Кондуктор для холодной ковки своими руками: Улитка для холодной ковки своими руками: инструкция
Улитка для холодной ковки своими руками: инструкция
Изготовить красивый забор из металлического прута по силам любому владельцу небольшой мастерской. Основными декоративными элементами, создающими рисунок полотна, являются улитки для холодной ковки, которые можно создать своими руками. Спирали различных размеров выкладываются в рисунок, прихватываются сваркой. Получаются сказочно красивые кружева из грубого металла.
Холодная ковка выполняется на различных приспособлениях, простых по своей конструкции. Купить кондуктора сложно, проще сделать самостоятельно. Улитки изготавливаются различными способами. Каждый мастер чертит свой образец. Оптимальным является форма золотого сечения.
Улитки для холодной ковкиВиды устройство и принцип работы улитки
Спираль, полученная прутком после гибки, полностью зависит от формы и размеров кондуктора для художественной ковки. Если он неразборный, то для каждого узора нужно делать отдельный инструмент. Бывают разные виды кондукторов для художественной холодной деформации тонкого проката: от приспособлений ручной гибки, до модернизированных трубогибов. Без промышленного оборудования сделать своими руками можно только следующие виды улиток для холодной ковки:
- монолитную;
- съемную;
- разборную.
Устройство и принцип действия самодельных улиток довольно просты. Сначала конец прутка зажимается в центре спирали, а затем прокат гнут по наружной поверхности кондуктора. На простейшем оборудовании мастер с прутом ходит вокруг улитки, вручную и с помощью рычага, укладывая его в кондуктор. При использовании подвижного приспособления, используется рычаг для вращения.
Кондуктор можно располагать горизонтально и сделать приспособление со штурвалом, когда штамп будет вращаться вертикально. Холодная ковка с ручной гибкой возможна на малых сечениях прутка (до 12 мм).
Технические характеристики конструкции
Размеры улитки для холодной деформации определяются диаметром изгибаемого проката и требуемым размером завитка. Предварительно делается эскиз рисунка кованого изделия. Разбивается на отдельные элементы. Под каждую спираль изготавливается кондуктор — улитка или любой другой.
Простейшие станки для холодной ковки имеют массивную, прочную стойку, на верхнем торце которой находится паз для фиксации пластины с кондуктором. Деформация осуществляется за счет усилия рук мастера. Он зажимает конец прутка и ходит вокруг приспособления.
При наличии поворотного стола и рычага, возможно изготовление улиток для проката большего сечения.
Изготовление простой улитки своими руками
Станок улитка обычно имеет сменные кондукторы разного размера. Сначала чертится шаблон инструмента для холодной ковки. Затем по нему изготавливается улитка — кондуктор, точнее открытый штамп для навивки. Вырезается улитка нужной формы и крепится к основанию.
Наиболее эстетично выглядят спирали, изготовленные по принципу золотого сечения. Для этого надо нарисовать квадрат, со стороной равной размеру сечения прутка, для которого готовится кондуктор. Затем циркуль поочередно ставят к каждой вершине квадрата и по часовой стрелке проводят линию.
Линия должна заканчиваться возле луча, на котором стоит ножка циркуля.
Как своими руками сделать улитку для холодной ковки
Сначала следует выбрать модель инструмента, затем начертить эскиз конструкции и создать шаблон будущей спирали. Исходить надо из количества деталей, которые планируется делать, их типоразмеров. Для изготовления забора вокруг собственного дома, можно использовать неразборной инструмент.
Монолитная неразборная улитка
Неразборной кондуктор можно за два часа изготовить в условиях гаража при наличии сварочного аппарата:
- На листе бумаги делается эскиз будущей улитки в натуральный размер.
- Из листа металла толщиной 4–5 мм вырезается полоса шириной 40 мм.
- Полоса сгибается на трубогибе, постоянно подгоняясь под шаблон. Можно использовать самодельный станок с пальцем и ограничителем движения листа на раскручивание.
- Срезать на конус полосу от первого вика до конца. Минимальный размер остается 20 мм.
- Приварить плоским торцом полученную спираль к металлической пластине размером примерно 10×200×200.
После остывания самодельный штамп готов к работе.
Съемная конструкция
Съемный кондуктор изготавливается из листа толщиной минимум 10 мм. В идеале, если спираль будет вырезана на станке с ЧПУ, но можно изготовить самостоятельно. На лист наносят контуры будущей детали и вырезают болгаркой. При наличии фрезера, делается шаблон, и обработка производится с применением копировальной втулки.
Для крепления к основанию в изготовленной спирали подмечаются и сверлятся отверстия под болты. Инструмент быстро сменяется и можно делать различные спирали с минимальной затратой времени на смену материала.
Разборные улитки с вращением
Кондуктор сложной формы считается наиболее сложным в самостоятельном изготовлении. Позволяет делать на одном штампе спирали с различным количеством витков.
Разборная поворотная улитка представляет собой съемную модель, изготовленную из нескольких сегментов. Сначала можно изготовить из листа большую, многовитковую спираль. Затем разрезать ее на несколько сегментов. Рез должен быть очень тонким и проходить под углом. В каждом сегмента делается 2 отверстия и в них вставляются штыри. Для точной сборки кондуктора, их надо делать методом подметки по платине.
В процессе гибки прутка сегменты добавляются до нужного размера завитка. Разборные улитки, сделанные по формуле золотого сечения, универсальны.
Улитка для холодной ковки своими руками с фото и видео
Мы расскажем про принцип работы улитки для ковки, ее преимущества и разновидности, простейшие чертежи и технологию самостоятельного монтажа.
Элементы в виде завитков, выполненные из прутков, широко применяются в дизайне придомовых территорий и интерьере жилых помещений. Для их изготовления используется специальные приспособления. Одно из них — это улитка. Домашние мастера часто конструируют это устройство из подручных материалов сами. Если вы также хотите знать, как изготавливается улитка для холодной ковки своими руками, то эта статья для вас. Из нее вы узнаете принцип работы этого устройства, его преимущества и разновидности, простейшие чертежи и технологию самостоятельного монтажа.
Виды, устройство и принцип работы «Улитки»
Улитка для холодной ковки — это приспособление для создания узоров в виде завитков из металлических прутков путем их деформационного загиба по контуру шаблона. Деформация происходит за счет жесткой фиксации рабочего прутка к шаблону. Для этого нужно прикладывать силу. Обеспечивается это ручным усилием или электрическим приводом. При самостоятельном изготовлении устройства целесообразность применения электрического привода должен определить сам мастер. Он необходим в случае большого объема работ. В основном используется ручное усилие.
Улитка (кондуктор) может иметь разную конструкцию. Она может быть выполнена:
- в виде стабильно приваренного к рабочему основанию шаблона;
- в виде разборных съемных частей, которые крепятся на основание.
По-разному может быть организован и ручной привод.
В самой примитивной конструкции пруток наматывают на шаблон простым усилием рук или с использованием в качестве рычага любого подходящего приспособления.
Также рычаг может входить в конструкцию станка и крепиться к ножке станины и приводиться в движение с помощью подвижного подшипника, перемещающегося по основанию улитки.
В более сложных устройствах вращается сам кондуктор, который крепится на ось вала. Она приводится в движение с помощью трех рычагов.
Вы должны заранее определить конструкцию станка, исходя из целесообразности и удобства использования.
Монолитный кондуктор имеет определенную форму шаблона, которая служит единственным вариантом завитка. Это является недостатком такой конструкции, но зато ее сделать самим совсем несложно.
Съемный вид конструкции удобен тем, что на таком станке можно изготавливать фигурные завитки разных размеров и форм. Но конструирование самого станка более сложное. Кроме того, у съемного устройства надежность фиксации частей шаблона хуже, чем у монолитного вида. Вам потребуется постоянное подкручивание резьбовых соединений, т. к. они при работе могут ослабеть.
Изготовление простой улитки своими руками
Если вы остановились на упрощенной монолитной конструкции, то знаете, что в этом устройстве применяют простое наматывание прутка усилием рук или с помощью рычага на жестко приваренную к рабочей поверхности форму. Такой станок можно использовать для создания завитков на прутках небольшого сечения (менее 12 мм).
Монолитная неразборная улитка
- Сначала вырисовывается схема на листе бумаги будущего шаблона с нужными размерами (иногда схема шаблона наносится непосредственно на основание кондуктора). К этому нужно подойти ответственно, т. к. после приваривания готовой формы исправить ошибки не получится. Толщина очертаний формы на чертеже должна быть такой же, как толщина используемой для ее изготовления металлической полосы. Минимально она должна составлять 3мм. Витки нужно размещать на расстоянии 12–13 мм друг от друга, чтобы между ними в паз умещался деформируемый пруток в 10 мм.
- Из стального листа толщиной не менее 4 мм вырезается основание улитки (лучше круглое), размер диаметра которого определяется соразмерно величине шаблонной спирали и быть больше размера улитки. Обычно диаметр основания бывает в пределах 70 см.
