное со сгоранием электродвигателя, требует очень тщательной и пока еще полностью не разработанной технологии очистки.
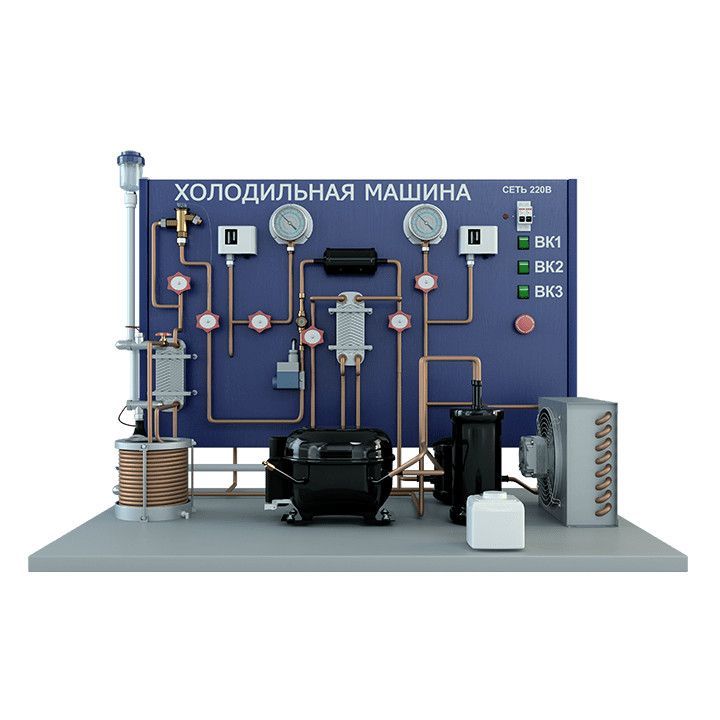
Холодильная техника Кн. 3 (1962) — [ c.386 ]
Смотрите так же термины и статьи:
Холодильная машина
© 2022 chem21.info Реклама на сайте
Заправка холодильной установки хладагентом | Холод
17.05.2016
Хладагент – это рабочее вещество холодильной машины, которое отнимает тепло у охлаждаемого объекта при кипении в процессе испарения и отдает его окружающей среде после конденсации. На данный момент основными хладагентами систем промышленного холода являются аммиак и фреон – вещества, при прямом контакте могущие нанести вред здоровью человека. Именно поэтому при заправке холодильных установок хладагентом необходимо соблюдать обязательные правила безопасности и придерживаться определенного порядка действий.
Заполнение системы хладоносителем в холодильных системах с промежуточным охлаждением
В холодильных системах с промежуточным хладоносителем заполнение системы рассолом осуществляется перед заполнением ее хладагентом (аммиаком). Рассол изготавливается на месте в баках-концентраторах холодильных станций из раздробленного твердого хлористого кальция (или твердого хлористого натрия), разведенного водой с добавлением веществ, уменьшающих коррозию металла трубопроводов. Перемешивание рассола осуществляется приводными мешалками циркуляционных насосов или барботажем воздуха, а концентрация контролируется ареометром с таким расчетом, чтобы температура замерзания хладоносителя была на 8-10°С ниже температуры кипения хладагента в испарителе. Заполнение холодильной системы хладоносителем нужной концентрации происходит с помощью рассольного насоса путем вытеснения воздуха через открытые воздухоспускные краны.
Заполнение хладагентом аммиачных холодильных установок
Заполнение холодильной системы аммиаком – ответственная и опасная операция, поэтому к ней допускается только специально обученный персонал, прошедший дополнительный инструктаж по технике безопасности и снабженный индивидуальными средствами защиты. Не участвующий в работах персонал удаляется из помещения.
Заправка холодильного оборудования аммиаком осуществляется в соответствии с нормами заполнения в процентном соотношении от внутреннего объема холодильных аппаратов согласно техническим паспортам, в которых содержатся сведения по монтажу и обслуживанию холодильного оборудования. Так, аммиаком заправляется 80% объема кожухотрубных испарителей или 50% панельных, 20% отделителей жидкости, 30% промежуточных сосудов, 50% линейных ресиверов, 100% жидкостных трубопроводов и т.д.
Перед заправкой аммиаком вновь смонтированные или отремонтированные холодильные системы тщательно продуваются сухим воздухом для удаления следов влаги, оставшихся после гидравлических испытаний. Затем система проверяется на герметичность для исключения подсоса воздуха во время дальнейшей эксплуатации, неплотности устраняются и лишний воздух удаляется с помощью специальных насосов или работающих на том же хладагенте компрессоров. После вакуумирования холодильной системы до остаточного давления 13,3 кПа в нее подается хладагент.
Запас аммиака целесообразно хранить в резервных ресиверах (на холодильных станциях). Туда он поступает из автомобильных или железнодорожных цистерн по жидкостному трубопроводу благодаря разнице давлений, создаваемой путем отсасывания из ресивера пара хладагента через отделитель жидкости. Наполнение емкости для аммиака не должно превышать 80% его объема (степень заполнения контролируется визуально по стеклу Клингера).
Порядок заправки больших аммиачных холодильных систем
Большие холодильные системы могут заправляться напрямую из железнодорожных или автомобильных цистерн по жидкостным трубопроводам. Слив аммиака в холодильную систему происходит поочередно в приборы охлаждения и осуществляется через испарительную систему. С помощью компрессора обеспечивается разница давлений в испарителе и цистерне: когда давление на одном участке выравнивается и слив прекращается, с помощью запорного вентиля вакуумируется следующий участок. Такой порядок заправки системы хладагентом производится с целью исключить возможность «влажного хода» компрессора, при котором очень быстро выходит из строя компрессорное оборудование. Норма заполнения системы аммиаком контролируется приборами (падение давления в цистерне) и визуально (оттаивание жидкостного трубопровода).
Порядок заправки небольших АХУ
Небольшие аммиачные системы заправляются с помощью баллонов, которые устанавливаются в наклонном положении на специальной подставке вентилями вниз. Количество баллонов зависит от количества вентилей на заправочном коллекторе, причем слив аммиака производится одновременно из всех баллонов, находящихся на подставке. Об окончании слива сигнализирует падение давления в баллонах, оттаивание их горловин и присоединительных трубок. Общее количество слитого в систему аммиака определяется исходя из разности массы баллонов до и после их опустошения, визуально по смотровым стеклам Клингера и обмерзающим трубкам, а также по режиму работы холодильной установки.
По мере заполнения холодильной системы аммиаком на конденсаторы подается вода, налаживается циркуляция рассола (в системах с промежуточным охлаждением хладоносителем).
Заправка холодильных установок фреоном
Перед заполнением холодильной системы фреоном ее вакуумируют, выдерживают сутки и заправляют маслом. Фреоновые установки большой производительности заправляются по принципу крупных аммиачных систем, малые вначале проверяются галоидной лампой на герметичность. Также во время заправки периодически проверяется герметичность холодильной системы вне зависимости от ее величины.
Заполнение фреоновых установок происходит из контейнеров или баллонов через коллектор и фильтр-осушитель. Сами принципы заправки системы хладагентом (фреоном и аммиаком) схожи: заполнение паром фреона также происходит через испарительную систему благодаря разнице давлений, обеспечиваемой компрессорным оборудованием. При присоединении баллона к холодильной системе обязательно используют индикатор влажности, который изменяет цвет в случае наличии влаги во фреоне.
Об окончании заправки судят по массе слитого в систему фреона, которая высчитывается исходя из разницы веса баллонов до начала и после окончания заправки системы.
3.4.2. Трудовая функция / КонсультантПлюс
Трудовые действия | Проверка рабочего места на соответствие требованиям безопасности, подготовка инструмента, приспособлений, КИП и СИЗ к выполнению предпусковых испытаний и заправке холодильных систем |
Изучение технической документации и проверка документации, подтверждающей готовность холодильных систем и КИП к испытаниям | |
Проверка соответствия монтажа оборудования техническим требованиям и правильности подключения электрооборудования | |
Проверка герметичности сальников, сварных швов, соединений на герметичность химическим индикатором | |
Подготовка оборудования холодильной установки к испытаниям с частичной разборкой и сборкой узлов | |
Продувка всей холодильной системы и очистка охлаждающих устройств и трубопроводов от грязи и ржавчины, освобождение их от воздуха (вакуумирование) | |
Испытание на прочность и герметичность всех аппаратов, охлаждающих устройств и трубопроводов, а также сварных и разъемных соединений (раздельно по сторонам высокого и низкого давления), устранение выявленных неплотностей | |
Проверка работы системы охлаждения конденсаторов с заполнением их водой и спуском воздуха, проверка работы системы смазки | |
Испытание компрессора без заполнения хладагентом, наблюдение за нагревом трущихся частей оборудования и уровнем вибрации | |
Проведение теплотехнических испытаний и фиксация в журнале: температуры, давления; параметров, определяющих расход хладагента, масла, воды, рассола и воздуха; мощности, потребляемой из сети электродвигателями; параметров, характеризующих состояние воздуха в охлаждаемых помещениях холодильных установок | |
Заправка маслосистем маслом (замена масла) после их промывки, продувки | |
Наполнение систем хладагентом и хладоносителем (первоначальное и полное заполнение системы хладагентом) и приготовление хладоносителя | |
Испытание компрессоров, насосов, вентиляторов на холостом ходу и под нагрузкой; испытание холодильных машин на холодопроводимость | |
Проверка работоспособности предохранительных устройств, замеры пусковых и номинальных токов | |
Регулировка и настройка реле давлений | |
Наладка работы всех элементов холодильной установки на холодопроизводительность | |
Составление актов об испытании оборудования, о заполнении и опробовании холодильной системы и актов приемки оборудования | |
Необходимые умения | Читать чертежи, проектную и рабочую документацию |
Пользоваться сопроводительной и технической документацией на монтируемое оборудование | |
Использовать слесарный и механизированный инструмент, оборудование, КИП, средства гигиены и пожаротушения при выполнении испытательных работ | |
Применять СИЗ при выполнении испытательных работ | |
Осуществлять испытания оборудования холодильных установок на холостом ходу и под нагрузкой, испытания холодильной системы на чистоту, герметичность, прочность и плотность | |
Оценивать качество выполненных испытательных работ | |
Выполнять испытания и заправку холодильных систем хладагентом и теплоносителем с соблюдением требований охраны труда и экологической безопасности | |
Оказывать первую помощь пострадавшим при аварийных ситуациях, пожаре, отравлении или поражении частей тела и глаз хладагентом | |
Оформлять акты на выполненные испытательные работы в бумажном и электронном виде | |
Необходимые знания | Нормативные правовые акты, технические регламенты и профессиональные термины по испытаниям и заправке холодильных систем хладагентом и теплоносителем |
Перечень и правила пользования сопроводительной и технической документацией | |
Назначение, устройство слесарного и механизированного инструмента, КИП, правила пользования ими | |
Условные обозначения, используемые в монтажных проектах | |
Устройство холодильной техники, основы термодинамики, теории теплообмена, электротехники и автоматизации | |
Требования, предъявляемые к качеству испытательных работ и заправки холодильных систем хладагентом и теплоносителем | |
Порядок продувки и подготовки холодильной системы к испытаниям, порядок ее испытания на герметичность, прочность, плотность и вакуумную плотность | |
Требования охраны труда, пожарной, промышленной и экологической безопасности при выполнении испытательных работ и заправке холодильной системы | |
Меры безопасности при работе с хладагентами | |
Правила применения СИЗ, средств пожаротушения, гигиены и оказания первой помощи при аварийных ситуациях, пожаре, отравлении или поражении частей тела и глаз хладагентом | |
Стандартные компьютерные офисные приложения, браузеры, профессиональные ресурсы информационно-телекоммуникационной сети «Интернет» по холодильной технике | |
Правила составления актов на выполненные испытательные работы в бумажном и электронном виде | |
Другие характеристики | — |
Принцип работы компрессора, как проверить компрессор
Подключение холодильного компрессора в холодильный контур имеет определенные «технологические хитрости»:
Подключение компрессора к трубопроводам холодильного контура имеет однозначную «направленность» — всасывающий терминал, когда происходит работа компрессора, служит для поступления в компрессор хладагента из испарительной части холодильной установки в газообразном состоянии (сторона низкого давления), а нагнетающий терминал компрессора служит для подачи скомпрессированного (сжатого) хладагента в конденсирующие (сжижающие) устройства (сторона высокого давления).
Чтобы происходила нормальная работа холодильной машины — в холодильном контуре должен перемещаться только «химически чистый» холодильный агент с сопутствующим этому перемещению хладоновым маслом. В связи с этим при механическом подключении холодильного компрессора в холодильный контур необходимо быть уверенным во внутренней чистоте самого холодильного контура.
Недостаточная очистка холодильного контура (или её отсутствие), когда подключается новый компрессор, приводит к печальным последствиям: наличие «несанкционированных» компонентов в холодильном контуре (сказывается предыдущая работа холодильной установки или замена компрессора в результате аварии) приводят к изменению термодинамических свойств хладагента, а значит, и к повышению нагрузок на механизмы компрессора. Превышение нагрузок на механизмы компрессора выше допустимых заводом изготовителем, как минимум, ведёт к резкому снижению ресурса нового компрессора, если не к полной поломке.
Специально следует отметить необходимость соблюдения «полной совместимости» компонентов:
- масло для компрессора
- используемый хладагент (ремонт холодильной установки)
- соответствие вязкости масла необходимым температурам кипения и конденсации хладагента
Новый фильтр для компрессора при его замене — обязательная процедура. Только следует помнить, что новый фильтр нельзя расценивать как «панацею» для очистки холодильного контура, потому что любой фильтр имеет вполне ограниченные его объёмом фильтрующие способности. Накопление загрязнений в фильтре снижает его «пропускную способность» — нарушение условий циркуляции хладагента в холодильном контуре со всеми вытекающими негативными последствиями.
Когда происходит установка компрессора и подготовка компрессора к пуску, то одним из важнейших условий является соблюдение герметичности холодильного контура. Проверку на герметичность вновь выполненных соединений терминалов компрессора с трубопроводами холодильного контура необходимо производить испытанием (опрессовкой) высоким давлением. Уровень испытательного давления должен в 2…3 раза превышать максимальное рабочее давление хладагента, которое возможно при номинальном режиме работы холодильной машины. Как правило, опрессовку производят используя азот, который благодаря своим физическим свойствам попутно ещё и высушивает холодильный контур. Длительность процесса опрессовки зависит от объема и разветвлённости холодильного контура, так как необходимо убедиться не только в герметичности соединений холодильного контура с компрессором, но и в герметичности всего холодильного контура.
Следующим этапом работ с холодильной установкой при подключении компрессора будет процесс вакуумирования. Так как для нормальной работы хладагента недопустимо наличие каких-либо добавок и примесей в холодильном контуре процесс вакуумирования призван максимально удалить из «внутренностей» холодильной машины все присутствующие там газы, включая воздух, который однозначно заполняет все трубопроводы при разгерметизации трубопроводов.
Вакуумирование осуществляется до «точки росы», определяемой тем, какой хладагент используется, его тип. Это вызвано тем, что синтетическое масло, заливаемое в компрессор, является очень гигроскопичной субстанцией и успевает «накопить» в себя достаточное количество влаги за время «контакта с окружающей средой», способное в последствии нарушить условия работы холодильной системы.
Процесс вакуумирования не может быть «одномоментным» и требует существенных временных затрат, которыми нельзя пренебрегать: молекулам воды необходимо время для того, чтобы покинуть «вязкие объятия» хладонового масла, и вакуумный насос способен удалить из системы.
Кроме того вакуумирование холодильного контура является второй проверкой холодильного контура на герметичность в целом.
Только при получении положительных результатов по испытаниям холодильного контура опрессовкой и вакуумированием появляется возможность приступить к заправке холодильного контура хладагентом.
В большинстве холодильных компрессоров «движущей силой», приводящей их в работоспособность, является электродвигатель. Поэтому при подключении компрессора очень важное внимание уделяется выполнению электротехнических мероприятий.
Во-первых, это тщательное соблюдение норм и правил электробезопасности: все отсоединения и присоединения электропроводов производятся на заведомо отключенном от питающей электросети холодильном оборудовании.
При выполнении электрических соединений крайне необходимо следить за качеством и надежностью создаваемых или восстанавливаемых контактов. Диаметры используемых проводов должны соответствовать потребляемым токам электродвигателей компрессоров, толщина и надёжность (целостность) изоляции проводов должна быть достаточной для уровней используемых напряжений электросети.
Во-вторых, однофазные электродвигатели компрессоров обычно оборудуются внешними пуско-защитными устройствами, включающими в себя пусковые и токовые реле, пусковой конденсатор для компрессора и фазосдвигающий. Когда нужно установить компрессор и подключить его, то не следует пренебрегать заменой соответствующей пуско-защитной арматуры на новую, так как все электротехнические изделия имеют свой ресурс наработки и их надежность со временем падает. Предустановочная проверка всех элементов на их работоспособность и целостность, даже новой пуско-защитной арматуры, является обязательной процедурой при подключении компрессора.
Включение трехфазных электродвигателей компрессоров обычно происходит через управляемые регулирующими и защитными устройствами контакторы (пускатели). Состояние контактных площадок контакторов требует постоянной проверки и при малейших подозрениях (например: нагар на контактных группах) контакторы подлежат замене на новые.
В-третьих, некоторые виды компрессоров, спиральный компрессор, винтовой и иногда роторный, очень критичны к направлению вращения вала электродвигателя. Если у однофазных электродвигателей «однонаправленность» вращения вала может быть «запрограммирована» на стадии изготовления электродвигателя, то при подключении трехфазных электромоторов следует строго следить за чередованием фаз питающих напряжений, чтобы получить необходимое направление вращения. «Противовращение» валов электродвигателей спиральных и винтовых компрессоров однозначно приводит к механическому разрушению нагнетающих механизмов (спиралей и винтов) таких компрессоров.
В-четвертых, при подключении компрессоров с изменяемой скоростью вращения (переменной производительности) необходимо предварительно убедиться в исправности и работоспособности инверторных устройств, управляющих и регулирующих производительность компрессора по текущим параметрам холодильного контура во время его работы.
Перед пуском и моментом, когда начинается работа холодильного компрессора, обязательно следует убедиться, что все защитные и управляющие приборы и устройства холодильной установки, такие как реле давления, контроллеры, термо-регулирующие вентили, соленоидные клапаны и т.п., исправны, отрегулированы, запрограммированы соответствующим образом, правильно подсоединены и готовы к тому, чтобы работа холодильных компрессоров происходила в штатном режиме.
Все технологические операции, проводимые ремонтным персоналом во время подключения компрессора в холодильную установку должны быть заактированы. Демонтированные и вновь установленные запасные части зарегистрированы и учтены, с указанием причин, по которым необходимо провести ремонт холодильных установок. Полученные параметры (электрические и холодильные) внесены в журнал учета профилактик (техническое обслуживание оборудования) и ремонтов каждой конкретной холодильной машины или установки.
Только тщательное и качественное соблюдение всех необходимых действий и процедур может обеспечить достижение заданных холодильных параметров после проведения ремонтных работ и чтобы холодильное оборудование долго и бесперебойно работало.
Заправка холодильной установки фреоном | АквилонСтройМонтаж
Заправка холодильной установки фреоном производится перед ее первым перезапуском для обеспечения всех необходимых процессов. Ее выполняют в соответствии с рядом требований и правил, обеспечивая полную герметичность системы во избежание утечек.