- В соответствии с чертежом из металлической полосы толщиной 3мм изготавливается нужная форма завитка. Для этого заготовку лучше прокалить, чтобы она легче поддавалась механической обработке. После изготовления формы лишний конец полосы отрезается, а кромки улитки подрезаются на конус и зачищаются.
- Готовая форма приваривается к основанию, которое крепится на станине. Иногда шаблон, приваренный к основанию, фиксируют на станине с помощью тисов, установленных на ней. Для этого к обратной стороне основания формы приваривают отрезок бруса для захвата тисами.
При варианте фиксации кондуктора в струбцине тисов можно легко менять шаблоны и получать различные формы завитков, если изготовить несколько видов, монолитно приваренных к основанию устройств.
- На рабочем основании сначала прорисовывают контур улитки с отметкой вдоль контура мест нанесения отверстий для крепления шаблона.
По эскизу из стальной толстой полосы изготавливается шаблон и в нем просверливаются отверстия. Он крепится к основанию на болты.
Ковку витой формы нужно начинать от центрального завитка. Конец заготовки вставляется в паз первого завитка формы и плотно к нему прижимается. Для надежности фиксации можно использовать небольшой зажимной инструмент. С усилием свободная часть прутка накручивается на шаблонную форму с помощью приспособления — рычага. Для усовершенствованных конструкций используется рычаг, приводимый в движение с помощью подвижного подшипника, закрепленного на нем. Рычаг изготавливают из прутка диаметром 20 мм.
Посмотреть изготовление такого устройства можно в видеоролике:
Разборные улитки с вращением
Шаблон улитки может состоять из нескольких частей, а деформация прутка происходить путем вращения кондуктора. Такой станок состоит из следующих элементов:
- толстого металлического основания в виде диска или квадрата;
- разборного шаблона, закрепленного на площадке основания;
- вала вращения;
- рычага для привода вала в движение.
Рабочее основание изготавливается из металла, толщиной от 4 до 10 мм.
Сборный шаблон может состоять из нескольких частей, которые соединяются между собой шарнирными штифтами, вставленными в отверстия проушин, приваренных к концам элементов. Вместе они составляют контур улитки.
Для крепления такой улитки к рабочему основанию в нем нужно просверлить отверстия для ее фиксации к поверхности в определенном положении. Меняя положение сборных частей на основании, можно получать разную кривизну завитков и их форму. Величина дуги формы регулируется специальными винтами, закрепленными на соединительные шарниры.
Составную улитку на шарнирных соединениях самостоятельно изготовить довольно сложно. Обычно, мастера приобретают изготовленный в промышленных условиях штамп и крепят его на станину.
Самим можно изготовить более простое устройство разборного шаблона без использования шарниров. Для этого нужно сделать эскиз сборных частей улитки с местами отверстий. Если подготовить несколько эскизов и, в соответствии с их контурами, просверлить отверстия в основании в разных местах, то можно крепить шаблоны с разными радиусами на одном основании.
Например, можно выполнить такой вариант:
Устройство со съемными частями улитки и вращающимся цилиндрическим валом, приводимым в движение с помощью рычага, показано в видеоролике:
Чертежи улитки для ковки
Начинающие мастера часто обходятся без чертежа, нанося контуры улитки на само основание без всяких расчетов. Для первого раза это допустимо, но, если вы хотите сделать качественный станок улитку для холодной ковки, то нужно, все-таки, пользоваться чертежами, в которых рассчитаны все параметры.

На схеме также описан принцип работы такого станка, в котором использован привод с помощью трех рычагов, вращающих вал и улитку.
Изгиб осуществляется после жесткого закрепления конца заготовки за первый завиток шаблонной формы с помощью фиксатора и последующего наматывания прутка вокруг вращающегося спиралевидного шаблона при вращении вала.
Познакомившись с устройством разных видов «Улитки» и особенностями их применения, а также посмотрев видео с примерами самостоятельного изготовления этого приспособления, вы можете приступать к созданию выбранной вами конструкции станка. А если у вас есть опыт в изготовлении таких устройств, то вы можете поделиться им в комментариях к этой статье и дать советы начинающим мастерам.
Как самому сделать качественный кондуктор для ковки? — moyakovka.
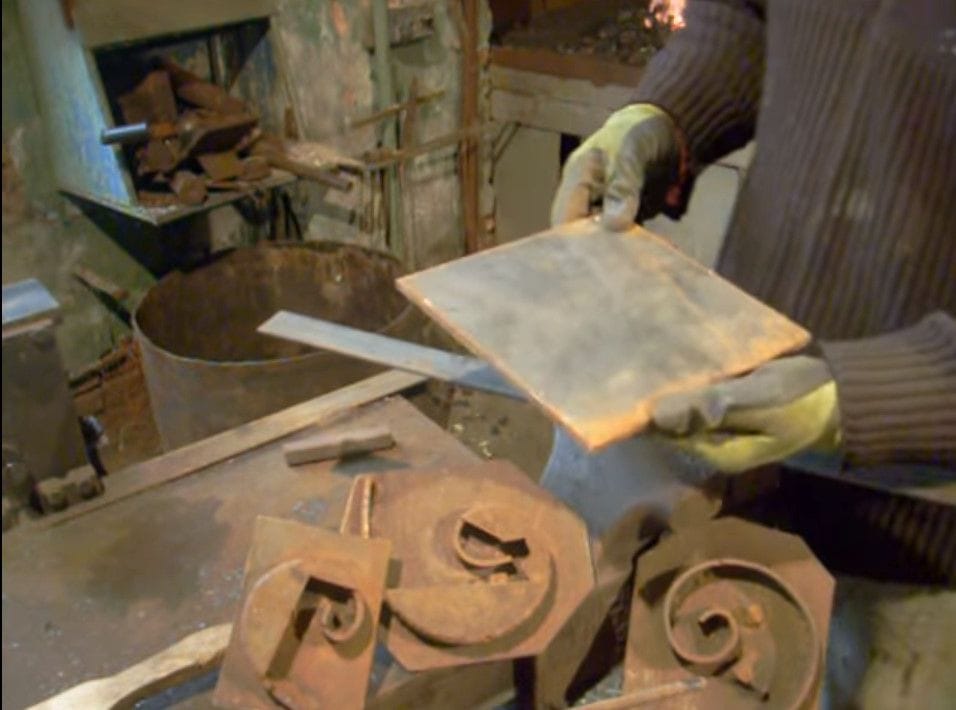
Кованые элементы пользуются спросом у клиентов различных категорий. Детали обладают разнообразием видов, реализуются по низким ценам, позволяют украшать различные изделия и создавать интересные композиции, легко крепятся к предметам посредством сварки, просты в уходе, отличаются долговечностью и привлекательным дизайном.
Востребованной категорией кованых элементов являются завитки различных конфигураций. Они прекрасно дополняют дизайн небольших изделий для интерьеров и массивных конструкций для внешнего облика зданий.
Производители предлагают обширный ассортимент спиралевидных элементов. Существует альтернатива – приобретение или изготовление оборудования, что позволяет создавать своими руками завитки разнообразных видов и размеров.
На чем осуществляют гибку, весь перечень оборудования: универсальные, ручные, матрица и прочие
Для изготовления завитков по горячей и холодной технологиях применяется различное оборудование.
Механизированные станки
Специальные станки с электрическим приводом и ручным управлением. На практике данные механизмы представляют собой гибочное оснащение, позволяющее обрабатывать заготовки из прутков, полос и профильных труб разного сечения. Встречаются как универсальные станки, предназначенные для изготовления разных элементов из металла, так и специальные, подходящие только для производства завитков.
Станок для ковки Ажур-1М. Фото КовкаПРО
Ручные инструменты, штампы, оправки
Инструмент с ручным управлением типа улитка популярен и представляет собой круглый стол, имеющий центральную ножку. Также в строение машины входит двойной рычаг, верхняя часть которого рабочая, а нижняя служит для опоры, кондуктор или оправка, располагающиеся на столе и служащие для гибки. Нередко улитки именуют матрицами, кондукторами и станками для холодной ковки.
Станок для холодной ковки типа Улитка Stalex SBG-30. Фото КовкаПРО
У исполнителей пользуются популярностью и другие устройства для холодной ковки: волна, твистер, глобус, фонарик, гидравлический пресс. Ручные устройства используются для холодной ковки в домашних условиях, т.е. в тех случаях, когда исполнителю не важны скорость изготовления и количество полученных элементов. Для увеличения производительности станки дополняются электрическим приводом или двигателем.
Кроме этого, для холодной ковки используются различные дополнительные приспособления: вилки, клещи и т.д. Мастера нередко собирают нестандартные модели инструментов и самодельные приспособления, которые имеют неофициальные названия.
В свою очередь для горячей ковки исполнителю потребуется меньший набор инструментов, основными являются молот и наковальня, но больший уровень знаний и навыков.
Однорогая консольная наковальня. Фото Станкоцентр
Основополагающие особенности
Есть несколько вариантов, как самому сделать кондуктор для ковки, при этом каждый из них имеет свои плюсы и минусы. Чаще всего используются стационарные платформы, где надо прилагать много сил, но делаются они проще других. На втором месте по сложности находится механическая наборная система. Самый сложный вариант — это кондуктора с электрическим приводом.