Порядок выполнения заправки
Заправка холодильной установки фреоном производится через специальные заправочные вентили. Вливают жидкий холодильный агент по жидкостному трубопроводу. Но в зависимости от типа и модели агрегата, заправка может происходить по-разному:
- Маленькие модели могут заправляться через всасывающую магистраль в газовой фазе.
- На агрегатах, работающих с перегревом, вентиль устанавливается перед осушителем на жидкостной магистрали, чтобы задержать влагу, присутствующую в хладагенте.
- В моделях с затопленными испарителями он может располагаться там же или между отделителем жидкости и ТРВ. Во втором случае дополнительно устанавливается осушитель.
Заполнение производится двумя способами – напрямую из баллона или заправочного цилиндра, предварительно заполненного точно рассчитанной дозой фреона. Его объем указывается на маркировочной табличке.
5 причин приобрести холодильные установки от АквилонСтройМонтаж
- Использование только проверенных комплектующих Европейских И Российских производителей
- Реально Внедрение импортозамещения в производстве
- Сборка холодильных агрегатов без использования сварки, болтовое соединение
- Порошковая покраска каркаса и антикоррозийная обработка
- Изготовление установок по индивидуальным заказам и размерам
ОСТАВИТЬ ЗАЯВКУ
Вакуумирование системы
Перед началом заправки гибкий шланг от цилиндра соединяют с машиной и удаляют из него остатки воздуха, чтобы он не проник в контур. Для этого на мгновенье открывают вентиль и сразу же до отказа закручивают гайку.
При заполнении в газовой среде, баллон переворачивают вверх днищем, так как он имеет один простой вентиль с проходом для паров. При заправке крупных машин используются баллоны с двухходовыми вентилями – для пара и жидкости, поэтому его оставляют на днище.
Количество хладагента необходимо постоянно контролировать. Чтобы обеспечить нужную степень заполнения используются специальные весы, играющие роль электронных дозаторов. При использовании цилиндра используется то количество хладагента, которое предстоит залить в агрегат.
Подготовка к заправке
Во время заправки часто происходит такая ситуация, что давление в контуре и баллоне уравнивается. Для продолжения перелива необходимо повысить давление в баллоне. Это достигается путем его помещения в теплую воду около 40С или опоясыванием электронагревательным шнуром.
С заправочными цилиндрами дело обстоит проще – они комплектуются небольшими электронагревателями, которые позволяют повысить давление на точно требуемую величину.
Контроль качества заправки
На стадии заполнения установок с одним или несколькими конденсаторами можно не останавливать циркуляцию воды в них. Она позволяет снизить температуру и тем самым обеспечивает запас холодильного агента внутри ресивера или конденсатора.
После выполнения этих работ производят включение компрессора и ждут, пока не установится запланированный режим работы. После этого нужно следить за показаниями уровня масла, давления нагнетания и всасывания, смотровым стеклом.
Если все сделано правильно, то в смотровом стекле виден сплошной поток жидкого хладагента. Пузырьки могут появляться только при открытии ТРВ. Если заправка холодильной установки фреоном была проведена не в полном объеме, то пузырьки будут идти постоянно. В этом случае необходима дозаправка.
РКЦ WSR
РЕГИОНАЛЬНЫЙ КООРДИНАЦИОННЫЙ ЦЕНТР WORLDSKILLS RUSSIA СВЕРДЛОВСКОЙ ОБЛАСТИ
VI Финал Национального чемпионата «Молодые профессионалы (ВОРЛДСКИЛЛС РОССИЯ)»

Результаты распределения квот в рамках Отборочных Соревнований на право участия в VI Финале Национального чемпионата «Молодые профессионалы (ВОРЛДСКИЛЛС РОССИЯ)»
Программы повышения квалификации Академии Ворлдскиллс
Инфраструктурные листы по компетенциям Финала WSR 2018
Отборочные соревнования на право участия в Финале Национального чемпионата «Молодые профессионалы» (WorldSkills Russia) — 2018
Конкурсная документация по отборочным соревнованиям в рамках Финала Национального чемпионата WorldSkills Russia в 2018 году
Демонстрационный экзамен 2018
Результаты проведения Регионального чемпионата по стандартам WorldSkills в Свердловской области в 2018 году

Итоги VI открытого Регионального чемпионата «Молодые профессионалы» (WorldSkills Russia) Свердловской области
СМИ о региональном чемпионате WorldSkills 2018
Требования к практике обслуживания стационарного холодильного оборудования
Правила EPA (40 CFR, часть 82, подраздел F) в соответствии с разделом 608 Закона о чистом воздухе требуют от техников, которые обслуживают стационарное холодильное оборудование и оборудование для кондиционирования воздуха, соблюдения определенных правил. Эти методы предназначены для максимального извлечения и рециркуляции хладагентов, которые могут быть озоноразрушающими веществами (ОРВ ОРВ Соединение, способствующее разрушению стратосферного озона. ОРВ включают хлорфторуглероды (ХФУ), гидрохлорфторуглероды (ГХФУ), галоны, бромистый метил, четыреххлористый углерод, гидробромфторуглероды, хлорбромметан и метилхлороформ.ОРВ, как правило, очень стабильны в тропосфере и разлагаются только под воздействием интенсивного ультрафиолетового света в стратосфере. Когда они распадаются, они выделяют атомы хлора или брома, которые затем разрушают озон. Доступен подробный список (http://www.epa.gov/ozone/science/ods/index.html) веществ класса I и класса II с их ODP, GWP и номерами CAS.) или сильнодействующих парниковых газов. Различные методы применяются к различному оборудованию, в зависимости от его размера и производителя.
Требования к эвакуации
Приборы с более чем пятью фунтами хладагента
Технические специалисты должны вакуумировать оборудование для кондиционирования воздуха и охлаждения до установленного уровня вакуума при открытии оборудования для технического обслуживания, обслуживания, ремонта или утилизации. Требуемый уровень эвакуации указан в следующей таблице.
За исключением оборудования, произведенного до 15 ноября 1993 г., оборудование для восстановления или переработки должно быть сертифицировано организацией по тестированию оборудования, утвержденной Агентством по охране окружающей среды. Чтобы убедиться, что они восстанавливают правильный уровень хладагента, технические специалисты должны использовать оборудование для восстановления в соответствии с указаниями его производителя.
Приборы с пятью или менее фунтами хладагента (малые приборы)
Техники, ремонтирующие мелкую бытовую технику, такую как бытовые холодильники, оконные кондиционеры и кулеры для воды, должны восстановиться:
- 80 процентов хладагента при
- Технический специалист использует оборудование для восстановления или переработки, изготовленное до 15 ноября 1993 г. или
- Компрессор прибора не работает.
- 90 процентов хладагента при
- Технический специалист использует оборудование для восстановления или переработки, изготовленное после 15 ноября 1993 г.
, и
- Компрессор прибора исправен.
- Технический специалист использует оборудование для восстановления или переработки, изготовленное после 15 ноября 1993 г.
Чтобы убедиться, что они восстанавливают правильный уровень хладагента, технические специалисты должны использовать оборудование для восстановления в соответствии с указаниями его производителя.
Технический персонал также может выполнить требования по восстановлению, откачав небольшой прибор до вакуума в четыре дюйма ртутного столба.
Исключения из требований эвакуации
EPA допускает ограниченные исключения из требований по эвакуации для 1) ремонта протекающего холодильного оборудования и оборудования для кондиционирования воздуха и 2) ремонта, который не является капитальным и за которым не следует эвакуация оборудования в окружающую среду.
Ремонт протекающего оборудования
Если технические специалисты не могут эвакуироваться до указанных уровней из-за утечек хладагента или из-за того, что это может привести к существенному загрязнению извлекаемого хладагента, они должны:
- По возможности изолируйте протекающие компоненты от непротекающих компонентов;
- Вакуумировать компоненты без утечек до указанных уровней; и
- Откачайте протекающие компоненты до самого низкого уровня, который может быть достигнут без существенного загрязнения хладагента.
Этот уровень не может превышать 0 фунтов на квадратный дюйм (psig).
Ремонт, не являющийся капитальным и не сопровождающийся эвакуацией
Если техник не эвакуирует оборудование на окружающую среду после завершения ремонта, и если ремонт не является капитальным, то должны быть выполнены следующие требования:
- Для приборов высокого или очень высокого давления, оборудование должно быть откачано до 0 фунтов на квадратный дюйм, прежде чем оно будет открыто.
- Для приборов низкого давления перед открытием в них должно быть повышено давление до 0 фунтов на квадратный дюйм.Методы, требующие последующей продувки (например, азотом) , нельзя использовать, кроме как с приборами, содержащими R-113.
Требование о рекультивации
Собранный хладагент может быть без ограничений возвращен в ту же систему или другие системы, принадлежащие тому же лицу. Однако, если восстановленный хладагент меняет владельца, он должен быть утилизирован. Утилизировано Для целей определения материала как твердых отходов в соответствии с подзаголовком C RCRA материал считается утилизированным, если он перерабатывается для получения годного к употреблению продукта или регенерируется путем его переработки в способ, который восстанавливает его до пригодного для использования состояния.регенератором хладагента, сертифицированным EPA.
Замена масла хладагента
Требования, описанные выше, распространяются на хладагент, содержащийся в масле. Масло в холодильном приборе может содержать большое количество растворенного хладагента. EPA требует снижения давления перед заменой масла, чтобы убедиться, что большая часть хладагента, содержащегося в масле, восстановлена. Замена масла при давлении выше 5 фунтов на кв. дюйм является нарушением.
Существует две приемлемые процедуры восстановления хладагента, содержащегося в масле:
- Вакуумируйте (или создайте давление) холодильный прибор или его изолированную часть до давления не более 5 фунтов на кв.
дюйм, а затем удалите масло; или
- Слейте масло в ресивер системы, который необходимо откачать (или создать под давлением) до давления не более 5 фунтов на кв. дюйм.
Информацию о надлежащей утилизации масла можно найти на веб-сайте Закона о сохранении и восстановлении ресурсов.
Обучение эвакуации системы | Обучение работе с вакуумными системами кондиционирования воздуха
Надлежащая установка и откачка воздуха из системы кондиционирования воздуха начинается с качественной установки и надлежащей практики прокладки трубопроводов.
Получите комплект!
Короткие пути при монтаже комплектов медных трубопроводов приводят к потерям времени при откачке, возможным утечкам хладагента, плохому возврату масла, загрязнению системы и избыточному времени, необходимому для откачки.
Надлежащая эвакуация после первоначальной установки или обслуживания, если
система была открыта для атмосферы, имеет решающее значение для правильной работы
система кондиционирования воздуха. Эвакуация представляет собой двухэтапный процесс:
дегазация и обезвоживание. Дегазация удаляет неконденсирующиеся вещества, которые
вызвать повышенное давление напора и увеличение эксплуатационных расходов.
Там, где часто бывают высокие температуры, неконденсирующиеся вещества в сочетании с влагой также вызывают образование масла.
выход из строя, снижение производительности и повышенный износ компрессора, а также вероятность
отказ.Потери, связанные с неправильной эвакуацией, могут быть очень высокими.
Влажность — вторая проблема. Влага тормозит масло POE в HFC систем (например, R410a), что приводит к преждевременному выходу масла из строя. Потому что POE ломается в его основные компоненты, он может засорить дозатор и загрязняют наборы линий. Это может привести к необходимости полной системы замена. Влажный хладагент и минеральные масла образуют кислоты, которые вызвать отказ системы из-за медного покрытия и повреждения компрессора обмотки.
Вакуумметр используется для определения уровня атмосферы (дегазации и осушки) в системе.
Быстрая и глубокая откачка воздуха из кондиционера или холодильной системы сводится к правильным действиям, включая правильную установку и сборку, защиту от влаги во время изготовления и, конечно же, правильные шланги и датчики для измерения уровня дегазации и обезвоживания. Когда влага (жидкость) попадает в систему или конденсируется, единственным способом ее удаления является пар.Когда дело доходит до удаления воздуха из системы, практически целесообразно удалить только небольшое количество влаги. «Нецелесообразно удалять большое количество воды с помощью вакуумного насоса, поскольку кипящая вода производит большое количество водяного пара. Один фунт воды (около 1 пинты) производит около 867 футов3 водяного пара при температуре 70ºF». (1) Поэтому, по словам Дэвида Бойда из Appion, «Содержите его в чистоте, сухости и герметичности».
- Трубопроводы должны содержаться в чистоте и сухости на протяжении всей установки, влага, грязь и другие загрязнения могут нарушить работу системы и значительно увеличить время, необходимое для вакуумирования.
- Сердечники клапанов должны быть удалены с помощью вакуумного инструмента для стержней, чтобы обеспечить продувку системы азотом и, когда это возможно, перекрыть систему клапанами во время установки трубок.
- Трубогибы следует использовать для минимизации количества фитингов и уменьшения внутренних ограничений. Фитинги требуют резки труб, очистки, удаления заусенцев, сборки, пайки, продувки азотом и проверки на герметичность. Лучше всего отказаться от всех фитингов.Хороший набор сгибателей быстро окупится.
- Обрезанный трубопровод следует рассверлить или удалить заусенцы. Внутренние ограничения могут вызвать эрозию трубопровода, снижение скорости всасываемого газа и плохой возврат масла. Даже несколько неправильно собранных фитингов могут поставить под угрозу качество установки.
- Азот должен быть пропущен через трубопровод во время установки и во время пайки, чтобы избежать попадания загрязнений и влаги в трубопровод, а также во избежание образования оксидов меди во время пайки.
Используйте откалиброванный расходомер, чтобы избежать использования избыточного азота. Продувка системы азотом во время установки значительно сократит время вакуумирования.
- Установите фильтр-осушитель для удаления следов влаги после вакуумирования. Небольшие количества влаги могут задерживаться под компрессорным маслом или, в случае POE, связываться с самим маслом. Осушитель, оснащенный индикатором влажности, установленный непосредственно перед дозирующим устройством, эффективно удаляет следы влаги и помогает быстро выявить потенциальные проблемы с влажностью.Установка осушителя внутри рядом с испарителем лучше защитит дозирующее устройство, обеспечит визуальное присутствие 100% жидкости и предотвратит преждевременную ржавчину осушителя.
Продувка
После установки линий и различных компонентов необходимо убедиться в наличии потока через всю систему путем продувки сухим газом, таким как сухой азот, из линии жидкости на сторону всасывания система. Продувка будет не только удалять небольшие капли воды (если они есть), но и собирать часть влаги из системы.
Испытание под давлением с использованием сухого газа
Испытание на постоянное давление используется для проверки на наличие утечек с использованием снова сухого газа, такого как сухой азот. Мы никогда не надеемся обнаружить утечки в вакууме. (Хотя это действительно случается.) Когда воздух просачивается, вместе с ним появляется влага, удаление которой может занять несколько часов, если ее количество чрезмерно. Испытание под давлением с температурной компенсацией, подобное используемому в цифровых коллекторах серии Testo, сделает процесс быстрым и эффективным. Однако, если вы используете цифровой коллектор, такой как Fieldpiece SMAN, утечки также будут очевидны просто из-за высокого разрешения датчиков давления.При установке типичной жилой системы испытание можно выполнить и проверить примерно за 15 минут. Выполнение этого теста снова соберет некоторую дополнительную влагу, которую не нужно будет удалять в процессе вакуумирования. При выпуске этого газа высокого давления не сбрасывайте давление до атмосферного. Снизьте его примерно до 1 psig. поэтому воздух не может попасть обратно в систему.
Проверка вакуумного насоса (проверка холостого хода)
Подсоедините микрометр прямо к вакуумному насосу через соединение 1/4″ и убедитесь, что насос способен обеспечить уровень вакуума 100 микрон или менее.Насос хорошего качества легко достигает уровней или ниже 50 микрон. Заглушки насоса печально известны своей протечкой, поэтому не полагайтесь на них для изоляции вакуумного насоса. Используйте основные инструменты, чтобы изолировать насос и шланги, чтобы свести к минимуму любую возможность проникновения газа через шланги. Помните, что даже самые лучшие вакуумные шланги будут протекать, поэтому необходима изоляция. Если ваш насос не может достичь 100 микрон или меньше, замените масло на высококачественное масло с низким давлением паров, такое как Appion Tezom.Часто требуется несколько замен масла, чтобы удалить значительное количество влаги из мокрого насоса. По сравнению с поломкой системы масло дешевое, меняйте его часто. Если насос по-прежнему не создает глубокий вакуум, возможно, пришло время его замены или обслуживания.
Примечания по заправке балласта (при наличии)
Вода может удаляться из системы только в виде пара. Если атмосфера, которую вы удаляете из системы охлаждения, насыщена влагой, когда эта влага поступает в насос, она находится в форме пара, она находится в состоянии равновесия с воздухом в системе.Это состояние равновесия и есть то, что подразумевается под балластом. (что-то, что обеспечивает устойчивость)
Балласт, когда он открыт, подает свободный воздух в насос во время такта нагнетания, чтобы удерживать эту влагу в равновесии. Если газовый балласт закрыт, давление, создаваемое в такте нагнетания, будет конденсировать водяной пар и выбрасывать влагу в масло. Открытие балласта во время первоначального опускания мокрой системы поможет предотвратить образование конденсата внутри насоса.(держите его открытым, пока не достигнете 15 000-10 000 микрон)
Влага убивает масло вакуумного насоса. Когда масло влажное, давление пара увеличивается до точки, при которой невозможно создать глубокий вакуум. (мокрое масло — это белое масло) Если масло мокрое, дешевле и быстрее заменить масло, чем позволить газовому балласту отработать его. Эта влага также повредит ваш насос, если вы оставите ее внутри, поэтому всегда меняйте масло, если вы работаете с влажной системой. Причина, по которой я рекомендую вам всегда менять масло, заключается в том, что через маленькое неосвещенное смотровое стекло трудно увидеть, насколько оно мутное.
Открытый газовый балласт не позволяет насосу достичь предельного уровня вакуума и должен быть закрыт после достижения 15 000–10 000 микрон. Используемый газовый балласт используется только во время чернового периода и необходим только при наличии влаги в системе.
Одна из самых важных вещей, которые вы можете сделать, это всегда прокачивать азотом или продувать систему перед вакуумированием. Это означает проталкивание азота через систему от одной стороны к другой БЕЗ значительного повышения давления в системе. Это вытеснит пары влаги, не пропуская их в систему в жидкой форме.
Если вы продуваете систему во время сборки и продуваете систему азотом перед вакуумированием, вам, скорее всего, вообще не понадобится использовать газовый балласт. Газовый балласт эффективен только для удаления небольшого количества влаги, поэтому в очень влажной системе потребуется частая замена масла, если вы хотите быстро выполнить работу.
Откачка
Системы кондиционирования и охлаждения предназначены для работы только с маслом и через них проходит хладагент.Когда обычная система устанавливается и/или обслуживается, воздух и влага попадают в систему. Кислород, азот и влага (все они составляют наш воздух или атмосферу) вредны для работы системы. Удаление воздуха и других неконденсирующихся примесей называется дегазацией, а удаление влаги – обезвоживанием. Удаление обоих обычно называют эвакуацией.