Наковальня: а – рог; б – хвостовик; в – лицо; г – углубление для пробивания отверстий; д – отверстие для установки подкладного инструмента; е – площадка для рубки металла; ж – башмак.
Вся система выстраивается по спирали, но в зависимости от ситуации используются 2 системы — Архимедова спираль и Фибоначчи. Выбор зависит исключительно от желаемого результата (чаще используется вариант с Архимедовой спиралью).
В первом случае спираль имеет постоянную ширину, несмотря на размах витка. При изготовлении кондуктора удержать постоянство очень не просто, но игра стоит свеч. Практических минусов у такого подхода нет, но не все хотят видеть у себя популярную конструкцию.
В случае со спиралью Фибоначчи идет стабильное увеличение. На такую спираль уходит меньше материала, но и выглядит она более жидкой, из-за чего используется не часто. Ее необычный внешний вид в первую очередь интересует любителей чего-то необычного, а таких в 21 веке очень много. Плюсов у системы очень много, но есть и минус — отсутствие надежности, так как спираль редко насчитывает более одного полного витка.
Существует два варианта кондукторов — для правшей и левшей. В результате разницы не будет, но напрямую от этого зависит удобство для мастера. В данном случае, чтобы определить, какой рукой работать удобнее, нужно попробовать оба варианта.
Изготовление платформы
Кувалда и молотки: а – кувалда; б – боевые молоты; в – ручник; г – фасонные молотки.
Данный способ самый простой, но для его использования потребуется дополнительная поверхность (стол, тиски или наковальня), на которой можно будет зафиксировать (утопить) конструкцию.
Вся работа проходит поэтапно, каждый из которых обязателен для выполнения:
- Отрезается 2 стальные пластины 10*10 см и 15*15 см. Чем толще будет листовая сталь, тем лучше, но не менее 3 мм. Такая необходимость вызвана дальнейшим регулярным воздействием грубой физической силы.
- Делаются отрезы от стальной полосы аналогичной толщины (можно немного уменьшить, т.
к. не в каждом городе можно найти плотную полосу). Длина отрезов зависит от предполагаемого размера витка, а также от диаметра прута, на который идет расчет (оптимально 10 мм). Когда приходит опыт, то такие отрезы делаются уже на глаз, но в самом начале придется использовать бумагу-миллиметровку.
- Поверх полученного рисунка плоскогубцами выгибается полоса. В итоге должны получиться 3 отреза на 1, 2 и 3 витка. Их нельзя будет между собой соединить, но в работе такой порядок позволит очень быстро решать любую поставленную задачу.
- Делаются 3 отрезка профилированной трубы по 5-8 см. Чем толще будут стенки, тем лучше. Иногда мастера совмещают две профилированные трубы и взаимно фиксируют их сваркой. Чем больше длина у «ножек», тем больше шансов на слом, поэтому не стоит лишний раз их удлинять.
- Все элементы свариваются воедино. Сначала приваривается улитка (внимательно надо смотреть за ее расположением, чтобы работать было удобно), затем ножка. В обратном порядке будет неудобно.
- Отрезается пруток и фиксируется на самой короткой спирали таким образом, чтобы при вхождении рабочего прута в спираль пруток выполнял роль фиксатора.
В итоге получается 3 формы разной длины. Благодаря такой конструкции можно за считанные минуты загибать прут диаметром до 10 мм до 3 оборотов, но для этого потребуется некоторое приложение физической силы. Очень важно обратить внимание на сварной шов, чтобы он покрывал максимальную длину стыка, иначе изделие может получиться недолговечным.
Механическая наборная система
Виды зубил: а – для поперечной рубки холодного металла; б – для поперечной рубки горячего металла; в – для продольной рубки; г – для рубки по радиусу; д – для фасонной рубки.
Тут сложность заключается не в изготовлении платформы, а в двигательной системе. Площадка может быть выполнена способом, описанным выше, но ее можно исполнить и более сложным способом, который повысит уровень комфорта при работе:
- Вырезается из листовой стали пластина 15-15 см.
- На миллиметровой бумаге делается рисунок спирали на нужное количество витков.
- Из стальной полосы делается отрез нужной длины, после чего сворачивается плоскогубцами в спираль, чтобы полностью совпадал по своим габаритам с рисунком.
- Спираль прикладывается к пластине и полностью переводится на нее. Нужно это для того, чтобы потом можно было проще сориентироваться.
- При помощи ножовки по металлу спираль разрезается на нужное количество элементов, каждый из которых равен 1 витку.
- С шагом в 4 см к каждому элементу привариваются ножки из стального прутка. На том же месте, где ножки у прутка, в пластине располагаются отверстия.
Основание из трубы делается таким образом, как и ранее. Этот же аспект касается прутка-фиксатора в спирали. Единственная разница в изготовлении платформ — это то, что сваркой фиксируется лишь самая маленькая спираль, а остальные устанавливаются наборным образом.
Более сложная часть — это ручная система, которая приводит механизм в движение. Для удобства можно использовать механизм с четным количеством шестеренок по типу часового. Если нет желания долго выстраивать систему, то можно воспользоваться принципом велосипеда — 2 шестерни и кожух, причем нужно сработать систему на понижение оборотов, что в значительной мере позволит уменьшить прилагаемые усилия.
На выходе устанавливается дополнительный вращающийся элемент, который будет служить формой для трубы. А в движение механизм приводится вращающейся ручкой (самый удобный вариант — от советской мясорубки).
Система с электрическим приводом
Клещи: а – для круглого металла; б – для квадратного сечения; в – для полосового металла.
Платформа в данном случае чаще всего наборная, т.к. делать сложный механизм и примитивную рабочую площадку по меньшей мере нелогично. Сама же система изготавливается следующим образом:
- Потребуется сильный электродвигатель. Обычно подобные двигатели используются на УБДН, стационарных циркулярных пилах и т.п. электротехнических приспособлениях, требующих немалых мощностей.
- К двигателю крепится понижающий инвертор, который понижает обороты, но повышает мощность вращения.
Вывод на платформу осуществляется ровно таким же образом, как и с ручным приводом. А вот включаться будет при помощи обыкновенного тумблера. Особо придумывать что-то не придется, т.к. система на практике довольно простая. Единственное осложнение — это обязательное наличие места электропитания, т.к. руками механизм в движение не приводится.
У данного станка есть еще одна особенность — нужен дополнительный пруток, устанавливаемый на дистанции 20 см от рабочей поверхности. Этот пруток будет служить упором для загибаемой заготовки, чтобы лишний раз не отвлекаться. Его можно организовать и для ручного механизма.
Обычно такие приспособления идут в качестве основных в организациях, занимающихся гнуто-кованными изделиями. Несмотря на достаточно простое описание работы системы, на практике ее изготовить гораздо сложнее, чем любую другую.
Читать также: Как соединить провода точечных светильников
Принцип работы улитки для накрутки кованых завитков, бубликов и спиралей
Для выполнения гибки завитков необходимо подготовить заготовки нужных размеров, в зависимости от технологии обработки детали следует нагреть или сразу же приступать к работе.
Создание завитка для балясины на кондукторе
Заготовка помещается в кондуктор, окончание фиксируется в специальной пазухе, прутку придается соответствующая форма посредством приложения усилий.
На нижеследующем видео это показано наглядно.
Как сделать своими руками станок с лекалом для холодной и художественной ковки
Сделать своими руками кондуктор для завитков достаточно просто. Для этого потребуется полоса, кусок листового металла, угольник и два малых элемента прямоугольной формы, один из которых имеет выемку для закрепления окончания заготовки.
Данные детали свариваются под прямым углом и присоединяются к полосе, которая уже имеет форму спирали. Полоса крепится к листу металла небольшого размера, с нижней стороны приваривается угольник, обеспечивающий фиксация в тисках или ножка для размещения на наковальне.
Как нарисовать спираль, можно посмотреть в следующем видео.
Кроме этого, при наличии знаний о строении и принципе работы устройств возможно изготовить своими руками и другие устройства: фонарик, улитка, волна и т. д.
Сборка устройства
Такой вариант станка используется для примера по причине его простоты. Зная основные принципы и последовательность конструирования оборудования, его можно модернизировать по своему желанию. Чтобы собрать все части оборудования в единое целое, необходимо будет воспользоваться:
- дрелью с твердосплавным типом сверл;
- аппаратом для сварки;
- пилой, разрезающей металл, либо ножовкой;
- металлическим полотном выбранного размера;
- круглой трубой из металла;
- прутом металлическим;
- разной величины подшипниками;
- болтами размером м8.
Чтобы собрать станок для холодной ковки своими руками необходимо воспользоваться проверенной последовательностью действий:
- Изначально необходимо собрать стойку, которая будет служить опорой. Для этого все ее составляющие (отрезы трубы одинакового размера и сочленения между ними с верхнего и нижнего краев) необходимо соединить в единое целое. Конструкция по внешнему виду может напомнить табуретку.