Предполагая, что сердечники клапанов сняты, подсоедините вакуумные шланги большого диаметра к задней части сердечников (не используйте боковые порты сердечника для откачки) как на стороне высокого, так и на низком уровне системы, чтобы обе стороны могли быть опущены одновременно. Хотя поначалу использование шлангов большого диаметра может показаться нелогичным, ценность быстро становится очевидной после начала откачки. Шланги 1/2″ уменьшат время, необходимое для эвакуации, в 16 раз по сравнению с типичными шлангами 1/4″, используемыми в большинстве отраслей. Большие шланги уменьшают трение и, следовательно, увеличивают скорость проводимости. Скорость проводимости 1/4-дюймового шланга настолько мала, что его никогда не следует использовать для эвакуации. По возможности избегайте 1/4-дюймовых шлангов для эвакуации, поскольку они требуют слишком много времени и средств, чтобы быть эффективными.Подсоедините шланги непосредственно к вакуумному насосу с помощью латунного тройника или вакуумного коллектора. Не используйте коллекторы, не снабженные уплотнительными кольцами, так как сальник часто выдерживает давление, но протекает в вакууме. Сведите количество подключений к минимуму, а количество точек доступа — к максимуму. Другими словами, подключитесь к как можно большему количеству мест в системе, но исключите ненужные шланги или фитинги.
Если доступны только две точки доступа, подключите их напрямую к вакуумному насосу, что избавит вас от необходимости использовать коллектор.
Установите высококачественный вакуумметр с медной линией или латунным разъемом непосредственно на сердечник, установленный на линии всасывания. Это позволит полностью изолировать оборудование для откачки (шланги и фитинги) от системы во время «испытаний постоянным давлением», в ходе которых будет измеряться качество вакуума.
Начните со свежего и сухого масла для вакуумного насоса. Масло для вакуумных насосов чрезвычайно гигроскопично (впитывает влагу), поэтому, начиная с свежего масла, все пойдет намного быстрее. Если ваш насос оснащен газовым балластом, откройте балласт до уровня 10000 микрон.В узких пределах назначение вакуумного балласта состоит в том, чтобы предотвратить конденсацию паров воды в насосе во время такта нагнетания. Вообще говоря, лучше и быстрее заменить масло, чем ждать, пока газовый балласт удалит лишнюю влагу из масла во время работы насоса. Влага разрушает масло вакуумного насоса, увеличивая давление его паров настолько, что высокий уровень вакуума не может быть создан. Насос не может создать более высокий вакуум, чем давление паров герметика.Если сомневаетесь, меняйте!
1-е постоянное испытание
Вакуум до достижения уровня 1000 микрон (при использовании шлангов большого диаметра и стержневых инструментов откачка трубопровода и змеевика испарителя займет менее 15 минут для типичной бытовой системы до до 5 тонн). Изолируйте вакуум с помощью основных инструментов, позволяя насосу продолжать работать, и запишите уровень утечки (приблизительно после 5-минутного периода стабилизации), указанный вакуумметром, если он установлен. Скорость утечки просто определяется падением вакуума в единицу времени, обычно отображаемым в микронах в секунду.Повышение давления после короткого периода стабилизации указывает на наличие влаги в системе или наличие небольшой утечки в системе.
2nd Standing Test
Откройте основные инструменты и дайте системе продолжить процесс вакуумирования, пока уровень вакуума не станет 500 микрон или меньше. Затем повторите «постоянный тест», чтобы определить, есть ли снижение скорости утечки после стабилизации вакуума. Если утечки нет, то 2-я скорость утечки в системе должна быть значительно меньше первой, что свидетельствует о прогрессе в работе по обезвоживанию.
Различие между влагой и утечкой в системе
Если скорость утечки не уменьшилась, могут произойти две вещи:
1) Система все еще загрязнена влагой. (Возможно, застрял под компрессорным маслом.)
2) В системе есть небольшая утечка, которая не была обнаружена при первоначальном испытании под высоким давлением. (Некоторые утечки более заметны в вакууме, чем под давлением.)
Высококачественный вакуумметр с высоким разрешением, подобный тем, которые можно найти на этой странице «Измерение вакуума», может выявить утечку гораздо быстрее, чем манометр, благодаря чувствительности прибора.Несмотря на то, что микронный манометр вполне эффективен, проверка на утечку в вакууме не является приемлемой практикой по сравнению с испытанием на постоянное давление, поскольку в процессе вакуумирования в систему втягивается влага. Если вы обнаружите утечку под вакуумом, разбейте вакуум сухим азотом и попытайтесь найти ее под давлением. НЕ открывайте систему в атмосферу под вакуумом! Это подрывает все ваше время и усилия до этого момента.
Если в системе есть утечка, показания вакуумметра будут продолжать расти, пока не будет достигнуто атмосферное давление.Однако, если система герметична, но все еще содержит влагу, рост выравнивается, когда давление паров в системе выравнивается, как правило, между 20 000 и 25 000 микрон в диапазоне от 72° до 80° F. В этот момент показания вакуума станут стабильными. (Примечание: система, которая продолжает выравниваться на уровне 3500-4500 микрон, может превратить влагу в лед. В этом случае может потребоваться повышение температуры системы с помощью внешнего источника тепла, чтобы удалить влагу из системы.)
Если система показывает влажность, многократная продувка азотом значительно уменьшит количество влаги в системе.Чтобы выполнить эту процедуру, уменьшите давление в системе до 1000–2500 микрон. Изолируйте вакуумный насос с помощью основных инструментов и отсоедините вакуумный шланг от нижней стороны системы. Разорвите вакуум в системе с помощью азота, введенного в боковой порт основного инструмента. Разбейте вакуум азотом до уровня, эквивалентного атмосферному давлению (760 000 микрон), затем продуйте систему азотом под давлением 1–3 фунта на кв. дюйм. от высокой к низкой стороне, позволяя ему выходить через открытый порт основного инструмента.Не повышайте давление в системе, так как это не удалит влагу. Нет необходимости повышать давление в системе, если только вы не выполняете проверку на утечку. Увеличение давления в системе фактически приведет к тому, что вода будет выпадать из азота, подобно тому, как это происходит со сжатым воздухом в воздушном компрессоре. Азот не поглощает воду, а увлекает ее и помогает двигаться дальше из системы, позволяя жидкой воде нагреваться, испаряться и повышать давление водяного пара без введения дополнительной влаги в систему.Если система высыхает, вы заметите, что более глубокие уровни вакуума быстро достигаются, что указывает на прогресс в работе по обезвоживанию.
При желании или необходимости повторяйте этот процесс до тех пор, пока влага не будет удалена. Обычно требуется не более трехкратной эвакуации с зачисткой. Если в ходе этого процесса не будет достигнут заметный прогресс, повторите продувку азотом, чтобы удалить жидкую влагу, которая может существовать. Если обнаружена утечка, она должна быть устранена до завершения вакуумирования.
После второго испытания на падение проверьте состояние масла вакуумного насоса.Молочное масло содержит влагу и не позволяет достичь окончательного вакуума из-за повышения давления паров и потери герметичности, вызванной влагой в масле. Если масло мокрое, замените его чистым сухим маслом. Если сомневаетесь, меняйте!
Окончательный вакуум
После второго постоянного испытания дайте вакуумному насосу поработать до тех пор, пока размер системы не станет предпочтительно ниже 200 микрон. (С хорошим насосом легко достижимо 50-100 микрон.) Изолируйте вакуумную установку с помощью основных инструментов и дайте системе постоять от 15 до 30 минут. Если микронный уровень не поднимается выше 500 микрон, вакуумирование завершено. Если давление поднимется выше 500, снова откройте керновые инструменты и дайте продолжить откачку. Опыт и/или микрометр с высоким разрешением позволят сократить время оценки.
После завершения вакуумирования, если вы работаете с новой установкой, держите насос изолированным и откройте (взломайте) линию всасывания, впуская небольшое количество хладагента в систему, постепенно создавая в системе положительное давление.(Примечание: когда вакуумметр показывает «высокое давление», вы находитесь выше 20 000 микрон, но все еще находитесь в отрицательном давлении.) Поскольку манометр может выдерживать давление до 500 фунтов на квадратный дюйм, вам не нужно беспокоиться о повреждении микронного манометра из-за избыточного давления. После того, как линия всасывания полностью открыта, откройте клапан подачи жидкости, установите на место сердечники клапана и снимите вакуумметр и инструменты для сердечника. (Примечание: хладагент может привести к срабатыванию датчика вакуума, если он находится под вакуумом или неустойчиво после удаления до тех пор, пока пары хладагента не выйдут из датчика.Датчик откалиброван для воздуха, и атмосфера хладагента повлияет на показания.) После того, как сердечники установлены и инструменты для сердечников удалены, очистите шланги коллектора и установите манометры, чтобы завершить ввод системы в эксплуатацию.
При техническом обслуживании и существующей установке перед снятием основных инструментов снимите вакуум с требуемым системным хладагентом, затем продолжите процедуру ввода в эксплуатацию в соответствии с требованиями производителя.
Заключение
Мы рекомендуем Accutool BluVac по нескольким причинам.Он имеет ряд преимуществ перед всеми другими вакуумметрами. Были решены проблемы с загрязнением масла, полевой калибровкой и рабочим процессом. С разрешением 0,1 микрон вы можете легко увидеть, набирает ли силу вакуумный насос, нуждается ли замена масла в вакуумном насосе, а когда манометр изолирован, падение вакуума и предельное давление в системе. Из-за разрешающей способности BluVac мы настоятельно рекомендуем использовать вакуумные инструменты и шланги. Все шланги протекают, и при разрешении 0,1 микрона это будет очень заметно.
Для правильного выполнения эвакуации используйте комплект RapidEvac от TruTech Tools. При использовании, как показано, время эвакуации сократится в 16 раз для шлангов диаметром 1/4 дюйма. Экономия трудозатрат при использовании этого комплекта очень существенна и снизит потребность в рабочей силе и время простоя обслуживаемого оборудования.
Ищете идеальную вакуумную установку? Не смотрите дальше, у нас есть это. ВАКУУМНАЯ УСТАНОВКА
Рекомендации:
Рекомендации:
(1) Технология холодильного кондиционирования воздуха 5-е издание Copyright 2005
(2) Обзор вакуума для сервисных инженеров 1988
Увеличение влаги в системах HVAC
Глубокие вакуумные требования
Начнем с самого вакуумного насоса. Вакуумные насосы оцениваются в CFM (кубических футах в минуту), и больше не всегда означает лучше или быстрее. В отличие от нагнетательного насоса, когда мы увеличиваем CFM вакуумного насоса, мы не обязательно увеличиваем скорость откачки. Находясь в вакууме, ограничения в откачиваемой системе (сердечники Шредера, адаптеры Шредера и диаметр шланга) определяют скорость, с которой вы можете откачивать больше, чем сам размер насоса. Согласно J/B, вакуумный насос на 7 кубических футов в минуту подходит для перекачивания до 49 тонн, а насос на 3 кубических футов в минуту — до 9 тонн.
Подключение насоса
При подсоединении вакуумного насоса рассмотрите возможность использования дренажного шланга диаметром 3/8 дюйма. По словам производителей вакуумных насосов, шланг диаметром 1/4 дюйма выдерживает только 1 кубический фут вакуума в минуту. За счет увеличения выпускного шланга коллектора до 3/8 дюйма скорость откачки также будет увеличена. Крайне важно всегда вытягивать вакуум как из сервисных отверстий на стороне высокого, так и на стороне низкого давления. Затем удалите сердечники Schrader из сервисных портов во время эвакуации с помощью инструмента для удаления сердечников.На этом инструменте есть клапан, который можно использовать во время теста удержания вакуума.
Замена масла
Необходимо менять масло перед каждым вакуумированием. Это может показаться большим, но большая часть влаги, которую вы удаляете из системы, конденсируется в масле. Вакуумный насос с влажным грязным маслом не будет работать так же хорошо, как тот же насос с чистым сухим маслом. Всегда следует использовать вакуумный насос с газовым балластом, который необходимо открыть в начале вакуумирования. Это поможет предотвратить конденсацию сильной влаги в начале откачки в насосе и загрязнение масла.Имейте в виду, что многие более дешевые насосы не имеют газового балласта. В более крупных системах или в очень влажных системах может потребоваться замена масла во время вакуумирования.
Измерение вакуума
Составной нижний манометр предназначен для измерения давления, а не вакуума. Он показывает 30 дюймов ртутного столба (дюймы ртутного столба) и не является точным показателем вакуума. Микронный датчик измеряет в микронах и является намного более точным. 1 дюйм ртутного столба равен 25 400 микронам, а 30 дюймов ртутного столба равен 762 000 микронам. Микронный манометр никогда не следует подключать через сервисные шланги, а следует подключать непосредственно к системным сервисным портам.Инструмент для вакуумирования или шаровые краны для сервисных шлангов можно затем использовать для изоляции ваших шлангов от вакуумируемой системы во время испытания на удержание вакуума. Имейте в виду, сервисные шланги и прокладки могут протекать, что может выглядеть как утечка в системе.
Вакуумный тест
После достижения вакуума в 500 микрон или ниже изолируйте систему от сервисных шлангов, коллектора и вакуумного насоса на клапанах вакуумного инструмента или шаровых кранах шлангов. Вакуум должен стабилизироваться и оставаться ниже 500 микрон. Если вакуум поднимается медленно и останавливается, в системе есть влага, и вакуумирование следует продолжить.Если вакуум поднимается до атмосферного давления, у вас есть утечка, которую необходимо устранить. Если вы можете поддерживать вакуум на уровне 500 микрон или ниже, то вы знаете, что у вас чистая, сухая и герметичная система кондиционирования воздуха или охлаждения.
Вы домовладелец или владеете коммерческой недвижимостью? Посетите сайт mybryantdealer.com, чтобы найти ближайшего к вам дилера Bryant!
Восстановление хладагента из приборов/стационарных источников
Постановление 40 CFR 82, подраздел F, применяется к вашему объекту, если вы извлекаете хладагент из приборов или других стационарных источников, таких как кондиционеры (не автомобильные кондиционеры) и холодильного оборудования, перед удалением/переработкой.Эти правила запрещают целенаправленную вентиляцию и сводят к минимуму случайные выбросы озоноразрушающих соединений хладагентов (ХФУ, ГХФУ и их смесей) во время обслуживания и/или утилизации кондиционеров и холодильного оборудования. Эти правила не распространяются на рекуперацию хладагента из автомобильных кондиционеров (MVAC) или транспортных средств, подобных MVAC (тракторов, тяжелой техники, лодок и т. д.), которые подпадают под действие 40 CFR 82, подраздел B.
Эти правила устанавливают сертификационные требования к оборудованию для переработки и регенерации, а также для технических специалистов и специалистов по регенерации хладагентов.Продажа хладагента разрешена только сертифицированным специалистам. Лица, выполняющие обслуживание или утилизирующие кондиционеры или холодильное оборудование, должны подтвердить Агентству по охране окружающей среды, что они приобрели надлежащее оборудование и соблюдают эти правила. Наконец, эти правила требуют устранения существенных утечек из кондиционеров и/или холодильного оборудования, а также устанавливают требования по обеспечению надлежащей эвакуации и утилизации оборудования, попадающего в поток отходов с неповрежденной загрузкой.
Запрет на вентиляцию
Строго запрещен целенаправленный сброс хладагента во время технического обслуживания, ремонта или утилизации кондиционеров и холодильного оборудования. Допускаются только четыре конкретных типа релизов.
- Минимальные количества в ходе добросовестных усилий по возврату хладагента
- Хладагент, выбрасываемый в процессе нормальной эксплуатации кондиционеров и холодильного оборудования, например, при механической продувке
- Выбросы ХФУ и ГХФУ, не используемых в качестве хладагентов
- Небольшие выбросы хладагента в результате продувки шлангов или при подсоединении или отсоединении шлангов для зарядки или обслуживания приборов
Требования к эвакуации
При открытии оборудования технические специалисты должны откачать хладагент до установленного уровня вакуума.Требуемые уровни зависят от того, когда было изготовлено используемое оборудование и какой тип откачиваемого хладагента. См. Таблицу 1 ниже.
Специалисты по ремонту мелкой бытовой техники (оконные кондиционеры, бытовые холодильники и кулеры для воды) должны восстановить 80% хладагента, если используется оборудование для откачки, изготовленное до 15 ноября 1993 г. , или компрессор в приборе не работает.
Техники, ремонтирующие небольшие бытовые приборы, должны восстановить 90% хладагента, если они используют оборудование для откачки, изготовленное 15 ноября 1993 г. или позже, и компрессор в приборе работает.
Загрузите PDF-файл справа для требуемых уровней оценки хладагента из приборов.
Сертификация оборудования
Если эвакуационное оборудование было изготовлено 15 ноября 1993 г. или позже, оно должно быть сертифицировано одобренной EPA организацией по тестированию оборудования, такой как Underwriters Laboratories (UL) или Институт кондиционирования и охлаждения воздуха (ARI). На сертифицированном оборудовании будет напечатано следующее: «Это оборудование было сертифицировано ARI/UL на соответствие минимальным требованиям Агентства по охране окружающей среды в отношении оборудования для переработки и/или восстановления, предназначенного для использования с (вставленным устройством соответствующей категории)».
EPA требует, чтобы лица, выполняющие техническое обслуживание или утилизацию холодильного оборудования, приобретали надлежащее оборудование и уведомляли соответствующее региональное отделение EPA об использовании такого оборудования, а также подтверждали выполнение применимых требований. Этот сертификат должен быть подписан владельцем/оператором. Образец формы сертификата прилагается.
Утечки хладагента
Владельцы оборудования с заправкой более 50 фунтов обязаны устранять утечки хладагента из такого оборудования, когда все утечки вместе приводят к потере определенного процента от общего количества хладагента в течение одного года.
- Утечки в коммерческом/промышленном оборудовании должны быть устранены, если скорость утечки приведет к потере 35% заряда хладагента в течение одного года; и
- Для всего остального оборудования утечки должны быть устранены, если скорость утечки приведет к потере 15% заряда хладагента в течение одного года.
Существуют более подробные требования к устранению утечки хладагента в зависимости от плана использования/списания оборудования, если требуется отключение для ремонта и т. д.
Сертификация техника
Для тех, кто занимается техническим обслуживанием, обслуживанием или ремонтом, существует программа сертификации технических специалистов.Техник – это человек, который прикрепляет/отсоединяет шланги и манометры к приборам и от них для измерения давления внутри прибора; добавление хладагента в прибор или удаление хладагента из прибора; или любые другие действия, которые могут нарушить целостность небольшого прибора.
Типы сертификации
- Обслуживание мелкой бытовой техники
- Обслуживание или утилизация приборов высокого или очень высокого давления, кроме небольших приборов и MVAC
- Обслуживание или утилизация приборов низкого давления
- Сервис на всех видах техники (Универсальный)
Сертификацию можно получить, пройдя одобренный EPA тест, проводимый одобренной EPA сертифицирующей организацией. На горячую линию EPA по защите от озона (800-296-1996) или в IWRC можно обратиться, чтобы получить список сертифицирующих организаций, утвержденных EPA. Сертификация технического специалиста не требуется для тех, кто удаляет хладагент из приборов в потоке отходов, который может обоснованно выбрасывать хладагент в атмосферу.