Соединение проводить при помощи аппарата для сварки, а нарезаются отрезки пилой.
- Следующим шагом является нарезка листов из металла. Должны получиться круги равных диаметров и четыре треугольника, имеющих равные стороны. Элементы треугольной формы необходимо приварить на низ соединенной конструкции труб таким образом, чтобы подучилось нечто подобное пирамиде. Основание, которое имеет более широкую площадь необходимо приварить в центральной точке вырезанной окружности.
- Четыре планки, которые расположены горизонтально необходимо присоединить к кругу с уже приваренным элементом. Произвести это следует, используя болты, для этого понадобится дрель, чтобы проделать отверстия.
- Следующий шаг – сооружение рукояти. Чтобы это сделать нужно воспользоваться двумя прутьями различной длины. Определить их размеры можно, соотнеся их с диаметром круга. Один прут должен быть соизмерим с диаметром, другой немного превышать его размер. Сгибая первый прут, следует соблюдать угол в 30 градусов при этом.
Оба прута после этого приварить друг к другу, после чего в нижнюю часть вварить еще один прут. Также должна быть перемычка между первыми двумя отрезками, к которой присоединяется сваркой рычаг, который должен сохранять направление в сторону сооружения из прутьев.
Читать также: Шлифмашинка по бетону цена
Подшипник для будущей вариабельности направлений в устройстве необходимо прикрепить к концу присоединенного рычага, а также к отрезку, находящемуся внизу конструкции. Верхний отрез служит креплением для катушки из металла, устанавливать которую необходимо горизонтально – она дает возможность загибать металл. С нижней стороны отрезка, где имеется свободный конец, следует проделать отверстие, равное по диаметру размеру сечения трубы.
- Последнее действие в алгоритме действий при сооружении станка для холодной ковки своими руками будет соединение сконструированной рукояти с частью устройства похожей на «пирамиду». Фиксация этих элементов после одевания рукояти производится гайкой широкого диаметра, к которой предварительно необходимо приварить металлический круг, который позволит крепить сам шаблон для станка.
Далее «улитка»-шаблон присоединяется сваркой.
Кто решил всерьез заняться ковкой и сделать станок для холодной ковки своими руками, следует быть очень скрупулезными на этапе создания чертежей и расчетов. В остальном процесс создания достаточно прост, а разобравшись в принципе конструкции оборудования, можно придумывать ему различного рода вариации, которые помогут совершенствовать изделия.
Один из способов украшения участков — использовать кованные изделия. Очень декоративно смотрятся заборы, скамейки, беседки, перила для лестницы и другие подобные сооружения. Причем в большинстве случаев данные изделия не есть ковка в ее традиционном понимании. Чаще всего это сделано не в кузне и не при помощи молотка и наковальни, а при помощи некоторых устройств, которые позволяют создавать из металлических полос и квадратных прутков самые различные узоры и изделия. Для изготовления подобных изделий потребуются станки для холодной ковки. Часть из них можно сделать своими руками другую проще купить.
Приспособления для изготовления мебели своими руками
Особенности применения в мебельной промышленности
Кондукторы и шаблоны нужны при сборке мебели. Благодаря таким вещам вы не допустите распространенной проблемы, возникающей во время сверления — попадания сверла в деталь под неправильным углом. Исправлять такую ошибку придется крайне долго, в некоторых случаях это будет даже невозможно.
А кондуктор для проделывания отверстий позволит не только правильно сориентировать рабочий инструмент, но еще не даст ему сбиться с нужной траектории.
В мебельной промышленности кондукторы и шаблоны используются в следующих случаях:
- на серийном производстве;
- при сборке конструкций, когда в соединяемых частях нужно сделать отверстия под крепежные элементы. В этом случае подойдет кондуктор для сверления отверстий под шканты или конфирмат;
- кондуктор для сверления отверстий под углом используется как в таких случаях, так и во время работы с тонкими плитами, например, с МДФ или ДСП.
Во время применения такого приспособления процесс сборки будет происходить намного проще и быстрее, нужные отверстия вы сможете проделать независимо от того, как далеко они должны располагаться от края детали и того, какую она имеет ширину.
При самостоятельной сборке мебели часто приходится соединять детали встык посредством шкантов. Отверстия под шканты лучше всего проделывать посредством специального кондуктора. Особенность шкантов состоит в том, что несмотря на то, что такие крепежные элементы хоть и устаревшие, но все равно актуальны при производстве мебели.
Сложность в их применении заключается в том, что оси отверстий, которые проделываются в деталях при соединении, должны иметь друг с другом прямой угол. Соответственно, они должны размещаться строго перпендикулярно по отношению друг к другу. Выполнять это без специального устройства сложно. Поэтому если хотите достичь высокого качества исполнения, рекомендуется купить кондуктор для шкантов.
Станок улитка для холодной ковки своими руками
Используя кондуктор, вы сможете самостоятельно изготавливать гнутые элементы нужного размера, которые отлично подойдут для оформления готовых уличных металлоконструкций.
Для создания спиралевидных завитков можно использовать разные материалы, но чаще всего используются металлические квадратные или круглые прутки.
Главная особенность самодельного станка «улитки» заключается в том, что декоративные элементы изготавливаются «на холодную» — без предварительной температурной обработки. Это снижает трудоемкость работ.
Cоветуем: Кондуктор для изготовления кругов из наждачки для УШМ
Прежде чем перейти к главному вопросу — пошаговой инструкции, как сделать улитку для холодной ковки, важно понять, какой именно станок вам необходим. Они бывают разных конфигураций.
Станок «улитка» может быть «заточен» под конкретный размер завитков — на нем можно сгибать декоративные элементы определенной длины.
Также домашние умельцы используют универсальные сборные конструкции — они предназначены для изготовления как небольших, так и крупноразмерных завитков.
В условиях мастерской обычно используются станки с ручным приводом. Однако если необходимо сделать большое количество заготовок, имеет смысл подумать над использованием электропривода.
Размеры будущего станка
Прежде чем приступить к изготовлению самодельного кондуктора для изготовления декоративных завитков, необходимо сначала определиться с размерами основных деталей.
В частности, нас интересуют габариты центральной части и завитка. Исходя из фактических размеров шаблона, определяют размеры других элементов конструкции — например, станины, на которой будет крепиться гибочный кондуктор.
Для создания станка улитка для холодной ковки своими руками чертежи и размеры при необходимости можно подобрать на тематических сайтах (или поищите подходящие варианты на форумах по данной тематике).
Причем существует много разных вариантов самодельной конструкции. Давайте рассмотрим один из них.
Для изготовления чертежа нам потребуются:
- стальной квадратный пруток 10х10 мм;
- лист бумаги формата А4;
- угольник;
- карандаш и циркуль.
Первым делом укладываем квадратный пруток посередине листа бумаги, и чертим две параллельных линии.
Затем прикладываем пруток в перпендикулярной плоскости под углом 90 градусов (используем для этого угольник), и чертим еще две линии.
В результате по центру шаблона улитки у нас должен получиться квадрат размеров 10х10 мм, от которого в разные стороны отходят четыре линии.
Берем циркуль, устанавливаем его в угол квадрата, и чертим полуокружность.
Потом смещаем циркуль в другой угол (идем по порядку), и также чертим полуокружность, продолжая предыдущую линию.
И делаем так до тех пор, пока не получится завиток требуемого размера — основная часть чертежа улитки.
После этого с помощью циркуля чертим окружность (в данном случае диаметр окружности составляет 43 мм).
Cоветуем: Буржуйка из газового баллона (с возможностью загрузки длинных дров)
Чертеж готов. Теперь необходимо подобрать стальную болванку подходящего диаметра и отрезаем от нее кусок длиной около 30 см. Из этой заготовки вырезается начало завитка (центр).
Нарисовать чертеж самостоятельно или скачать его из интернета и распечатать на принтере — это уже на ваше усмотрение.
Есть еще и другой способ, как сделать центральную часть — о нем мы подробно расскажем ниже.
Изготовление центральной части кондуктора
Оборудование и инструменты, которые потребуются для работы:
- сверлильный станок или дрель;
- болгарка.
Из листового металла толщиной 18-20 мм вырезаем один большой круг (это будет опорная пластина) и четыре маленьких круга — для изготовления центра кондуктора.
Сделанный центр крепится к станине при помощи крепежных болтов (автор использует болты под шестигранник) — для этого в заготовках сверлим соосные отверстия.
Далее расчерчиваем профиль, который нужно будет вырезать с помощью болгарки. Обрабатываем заготовку лепестковым кругом.
На следующем этапе подробно разберем, как сделать улитку. Можно использовать в качестве исходного материала квадрат или полосу. Если нет полосы, ее можно вырезать из листового металла подходящей толщины.
Изготовление заготовки кондуктора
Приступаем к следующему этапу работ — занимаемся изготовлением устройства для ковки металла, по которому будет гнуться заготовка. За основу возьмем квадратный пруток.
На гибочном станке сгибаем два одинаковых по длине завитка. Скрепляем их вместе с помощью малярного скотча, размечаем с помощью кернера места будущих отверстий.
Сверлим отверстия и нарезаем резьбу под крепежные болты. Готовый контур улитки будет крепиться болтами к металлической опорной пластине (станине).
Когда основные детали готовы, можно приступать к заключительной части работ — сборке станка холодной ковки своими руками.
Для этого потребуется еще изготовить станину, и продумать, из каких материалов сделать основание и как оно будет крепиться к рабочему верстаку или другой опорной поверхности (например, горизонтальной площадке, расположенной на стойке).
Окончательная сборка станка
Изготавливаем станину станка. Для этого нам потребуются два отрезка металлического уголка и пластина металла, которая будет устанавливаться вертикально.
Cоветуем: Ленточный шлифовальный мини станок с регулируемым столом
Верхние края пластины необходимо будет закруглить. В подготовленных деталях сверлим отверстия, после чего соединяем их вместе с помощью болтов.
В металлической пластине сверлим отверстие под вал, в роли которого используется стальной кругляк.
Дополнительно необходимо просверлить крепежные отверстия — для крепления корпусных подшипников. Далее с двух сторон пластины прикручиваем на болты подшипники, устанавливаем вал.
Как видите, в том, чтобы сделать улитку для холодной ковки своими руками, нет никаких сложностей.
Причем рассмотренный выше вариант кондуктора является разборным, что очень удобно — это существенно упрощает хранение приспособления, когда оно не используется.
К опорной пластине крепим центральную часть, потом прикручиваем на болты завитки из квадратного прутка.
К тыльной стороне опорной пластины крепим вал. Потом устанавливаем собранный кондуктор улитку для холодной ковки на вертикальную пластину (станину) станка.
Дополнительно сверлим в пластине отверстие и устанавливаем вал с опорными подшипниками.
На конце основного вала сверлим отверстие, в которое вставляем ручку, изготовленную из стального круглого прутка. Пошаговый процесс работ можно посмотреть на видео ниже.
Другие сферы использования
Кондукторы для отверстий используются не только при производстве мебели. Достаточно часто их применяют тогда, когда нужно проделать отверстие в трубе или другой детали цилиндрической формы. Благодаря им можно выполнить качественное отверстие даже в трубе с малым диаметром.
Читать также: Картофелекопалка своими руками размеры чертёж картинки
Такие устройства универсальны и просты в применении, поэтому их также используют в следующих отраслях:
- машиностроение — сверление отверстий в разнокалиберных заготовках на основе разных материалов;
- строительство — бурение отверстий в строительных конструкциях;
- домашние коммуникации — как уже говорилось, сверление труб и не только.
Современные сверлильные кондукторы могут быть разных размеров и иметь разный принцип работы. Некоторые их них устроены сложно, поэтому их проще купить. А некоторые модификации можно изготовить самостоятельно, тем более что некоторые серийные мебельные модели, особенно имеющие универсальное назначение, стоят дорого.
Шаблоны для изготовления мебели
Мебельный шаблон – это приспособление, которое ускоряет и облегчает процесс производства деревянных конструкций. Мебельщик совершает много однообразных действий, связанных с разметкой заготовок и сверлением отверстий. В зависимости от предназначения, шаблоны бывают двух видов.
Разметочные. Изготовить простое приспособление можно на основе столярного угольника, в котором сверлятся отверстия на необходимом расстоянии.
Разметочный шаблон для мебели
Сверловочные. Можно приобрести заводское приспособление или сделать самостоятельно. На металлической линейке делаются отверстия разметки мест сверления, которые располагаются друг от друга на определенном расстоянии. Перпендикулярно к поверхности инструмента крепится поперечина.
По такому принципу изготавливаются узкоспециализированные шаблоны для разных деталей мебельной фурнитуры.
Преимущества использования
По сути, такой кондуктор выступает в роли шаблона для проделывания отверстий, чтобы они были сделаны максимально точно. Их можно применять для тех отверстий, ось которых находится перпендикулярно поверхности рабочей заготовки, а также для работы под углом.
Данный инструмент — отличная альтернатива зарисовкам и ручным замерам. Сверло вы сможете разместить строго под нужным углом по отношению к заготовке и не допустите никакого отклонения. Результат будет особо заметным, если речь идет о проделывании глубоких отверстий.
Если вы применяете такое приспособление высокого качества для работы с ДСП, то оно должно иметь следующие характеристики:
- способствовать быстрой сборке мебели без необходимости применять сложные инструменты;
- давать возможность проделывать несколько отверстий одновременно без ручной разметки;
- заметно повышать качество работы со сверлом.
Кондукторы изготавливают на основе разных материалов, есть модели на основе пластика или органического стекла. Однако самым лучшим считается вариант из стали, имеющий такие преимущества, как:
- минимальная вероятность деформации;
- сверло направлено максимально четко;
- отсутствие нагрева при работе.
Очень часто в роли мебельных кондукторов применяют накладные модели на основе легких материалов, которыми легко манипулировать. Многие применяют заводские или самодельные инструменты.
А наиболее квалифицированные и опытные мастера уже не пользуются кондуктором, поскольку могут самостоятельно без труда проделать отверстие в конструкциях максимально точно. Но это под силу далеко не каждому.
Ключевое преимущество такого приспособления — это то, что работу может выполнить максимально точно и качественно даже тот человек, у которого нет должного опыта. Вам не придется выполнять разметки и сложные предварительные расчеты. Вы значительно сэкономите время и изготовите мебель намного быстрее.
Классификация инструментов
Перед тем как купить готовый кондуктор или же сделать его своими руками, нужно определиться, какие задачи вы будете решать с его помощью и только потом нужно подбирать подходящий вариант по конструкции и функциям.
Есть ряд категорий приспособлений, которые различаются по своему исполнению и функциональным особенностям. Вот некоторые из них:
- накладные — такие устройства накладываются на деталь, которая поддается обработке, затем ее на ней крепят или же просто фиксируют вручную. С их помощью проделываются отверстия в разных плоских деталях, плитах МДФ или в ДСП;
- поворотные — данные шаблоны применяются при обработке деталей цилиндрической формы. Они оснащены горизонтальной и вертикальной осями поворота, благодаря чему отверстия можно выполнять под разными углами;
- универсальные — такие устройства подойдут для малых серийных производителей мебели, где иногда требуется быстрая переналадка применяемого оборудования, они имеют все необходимые для этого функции;
- опрокидываемые — используются тогда, когда технологическая процедура проводится сразу в нескольких плоскостях;
- скользящие — такие кондукторы крепить не нужно. Просто приложите их к участку поверхности заготовки, где нужно сделать отверстие;
- закрепляемые — они более удобны в применении, но ограничивают свободу действий, что очень критично при работе со станками, где есть только один шпиндель.
Особенности конструкции и виды
Кондуктор, по сути, – это шаблон для сверления отверстий, позволяющий выполнить их максимально точно. Используют его и для создания отверстий, ось которых располагается перпендикулярно поверхности детали, и для сверления под углом.
Благодаря своей универсальности и простоте кондукторы для сверления отверстий активно применяются в различных сферах. В частности, в машиностроительной отрасли с их помощью уже давно и успешно выполняют сверление отверстий в заготовках различной конфигурации и изготовленных из разных материалов. Нельзя работать без кондуктора и в мебельном производстве, где такое приспособление активно используется при сборке мебели, установке на нее фурнитуры и выполнении целого ряда других технологических операций. Строительство – еще одна сфера, где кондукторы находят широкое применение. С их помощью, в частности, выполняют бурение отверстий в строительных конструкциях. Кондукторы также необходимы для сверления труб и решения других задач.
Даже простое приспособление в виде планки с упором намного облегчает и ускоряет процесс изготовления однотипных отверстий
В качестве мебельного кондуктора чаще всего применяются накладные модели, изготовленные из легких материалов, чтобы было удобнее ими манипулировать. Можно приобрести такие приспособления в заводском исполнении или изготовить мебельный кондуктор своими руками. Квалифицированные специалисты-мебельщики могут и не использовать кондуктор, чтобы качественно и точно просверлить отверстие в элементах мебельной конструкции, но для этого они должны обладать большим опытом работы в своей области.
Читать также: Шланг для кровельной горелки
Наиболее значимое преимущество кондуктора заключается в том, что с его помощью качественное и точное сверление как перпендикулярного к поверхности детали, так и наклонного отверстия может выполнить даже человек, не обладающий высокой квалификацией. Использование кондукторов исключает необходимость сложных предварительных расчетов и разметки мест расположения будущих отверстий, что снижает трудоемкость сборки мебельной конструкции и позволяет выполнить такую работу за более короткий промежуток времени. Даже начинающий специалист может разобраться в применении кондуктора для сверления под шканты и для решения других технологических задач.
Накладной кондуктор с револьверной головкой подходит для сверловки типовых отверстий под шканты любого размера
Прежде чем приобрести или изготовить свой самодельный кондуктор, определите, для решения каких задач необходимо его использовать, и на основе этих данных выберите его тип и конструктивное исполнение.
Среди кондукторов для сверления отверстий по типу конструкции и функциональным возможностям можно выделить целый ряд категорий.