Продажа хладагентов
Продажа хладагента в контейнерах любого размера разрешена только сертифицированным техническим специалистам, как описано выше, или сертифицированным в соответствии с правилами MVAC. Это ограничение на продажу распространяется на хладагент в контейнерах (баллонах/бочках) и предварительно заправленные детали.Он не включает хладагент, содержащийся в холодильниках/кондиционерах воздуха с полностью собранными контурами хладагента. Он также не включает чистые хладагенты ГФУ, ХФУ или ГХФУ, не предназначенные для использования в качестве хладагента.
Утилизация холодильного оборудования
Оборудование, которое обычно попадает в поток отходов с неповрежденной заправкой хладагента (MVAC, бытовые холодильники и морозильники, комнатные кондиционеры и т. д.), подпадает под особые требования по безопасной утилизации. Последнее лицо в цепочке утилизации несет ответственность за удаление хладагента из всего оборудования перед окончательной утилизацией оборудования.Лица «выше по течению» могут удалять и правильно утилизировать хладагент до того, как оборудование достигнет стадии окончательной утилизации. Они должны предоставить документацию о его удалении последнему человеку в потоке отходов.
Те же стандарты производительности требуются для оборудования, используемого для восстановления хладагента на этапе окончательной утилизации, однако такое оборудование не требует тестирования в лаборатории. Это позволяет создавать оборудование самостоятельно, если оно соответствует следующим стандартам производительности.
- MVAC и устройства, подобные MVAC — вакуум 102 мм ртутного столба
- Для небольших бытовых приборов — эффективность 90%, когда компрессор устройства работает, и 80%, если компрессор не работает
Утилизация хладагента
Если хладагенты перерабатываются или перерабатываются, они не считаются опасными отходами. Кроме того, отработанные масла, загрязненные ХФУ, не являются опасными отходами, если масла не смешиваются с другими отходами, подвергаются переработке или утилизации ХФУ и не смешиваются с отработанными маслами из других источников.
Процесс вакуумирования системы хладагента чиллера
Черный день из-за поломки чиллера для нашего инженера на Северо-Западе.
Новости Статья №8
Электрические неисправности при выходе из строя чиллера
Наш клиент вызвал нас, потому что у него были электрические неисправности чиллера. Электропитание части панели пропало, и ему потребовалась наша помощь. Наш инженер нашел перегоревший предохранитель, заменил его и проверил работоспособность — снова перегорел.Используя свой мультиметр, он проследил диагностику до замыкания на землю реле потока…
Реле протока системы водоснабжения
Пароизоляция реле потока вышла из строя, что привело к попаданию дождевой воды. Это вызвало замыкание на землю в цепи управления 240 В и перегорание предохранителя. Клиент тут же оформил заказ, и наш инженер заменил реле потока на шток от своей машины. У каждого из наших инженеров есть ряд реле расхода для различных применений…
Нержавеющая сталь
Там, где химикаты системы водоснабжения вызывают коррозию, мы предлагаем реле потока, устойчивые к коррозии.Этот тип имеет более длительный срок службы из-за использования нержавеющей стали. Они дороже из-за более высоких производственных затрат, но они стоят своих денег, поскольку с меньшей вероятностью выйдут из строя, что приведет к потенциальной потере производства.
Наружное использование
Этот тип был установлен нашим инженером на месте в этой новостной статье. Он был разработан и испытан в различных неблагоприятных погодных условиях, включая мороз и сильный дождь. Электрическое и коммутационное отделение защищено уплотнительным сальником для защиты от непогоды.Резиновое уплотнительное кольцо обеспечивает герметичность этого отсека.
Внутреннее использование
В некоторых приложениях реле протока расположено внутри здания в машинном зале, а кабель управления проходит к элементам управления чиллером. Другая конфигурация позволяет переключателю потока отключать систему управления зданием и, таким образом, отключать сигнал работы чиллера. В любом случае нет необходимости в защите от атмосферных воздействий. Этот тип переключателя потока дешевле из-за более низких затрат на строительство.
Высокое давление
Некоторые водные системы работают под значительным давлением. Поэтому для этого применения были разработаны реле расхода высокого давления. Они способны предотвратить попадание воды из водопроводной системы в отсек электрооборудования и коммутации.
Проверка и регулировка
Наш инженер провел тестирование и настройку реле потока, чтобы убедиться в его надежной работе. Он добился этого, отслеживая показания и измерения системы водоснабжения в соответствии с проектными спецификациями переключателя.Когда все успокоилось, заменил предохранитель и побежал тестировать чиллер…
0161 370 7193
service@maximuschillers. com
✎ Контактная форма
Вентиляторы конденсатора
Вентиляторы конденсатора сначала вообще не включались, а затем работали медленно. Они управляются регулятором скорости вращения вентилятора, который чувствителен к давлению. На вентиляторы подается минимальное значение вольт, чтобы предотвратить остановку и перегрев внутренних обмоток двигателя.Вентиляторы оказались в исправном состоянии, поэтому он решил обратить внимание на…
Зависимость давления от температуры хладагента
Было обнаружено более низкое давление и, следовательно, более низкая температура в конденсаторе. После тщательного поиска неисправностей и диагностики, включающей ввод значений давления и температуры в калькулятор, наш инженер решил, что в чиллере не хватает хладагента. Это согласуется с законом постоянного объема Чарльза. Это один из фундаментальных научных принципов работы чиллера: чем выше давление, тем выше температура, чем ниже давление, тем ниже температура.
Блоки регенерации хладагента
Получив еще один заказ от нашего клиента, мы разрешили нашему инженеру использовать его установку для декантации газа. Хладагент всасывается в агрегат с помощью небольшого одноцилиндрового поршневого компрессора. Компрессор разряжается во встроенный конденсатор, который охлаждается вентилятором. Переохлажденный хладагент стекает по шлангу хладагента, который, как показано на рисунке, подсоединен к цилиндру регенерации. После того, как этот процесс был завершен, он начал искать утечку…
Испытание на герметичность и испытание под давлением
Обнаружена течь на фланце расширительного клапана. Этот компонент был удален, очищен нашим растворителем для хладагентов, затем соединение было восстановлено с помощью компаунда, подходящего для температурного диапазона компонента. После удовлетворительного испытания давлением азота можно начинать процесс вакуумирования…
0161 370 7193
service@maximuschillers. com
✎ Контактная форма
Вакуумные насосы системы хладагента
Каждый из наших инженеров имеет высокопроизводительный вакуумный насос высочайшего качества.Мы считаем необходимым инвестировать в современное оборудование, так как это часть того, как мы поставляем MAXIMUS ADVANTAGE™ Любой чиллер — Любая проблема — Любая деталь — Любой хладагент — Везде. Хорошее оборудование облегчает работу.
Лопастной насос
Насос работает, всасывая пар во впускное отверстие. Вращающаяся лопастная система извлекает пар и выпускает его через верхнюю часть модуля насоса. Масло используется для смазки лопастей, которые скользят вокруг цилиндра насоса. Лопасти плотно прилегают к цилиндру с помощью пружин.Поскольку наши насосы имеют большую производительность, на выпускном отверстии установлен масляный фильтр с сеткой внутри для улавливания капель масла.
Электродвигатель
Этот двигатель устанавливается на заднюю часть модуля лопастного насоса. Он поставляется с заводской настройкой на 240 В, но мы меняем контакты для электрических соединений, чтобы преобразовать его для использования с 110 В. Это связано с тем, что клиенты и инженеры требуют использования 110 В, как будто это безопаснее для использования в климате Великобритании. Вилки 110 В и удлинительный кабель защищены кожухом и устойчивы к атмосферным воздействиям.Устойчивость к атмосферным воздействиям не означает устойчивость к атмосферным воздействиям, поэтому мы принимаем меры по ограничению воздействия неблагоприятных погодных условий. Однако двигатель насоса совсем не устойчив к атмосферным воздействиям, поэтому необходимо позаботиться о том, чтобы разместить его в сухом месте. После длительной работы двигатель нагревается, поэтому наши инженеры снимают показания и выполняют регулировки, чтобы убедиться, что он остается в номинальном диапазоне рабочих температур.
Замена масла при поломке чиллера
Масло для вакуумного насоса заменяется перед каждым использованием нашим высококачественным маслом специального сорта. Свяжитесь с нашим офисом, чтобы узнать цены и сроки доставки. Производитель насоса рекомендует эту замену масла, так как влага и примеси впитываются в масло и, таким образом, снижают его производительность, а также работу насоса.
0161 370 7193
service@maximuschillers.com
✎ Контактная форма
Откачка системы хладагента
Настроив вакуумный насос, наш инженер начал процесс эвакуации.
Торр-манометры, использованные во время поломки чиллера
Мы используем аналоговые торр-манометры, так как они более надежны, чем цифровые.Также им не нужны батарейки и неважно, промокнут ли они. Наш инженер прикрепил манометр Torr к подходящей части системы с помощью шланга для хладагента, обеспечив хорошее уплотнение между компонентами с помощью герметика.
Фитинги, использованные при поломке чиллера
Фитинги использовались для соединения различных типов резьбы от вакуумного насоса до холодильной системы. Прогрев насос полчаса, он был готов приступить к процессу.
Неконденсируемые компоненты удалены во время поломки чиллера
Одной из целей вакуумирования является удаление газов, которые не будут конденсироваться, таких как азот, оставшихся в системе после испытаний под давлением.Другим неконденсируемым воздухом является воздух, который попал в систему после удаления расширительного клапана. Эти неконденсирующиеся газы влияют на работу холодильной системы в соответствии с законом парциального давления Дальтона: все газы в сосуде действуют так, как если бы они были сами по себе. Неконденсирующиеся газы вызывают более высокое давление в конденсаторе. Когда это давление добавляется в наши расчеты, сумма выбрасывается и, таким образом, дает ложное значение переохлаждения.