Эти кондукторы называются так потому, что их накладывают на обрабатываемую деталь и закрепляют на ней либо просто фиксируют руками. Посредством кондукторов данного типа, в частности, выполняют сверление отверстий в ДСП, плитах МДФ и в других плоских деталях.
Такие шаблоны можно использовать для того, чтобы выполнять отверстия на деталях цилиндрической формы. Кондукторы данного типа оснащаются вертикальными и горизонтальными осями поворота, что дает возможность выполнять с их помощью отверстия под различными углами.
Это приспособления, которые особенно актуальны для маленьких серийных производств, где важна возможность быстрой переналадки используемого оборудования. Кондуктор данного типа как раз и наделен такими функциями.
Этот универсальный кондуктор предназначен для засверливания отверстий под минификс, конфирмат, рафикс и дверную петлю
Данные приспособления для сверления отверстий требуются в тех случаях, когда такую технологическую операцию приходится выполнять в нескольких плоскостях.
Скользящие и закрепляемые
Скользящий кондуктор в полном соответствии со своим названием не требует закрепления: его просто прикладывают к тому участку поверхности детали, где надо просверлить отверстие. Закрепляемые кондукторные устройства, хотя и являются более удобными, несколько ограничивают свободу действий специалиста, что особенно критично при выполнении сверлильных работ на станках, оснащенных только одним шпинделем.
Кондуктор для сверления отверстий своими руками
Как уже говорилось, в зависимости от сферы использования и конструкции, некоторые варианты можно сделать и самому, благодаря чему вы сэкономите существенную сумму.
Перед работой отыщите требуемый чертеж устройства и все изготавливайте строго по нему.
Необходимые для работы инструменты:
- сварочный аппарат;
- болгарка;
- дрель;
- слесарные принадлежности.
Чтобы своими руками сделать самый простой вариант кондуктора, выполняем такие действия:
- возьмите арматуру размером 10 на 10 мм с квадратным сечением;
- отрежьте кусок требуемой длины и зачистите его с помощью наждачной бумаги;
- сделайте разметку под шаблонные отверстия. При этом не допускается, чтобы центр приближался к краю более, чем на 8 мм, это почти половина толщины листа ДСП. Также согласно стандартам, между центрами должно соблюдаться расстояние в 32 мм;
- после выполнения разметки центров проделайте в них отверстия по 5 мм в диаметре;
- чтобы сделать упор, возьмите пластину из металла шириной в 2,5 мм и толщиной в 1 мм.
Согните ее под углом в 90 градусов, а потом, вместе с куском подготовленной арматуре и крепления в струбцине, сделайте место под резьбу;
- нарежьте резьбу и две детали соедините в одну конструкцию. Приспособление готово.
Как видим, подобное устройство очень простое в плане самостоятельного изготовления, но оно значительно упростит работу, если вы занимаетесь изготовлением мебели. Если вы занимаетесь этим исключительно как любитель, то этого варианта будет достаточно. Если сделать самому у вас не получится, купите готовый вариант, возможно, самый простой и недорогой.
А вот профессиональное оборудование будет стоить намного дороже, целесообразность его приобретения имеется уже тогда, когда речь идет как минимум о малом серийном производстве. Зато с его помощью вы сможете просто и быстро соединять предметы мебели или ремонтировать ее.
Итак, вы узнали, что такое кондуктор для проделывания отверстий и как он помогает при производстве мебели. Данное устройство можно как приобрести в готовом виде, так и сделать самому.
Читать также: Правильная установка цепи на бензопилу
Сверлильный кондуктор — непременный атрибут на крупном производстве, неважно на каком. Там, где много сверлят, он действительно необходим, особенно когда производство серийное или массовое.
С помощью кондуктора в значительной степени ускоряется производство, облегчается труд рабочего.
Самодельные кондукторные устройства
Кондукторы простейшей конструкции, например, те, которые используются для сверления отверстий под конфирмат, стоят относительно недорого, поэтому многие мастера не озадачиваются их самостоятельным изготовлением и приобретают серийные модели. Между тем есть и те, кто даже такие простые устройства старается сделать своими руками. Вопрос о том, как сделать кондуктор для сверления своими руками, часто появляется и при необходимости просверлить нестандартные отверстия.
Чтобы самостоятельно изготовить кондуктор для шкантов или более простой по конструкции кондуктор для конфирматов, можно воспользоваться чертежами и видео в интернете.
При изготовлении кондуктора потребуется идеально точное сверление направляющих отверстий и закалка готового приспособления
Для изготовления такого устройства, естественно, потребуется его чертеж. Нужен также минимальный набор инструментов и оборудования:
- электрическая или ручная дрель;
- набор слесарных инструментов;
- болгарка;
- сварочный аппарат (для изготовления кондукторных приспособлений более сложной конструкции).
Простейший самодельный кондуктор можно изготовить из подручных средств и материалов, которые в избытке имеются в большинстве домашних мастерских или гаражей. Использование таких материалов, к которым относятся куски металлической арматуры, деревянные бруски, металлические пластины и др., позволяет значительно сэкономить на приобретении серийной модели устройства.
Чертеж самодельного кондуктора для высверливания отверстий под конфирматы
Изготовление самодельного кондуктора для дрели или одношпиндельного станка проходит в несколько этапов.
- Квадратную арматуру сечением 10 на 10 мм, используя ножовку по металлу или болгарку, необходимо нарезать на отрезки требуемой длины.
- Центры отверстий, через которые будет выполняться сверление, должны находиться на расстоянии 8 мм от края кондукторной плиты. Именно на таком расстоянии расположен центр плиты ДСП или МДФ, в которой сверлят отверстие.
- Шаг между отверстиями на кондукторе в соответствии с общепринятыми мебельными стандартами составляет 32 мм, при этом диаметр таких отверстий должен быть равен 5 мм.
- Если оснастить самодельный кондуктор упором, то использовать такое приспособление будет значительно удобнее. Для создания такого упора нужна металлическая пластина толщиной 1 мм и шириной 25 мм, которую сгибают под прямым углом и фиксируют на уже готовом кондукторном приспособлении, изготовленном из арматуры.
- После того как конструктивные элементы самодельного кондуктора зафиксированы при помощи струбцины, их необходимо надежно соединить между собой, используя для этого резьбовые крепежные элементы.
Читать также: Углекислый газ образуется при
Готовый кондуктор с поворотными упорами
Чтобы минимизировать количество пыли, образующейся при использовании самодельного кондуктора, его конструкцию можно дополнить половинкой пластиковой бутылки. Такое простейшее приспособление может выступать и в качестве поддона, в котором будет собираться образующаяся в процессе сверления стружка.
Описанный выше метод позволяет изготовить простейший самодельный кондуктор, который значительно облегчает и ускоряет процесс сборки любой мебельной конструкции.
Главным крепежным элементом в сборке мебели является конфирмат. Ввинчивается он с подготовительным сверлением отверстия. Конкретно сверление сборочных отверстий в ДСП под конфирматы мы и разглядим в этой публикации.
Для сборки деталей ДСП нам пригодится:
- Шуруповерт
- Бита под конфирматы
- Конфирматное сверло
- Линейка иначе говоря рулетка
- Карандаш и шило
- Конфирматы
При сборке мебели обычно употребляют конфирмат размером 6,450. Т.к. поперечник резьбы 6,4 мм, а поперечник тела конфирмата 4,4 мм, то для высококачественного крепления деталей поперечник отверстия ожидается в рамках 4,5-5 мм и глубиной более 50 мм.
Если толщина отверстия будет не просто обозначенной – конфирмат будет плохо держать детали, если меньше – он собственной шириной может порвать ДСП.
Для выполнения сверлений употребляют конфирматное сверло, поперечником 4,5 мм, которое обустроено дополнительной головкой для выполнения сверлений увеличенного отверстия под шею конфирмата, которая так же делает зенковку под его шляпку.
Это, применяют и обыденное сверло поперечником 5 мм, но для высококачественного крепления в отверстии дополнительно делается место под шею конфирмата и его шляпку.
Чтоб совершенно скрепить две детали, нужно очень точно разметить места их креплений.
На детали, которая будет накладываться на торец (та, на занят будет сквозное отверстие), необходимо сделать два замера – в длину (обычно 5-10 см) и от края – ровно 8 мм (это если толщина плиты 16 мм).
На детали, которая ложится перпендикулярно, точку сверления отмечаем на торце. Тут необходимо выдержать такое же расстояние в длину (5-10 см от начала), а по ширине – строго по центру (8 мм от края).
Кондуктор для сверления отверстий
Сверлильный кондуктор, как правило, представляет собой планку (пластину) с отверстиями и втулками (гильзами). Посредством кондуктора значительно проще, например, сверлить трубы.
Что касается производства мебели, то здесь они тоже применяются, хотя и относительно недавно.
С помощью такой оснастки производитель избавлен от следующих проблем:
- Разметка.
- Кернение (точечные углубления в материале под сверло).
- Сверловка с соблюдением перпендикулярности.
Последнее особенно сложно выполнимо, поскольку требует серьёзных навыков, обретаемых только с годами.
Некоторые операции, например, сверловка под шканты (короткие деревянные стержни, предназначенные для скрытой стыковки деталей), требует очень точной разметки, и не менее точной сверловки под углом 90°.
С таким приспособлением, как кондуктор, эти задачи решаются легко и просто.
Кондуктор для перпендикулярного сверления отверстий
Простой мебельный кондуктор для сверления отверстий при сборке мебели из металла. Подробности в видео материале
Назначение — получение проходов в толстых заготовках, строго под углом 90°. Представляет собой набор втулок в едином корпусе, или кронштейн со сменными рабочими насадками. Установив приспособление над точкой сверления, можно начинать работу без предварительного накернивания. Сверло точно попадает в центр втулки и не отклоняется от оси.
Важно! Единственная проблема — инструмент необходимо удерживать на заготовке, особенно в начале работы. Иначе от вибрации он может сместиться.
Такой кондуктор для сверления можно сделать своими руками. Используется толстый текстолит или твердое дерево. Идеальный вариант — применение втулок от экструдера для протяжки проволоки. Изношенные втулки можно найти на заводе. Насадки для экструдера выполнены из легированной стали, с добавлением победита. Срок службы практически неисчерпаем.
Виды: выбираем нужный
Накладные. Они не нуждаются в фиксации перед их использованием по назначению. Конструктивно простые, мобильные, но их нужно держать свободной от дрели рукой, поскольку зачастую оснастка не закреплена в специальном устройстве, что не очень удобно. Учитывая простоту конструкции сделать его своими руками довольно просто. Применяется при сверлении ДСП и МДФ.
Кондукторы для сверления отверстий под углом. Конструкцию легко представить, поскольку название говорит само за себя. Такая оснастка может быть и накладной. В производстве качественной мебели присутствует и сверление под углом, что представляет не самую простую операцию в производственном процессе — для этого нужен навык. Хотя и в этом случае иногда нарушается нужный угол, сборка в результате не будет уже такой качественной и страдает внешний вид мебели, особенно если она не из ДСП, а из дерева — здесь уж некрасивую сверловку не зашпатлюешь. Оснастка же нужной конструкции полностью избавляет от ненужных проблем.
Поворотные кондукторы. В них имеются откидные кронштейны, и это позволяет произвести сверление на двух смежных плоскостях.
Скользящие редукторы. С их помощью без переустановок можно просверлить несколько отверстий. Для работы с такой оснасткой всё же требуются необходимые навыки.
Кондуктор отверстий под шканты
Приспособление предназначено для того, чтобы соблюсти соосность отверстий. Иначе вы не сможете установить шипы. Прикладывая кондуктор к обеим соединяемым деталям, вы обеспечите идеальную стыковку. Если вы решите сделать подобный кондуктор своими руками, искать чертежи не обязательно. Представляем два варианта прекрасно работающих самоделок:
Накладной шаблон
Изготовить его очень просто. Достаточно небольшого кусочка фанеры, и листа оргалита. С помощью такого приспособления вы всегда сможете просверлить пару соосных отверстий для шкантов. Оргалит (или другой прозрачный пластик) надо разметить, и насверлить калибровочных отверстий. С их помощью вам проще будет установить шаблон на нужное место. В отверстия надо забить тонкостенные латунные трубки. Иначе сверло по дереву быстро разрушит направляющие.
Важно! Такое приспособление подходит лишь для заготовок фиксированной ширины.
Тогда шипы будут расположены по центру торца. Для дерева других размеров, необходимо сделать отдельные направляющие, или универсальный шаблон кондуктор.
Самоцентрующийся кондуктор
Если вы не изготавливаете мебель с использованием стандартных панелей, нужен универсальный инструмент. Его также можно сделать своими руками, причем материалы буквально валяются под ногами. Чтобы изготовить такой кондуктор для сверления отверстий вам понадобится чертеж и базовые знания геометрии. Используемые материалы: кусок фанеры 15-18 мм, тонкостенная трубка, подходящая под сверло, несколько шкантов, и металлическая полоска для плеч параллелепипеда. Делаем три одинаковые детали: в середине отверстие, армированное трубкой, с нижней стороны симметрично расположены упорные ножки из шкантов. Важно, чтобы все три составляющие были абсолютно идентичными. Из металла нарезаем три одинаковых плеча с симметрично расположенными отверстиями. Именно они определяют линейность отверстий кондуктора. Выпиливаем пазы в трех заготовках, и соединяем их с помощью металлических плеч. Приспособление работает не хуже фабричного, при фактически нулевой стоимости. Еще один способ соединения мебели – использование так называемого конфирмата. Для этого нужен отдельный инструмент.
Изготовление самоцентрирующегося кондуктора — видео
Популярное: Пассатижи и плоскогубцы – отличие и сходство инструмента
Приспособление для сверления отверстий под шканты и конфирматы
Несмотря на то что на сегодняшний день в мебельной промышленности появилось много новой фурнитуры, старый добрый шкант применяется до сих пор. Это объясняется тем, что посредством этого предмета фурнитуры не видны соединения, и это особенно ценно в производстве мебели из натурального дерева.
Как уже говорилось, сверление под шканты создаёт немало проблем мебельщикам, особенно недостаточно квалифицированным.
Для того чтобы мебельные плоскости были идеально состыкованы, необходима точная разметка, а эта оснастка позволяет ускорить работу и довести качество таковой до нужного уровня.
Работа с конфирматами — специальными мебельными винтами — хоть и менее хлопотная, но тоже требует определённых навыков. А учитывая то, сколько нужно разметить и просверлить отверстий, перед тем, как закрутить конфирмат в одном мебельном изделии, такое приспособление в значительной степени ускорит работу, да и её качество тоже.
Простейшие устройства
- Кондуктор двухползунковый. Он позволяет сверлить отверстия в двух смежных (сопрягаемых) деталях. Приспособление сконструировано из двух линеек, которые служат направляющими и соединены с крепёжной планкой. Отверстия, выполненные в ней, дают возможность для установления планки на деталях разной ширины. Перемещаемые по линейкам корпуса (сменные) имеют набор направляющих втулок, где расстояния между ними разные. Кондуктор фиксируется посредством соединительной планки, с противоположной стороны же имеется ограничитель хода, поджимаемый винтом-барашком.
- Кондуктор многопозиционный. Крепится струбцинами. Конструкция позволяет производить вертикальное сверление. Изготовлен он из толстостенного алюминиевого уголка. Поскольку приспособление имеет значительную длину, оно оснащено промежуточным креплением в центре конструкции. Очень удачно применена толстая стенка уголка, что нельзя переоценить в момент накладки приспособления на поверхность детали и при переустановки кондуктора на 90°. Подбор расстояния между втулками осуществляется по самым распространённым величинам, предусмотренным для установки шкантов или конфирматов.
Порядок работы с кондуктором:
- Приспособление фиксируют на обрабатываемой детали.
- Гильзу вставляют в отверстие.
- Сверлят через гильзу.
Мебельный кондуктор своими руками: чертежи с размерами в помощь
Принцип этой оснастки:
- Корпус углового типа. Накладывается на плоскости деталей, которые потом будут соединяться между собой.
- Втулки направляющие.
Через них будет входить сверло.
- Зажимные устройства. Они фиксируют кондуктор и выполнены с торцевой части.
Проектирование собственного кондуктора должно основываться на том, чтобы с помощью этой оснастки можно было делать большую часть выполняемых работ, связанных с крепежами различных типов.
Важно! Коль нужен универсальный помощник — это касается профессиональных мебельщиков, то лучше будет приобрести промышленную оснастку, которая сделана более точно и качественно. Именно такое приспособление будет предпочтительным и быстро себя окупит, особенно, если ещё учесть и то, что к этому устройству зачастую прилагается немало различных шаблонов, упоров и других мелочей, которые также необходимы в работе. Обходятся они гораздо дешевле, чем при покупке в розницу.
И всё же это приспособление, по необходимости, можно сделать своими руками.
Такая оснастка, возможно, нужна не так уж и часто в том или ином производстве, а уж домашнему мастеру — тем более. Так что многим пользователям сделать её самому будет значительно выгоднее.
Если же проектирование таковой остаётся актуальным, то нужно подготовить материалы для изготовления самодельного кондуктора для сверления под конфирмат:
- Уголок. Свой выбор следует остановить на неравнополочном виде этого проката — его возможности более широки. Полку уголка надо выбирать наибольшей толщины, которая может доходить до 8 мм. Это вполне обосновано, поскольку тогда можно вставлять направляющие втулки, наружный диаметр которых достигает 6 мм. Исходя из этого, можно использовать свёрла от 3,5 до 4 мм. Если даже того диаметра и будет недостаточно, то материал рассверливают большим сверлом, не используя уже никаких других приспособлений.
- Направляющие втулки. Здесь будут предпочтительнее трубы из нержавеющей стали, которые подбираются, прежде всего, по внутреннему диаметру. Пример: труба 6×1,5 подходит для сверла не более 2,7 диаметром. Разъяснение: внутреннее отверстие её будет 3 мм, а небольшой зазор по всему внутреннему диаметру учитывается из-за термического расширения материала.