Обезвоживание во время поломки чиллера
Другой целью вакуумирования является обезвоживание системы.Вода, как известно, имеет температуру кипения 100°C на уровне моря, что соответствует 1 бару абсолютного давления или 760 торр. По мере того, как вы начинаете падать давление, соответственно падает и температура кипения. Например, вода на вершине Эвереста кипит при температуре около 68°C. Если мы продолжим вакуумировать систему хладагента, в конечном итоге мы сможем удалить всю влагу, снизив давление ниже точки насыщения воды. Это работает даже зимой в условиях окружающей среды в Великобритании. Влага в системе вызывает системные сбои и неисправности, приводящие к дорогостоящим поломкам.
Связанные статьи:
Обслуживание холодильной установки
Система охлажденной воды EEV Service
Обслуживание водяной системы испарителя
Обслуживание чиллера HFC
Вакуумная служба технологического чиллера
Компания по обслуживанию чиллеров
Обслуживание промышленных чиллеров
Сервисная компания чиллеров Посещение
Поиск и диагностика чиллеров
Проверка герметичности охладителя фторсодержащих газов
Ввод в эксплуатацию чиллера
Испытание конденсатора чиллера с воздушным охлаждением
Вызов чиллера
Проблемы с чиллером
Отказ чиллера
Чтобы узнать больше о вентиляторах конденсатора чиллера, нажмите на тег вверху страницы.
Подробнее о пластинчато-роторных насосах читайте в Википедии
Вакуумирование и обезвоживание холодильных систем — Технический паспорт
Влага в системе охлаждения
Любое количество влаги или воды в системе охлаждения является просто катастрофическим и в конечном итоге приведет к серьезному отказу и обширной очистке системы. Крайне важно, чтобы на всех этапах процедуры установки, обслуживания и ремонта определялась и удалялась влага из системы.Небольшие количества влаги вступают в реакцию с хладагентом и маслом, что приводит к их кислотности. Когда он прокачивается по системе, он образует электролитическое медное покрытие на всех стальных поверхностях, таких как компрессор, клапаны и внутренние органы управления. Эти отложения меди уменьшают зазоры в подшипниках и могут вызвать заедание некоторых компонентов. Кислота также вступает в реакцию с изоляцией обмоток двигателя и может вызвать электрическое перегорание герметичных или полугерметичных двигателей компрессоров.
Влага также может вызвать следующее:
- Шлам, который может блокировать масляные фильтры, уменьшая поток масла и увеличивая износ компонентов.
- Это может вызвать ограничение в устройстве расширения. Это, следовательно, понизит температуру на отверстии, что приведет к замерзанию влаги и закупорке.
- Большие количества воды вызовут засорение сердцевин фильтра-осушителя, а также могут вытеснить объем масла при перекачивании по системе.
Процедура настройки
- Подсоедините линии как к высокой, так и к низкой стороне системы.
- Всегда используйте манометр Torr, подключенный в самой дальней точке от вакуумного насоса.
- Если шланги манометра коллектора находятся в плохом состоянии, рассмотрите возможность использования медных линий для подключения к вакуумному насосу.
Одновакуумный метод
Глубокий или одиночный вакуум пытается достичь давления 2 Торр за одну попытку или за один этап.
Вакуумный насос подключается к сторонам высокого и низкого давления системы и работает до тех пор, пока не будет достигнуто давление 2 Торр или ниже. Как только давление достигает 2 Торр, насос отключается, и в течение как минимум одного часа выполняется испытание подъемом давления (испытание отрицательным давлением).
Метод тройного вакуума
Метод тройного вакуума в основном используется на более крупном оборудовании и является предпочтительным способом удаления влаги из системы. После достижения вакуума приблизительно 10 Торр используйте OFN (бескислородный азот) в качестве осушителя, чтобы поглотить всю влагу из воздуха. Этот метод можно использовать при низкой температуре окружающей среды, так как он помогает испарить любую влагу и ускорить процесс вакуумирования.
Последовательность для тройного пылесоса:
- Система прошла испытания на прочность/герметичность, OFN стравливался контролируемым образом.
- Подсоедините вакуумный насос и манометры к сторонам высокого и низкого давления системы.
- Вакуумируйте систему, пока не будет достигнуто давление 10 торр или ниже.
- Отключите вакуумный насос и манометр Torr, затем с помощью OFN доведите давление до 0 бар.
- Вакуумный насос перезапускается, манометр Торр открыт и достигается давление 5 Торр или ниже.
- Вакуумный насос и манометр Torr отключаются, и OFN вводится до тех пор, пока снова не будет достигнуто 0 бар.
- Вакуумный насос перезапускается, манометр Торр открыт и достигается давление 2 Торр.
Чтобы убедиться, что в системе нет утечек, давление должно поддерживаться без значительного повышения в течение как минимум одного часа с отключенным вакуумным насосом.
Примечание . Во время вакуумной процедуры любого типа убедитесь, что все клапаны и соленоиды открыты. Это гарантирует отсутствие «карманов» воздуха или азота в трубопроводе. Если компонент закрыт или ограничен, подсоедините шланг к обеим сторонам компонента.
ДЛЯ ДОПОЛНИТЕЛЬНОЙ ИНФОРМАЦИИ О РЕМОНТЕ ХОЛОДИЛЬНЫХ СИСТЕМ ПРИСОЕДИНЯЙТЕСЬ К НАШЕЙ ГРУППЕ В FACEBOOK
Зачем делать тройную эвакуацию для AC
Смазка для локтей работает, не так ли? Независимо от того, моете ли вы тарелку, протираете машину губкой или чистите унитаз, дополнительные усилия приведут к более качественной уборке.
То же самое касается комплектов трубопроводов кондиционера, трубок, по которым циркулирует хладагент. Мы всегда очищаем их перед установкой нового блока, и мы используем проверенную методику, которая оставляет наборы линий в первозданном виде.
Зачем нужно чистить комплект линий?
Поскольку любой материал внутри комплекта трубопроводов, кроме масла или хладагента, может помешать правильному охлаждению системы.
Если ваш старый кондиционер сгорел, он мог оставить кислотный осадок внутри комплекта проводов. Вам нужно убрать этот осадок. Комплект трубопроводов также должен содержать только подходящие типы масла и хладагента. Другими словами, вы не хотите, чтобы R-22 или минеральное масло оставалось, когда вы устанавливаете новую систему, использующую хладагент R-410A.
Чаще всего мы можем повторно использовать существующие наборы линий при установке нового кондиционера. Иногда нам приходится использовать их повторно, потому что они проходят сквозь стены и их было бы чрезвычайно сложно (и дорого) заменить. Но даже когда мы устанавливаем совершенно новый, мы сначала тратим время на его очистку.
Оно того стоит. Вы столкнетесь с меньшим количеством проблем в будущем. Игра слов.
Процесс, который мы используем для очистки наборов линий, называется тройной эвакуацией. Мы буквально «эвакуируем» влагу, песок и другие остатки из комплекта лески.И мы делаем это три раза, чтобы убедиться, что все ушло.
Но есть и другие вещи, которые мы делаем.
Чтобы получить действительно чистые наборы линий, мы следуем этим процедурам.

Помните, когда вы учились в школе и сдали задание, которое было не совсем, ну… тщательно изучено? Знаешь, что-то, что было не совсем твоей лучшей работой? Вот что случилось: ты получил плохую оценку.
И из-за одной плохой оценки было трудно получить хорошую оценку в классе в этом семестре.
То же самое происходит, когда техник HVAC выполняет не очень качественную очистку линии. Они не удаляют все загрязнения. В долгосрочной перспективе ваш кондиционер не будет работать очень хорошо и может полностью выйти из строя. Фигово.
Решение, как всегда, сделать правильно с первого раза. Поэтому мы всегда:
- Промойте трубопровод азотом. Струя азота упрощает процесс тройной эвакуации.Азот вымывает много мусора, так что пылесосу не приходится работать так усердно.
- Контролируйте линию, установленную на обоих концах. Многие подрядчики просто дуют азотом в трубопровод и хлопают себя по плечу. На самом деле мы помещаем техника на каждом конце набора линий.
Таким образом, мы можем визуально отслеживать наш прогресс. Если будет много мусора, мы об этом узнаем. Затем мы продуем еще немного азота через систему.
- Пропылесосьте комплект линий. С помощью вакуумного насоса и специальных шлангов отсасываем весь оставшийся мусор и влагу — все, что может помешать циклу охлаждения. Мы также продуваем линию азотом после каждого вакуумного цикла.
- Снова пропылесосить. Хорошо. Сейчас у нас двойная эвакуация. Снова промываем магистраль азотом…
- Снова пропылесосить . …и тройная эвакуация! Начать дополнительную промывку азотом.
- Измеряйте прогресс с помощью цифрового микрометра. Это шаг, на который не каждая компания обращает внимание. Вместо того, чтобы просто надеяться, что мы получили все из набора линий, мы на самом деле измеряем вещи до микрона. Таким образом, мы будем знать, достаточно ли чист набор строк для повторного использования, а когда нет.
- Повторяйте, пока датчик не покажет 300 микрон или меньше. Это наш порог. Если после трехкратной эвакуации в трубопроводе остается более 300 микрон загрязнений, мы повторяем процесс.
Когда мы закончим, ваш набор лесок будет чист, как свисток, и все получат хорошие оценки.А твой новый кондиционер? Скажем так, более чистый набор лески поможет максимально увеличить срок ее службы.
Поэтому обязательно узнайте в своей компании по ОВКВ, как они очищают комплект трубопроводов.
Все, кроме тройной эвакуации, должно быть тревожным сигналом. В некоторых кругах можно было бы считать «достаточно хорошим» один раз пропустить пылесос через установленную линию, но только не среди добросовестных профессионалов в области вентиляции и кондиционирования.
А если компания заявляет, что они продувают трубопровод азотом и уменьшают размер загрязняющих веществ до 300 микрон, это еще лучше! Безусловно, не все компании делают все возможное.