Длина втулки — это глубина отверстия в уголке, умноженная на два и более. Посадка втулок либо переходная, либо с натягом, либо по системе вала. Последняя является наиболее целесообразной.
Читать также: Колун из рельса своими руками
Вместо труб, конечно, можно использовать готовые втулки, применяемые в аппаратах по протяжке проволок — таковые имеются, например, в машиностроении. Такие детали (даже бывшие в употреблении), подойдут как нельзя кстати: они выполнены из легированных сталей и имеют практически неограниченный ресурс работы.
Выбор способа крепления
- Фиксация при помощи саморезов. Они вкручиваются в деталь, что не допускает смещения приспособления из-за силы трения. Это удобно тем, что эти отметки понадобятся для последующего сверления других отверстий.
- Упор пружинный. Он будет надёжно фиксировать кондуктор на детали. Для такого упора подойдёт плоская пружина с соответствующей силой прижима.
- Струбцины внешние. Под них необходимо подкладывать резиновые прокладки.
В качестве материала идеально подойдёт рифлёная резина. Это, конечно, немного увеличивает вес оснастки, а эластичность подкладок может негативно повлиять на перпендикулярность втулок. Чтобы этого не произошло, сверло заводят во втулку с целью разметки отверстия, а уж потом зажимаются струбцины.
Для сверловки труб и деталей цилиндрической формы
В современной мебели используются не только ДСП, ДВП, МДФ и дерево. В качестве дополнительных элементов могут применяться стальные трубы различного диаметра. Покрытые хромом или из нержавеющей стали, они отлично дополняют общий мебельный ансамбль.
Очень сложно просверлить сферическую поверхность — сверло так и норовит соскользнуть в сторону. Да и разметить не так-то просто, когда отверстий много и они располагаются в несколько рядов.
Для того чтобы из трубы не получился пресловутый дуршлаг, а правильная деталь с точно выполненными отверстиями, понадобится кондуктор — это идеальное решение в создавшейся ситуации.
Есть кондукторы стальные, выполненные в виде регулируемой струбцины. Эта особенность конструкции позволяет зажимать в них трубы разного диаметра и сверлить в них отверстия с высокой точностью.
Не имея возможности изготовить такое приспособление, можно использовать бросовые материалы, сделав ещё более простое устройство, используя брусок и полоску фанеры. Так, брусок, разрезанный вдоль по диагонали на циркулярной пиле, можно прибить гвоздями или прикрутить саморезами под углом в 90° к фанере. Полученное устройство накладывается сверху на трубу, а полоска фанеры, упираясь в стол или верстак, не даёт нарушиться заданному углу. Заблаговременно просверлённые в бруске отверстия нужного диаметра размещены с учётом необходимых расстояний между будущими отверстиями, что позволит быстро и точно просверлить трубу точно по чертежам.
Мебельные кондукторы и шаблоны своими руками
Как делаются кондукторы, теперь понятно, равно как и их необходимость для производства мебели.
Не только кондукторы, но и шаблоны необходимы в мебельном производстве. Простейший шаблон, порой сэкономит массу времени и даст возможность не менее точной сверловки, чем кондуктор.
Например, простейший металлический сборный накладной шаблон, состоящий из двух листовых заготовок размером 130×70 мм и стального квадрата сечением в 20 мм. Они соединены между собой винтами в верхней части конструкции — так прикреплены к квадрату. Квадрат просверлён под втулки, куда последние и запрессованы. Такое приспособление для сверления отверстий в торце детали, выполненной из ДСП, даст возможность сверлить, совершенно не задумываясь о разметке и перпендикулярном сверлении. А уж цена этой оснастки ниже всякого представления об экономии.
Вместо металла можно и нужно использовать те материалы, которые стоят недорого и легко обрабатываются.
- Фанера.
- Текстолит или стеклотекстолит — желательно толстый.
- Дерево твёрдых пород.
- Оргалит или его аналог.
Нужно иметь в виду, что эти материалы недолговечны, и для того, чтобы приспособления не приходилась делать каждый день, вполне резонно впрессовывать в них металлические трубки.
В заключение стоит подвести итоги сказанному. Делать кондуктор или шаблон самому или же купить его в магазине — это дело каждого в отдельности. Если домашнему мастеру надо сделать какую-нибудь мебель в единственном экземпляре и есть материал для кондуктора, а также и возможность его изготовления — можно воспользоваться этим. Возможно, что подобная оснастка мастеру больше никогда и не пригодится.
А вот если даже небольшая мебельная мастерская занимается производством серийной мебели, и в ней работает достаточно людей — проще, вероятно, приобрести что-то готовое, тем более, что эти незаменимые помощники мастеров понадобятся им в нескольких экземплярах.
В последнем случае имеет смысл приобретение более дорогих, точных и износостойких кондукторов вместо изготовления кустарных, которые менее точны и долговечны.
Станок для холодной ковки своими руками
Крепление элементов узора: последняя обработка металла
После того как все необходимые элементы орнамента созданы, начинается его формирование. Внешний вид узора может немного отличаться от эскиза. Чтобы определить возможные ошибки, нужно провести предварительный просмотр. Изначально узор можно выложить на плоской поверхности, не скрепляя его части. Таким образом можно оценить, насколько удалось воплотить задумку в жизнь, а также исправить недочеты в своей работе. Начинать формирование узора без предварительного просмотра результата не стоит.
Изделия смотрятся более целостно, если элементы соединены с помощью сварки.
Основных видов соединений два:
- сварочный шов;
- заклепки (или художественные хомуты).
Сварочный аппарат полезно использовать в тех местах, где шов соединения можно легко зачистить или он будет незаметен. Для сохранения эстетичности орнамента изделия из холодной ковки можно поставить фигурные заклепки. Они надежно скрепят составные части и дополнят декор.
Орнамент соединяют постепенно, в зависимости от количества деталей. Изначально скрепляют мелкие элементы, формируют просечки, витые линии и вензеля. Применяют сварку. Шов выравнивают болгаркой, используя зачистной круг толщиной 0,6 см. Он легко обходит изгибы и неровности. Крупные детали соединяют фигурными хомутами. Заклепки ставят симметрично друг другу, чтобы дополнить узор. В завершение работы орнамент обходят зачистным или полировочным кругом.
Холодная ковка позволяет создавать своими руками красивые и оригинальные изделия.
Художественная ковка не только является бизнесом или работой, но и может быть занимательным хобби. Оборудование холодной ковки своими руками может сделать даже начинающий мастер из подручных материалов. Специалистов по холодной ковке можно смело назвать художниками, так как они создают красивые орнаменты из неотесанных прутьев, труб и листов. Подобные увлечения требуют полной отдачи и немалых затрат. Однако все вложенные средства и старания принесут свои плоды, если они подкреплены желанием создавать прекрасное.
Изготовление простейшей детали на станке
Отрезают заготовку из полосовой стали в нужный размер. Этот размер обычно уточняют, прорисовывая готовое изделие и его составляющие элементы.
Свободный конец устанавливают в центр спирали. С помощью внутреннего винта производится фиксация заготовки.
Выполняется поворот «Улитки». Заготовка плотно прижимается к направляющим. Тут требуется прилагать определенные усилия, чтобы получать нужный профиль изделия.
Проворачивая приспособление дальше, осуществляют изготовление завитка. При необходимости вставляют другой конец заготовки и производят изготовление замкнутого или разомкнутого завитка.
Обычно другой конец не остается прямым. Его тоже изгибают. Поэтому различают внутренние и наружные обратные завитки. На самом приспособлении с помощью маркера или мела делают отметки. По ним ориентируются, когда изготавливают завитки с требуемыми параметрами.
Как видно из пошагового руководства, используя простой набор инструментов, самодельный станок для изготовления завитков несложен в изготовлении. Сколько он стоит? Его цена определяется стоимостью заготовок. Часто цена минимальная.
Процесс холодной ковки
При холодном варианте ковки потребуется два основных процесса:
Необязательно иметь в своем распоряжении полноценные станки для художественной ковки, часто любители изготавливают инструменты своими руками. С помощью самодельного оборудования можно придавать заготовкам всевозможные причудливые формы. Нужно только обзавестись определенными навыками работы. Поэтому готовьтесь к тому, что для того, чтобы согнуть требуемую фигуру, будут необходимы чертежи и немалые усилия. Выполнение работ возможно только с использованием сырья необходимой толщины.
Изделия, которые получаются с помощью самодельного станка для холодной ковки, намного крепче тех, которые выполняются или отливаются с помощью штамповки. Так происходит за счет того, что металлические прутья, которые проходят через оснастку, прессуются вместе с приданием им необходимой формы. При этом способе ковки нужно не допускать ошибок, так как они практически не исправляемы. С приобретением навыков вы сможете создавать своими руками привлекательные и замечательные изделия.
С помощью самодельного станка для холодной ковки, можно изготавливать такие изделия, как:
- элементы вроде балконных козырьков, поручней для лестницы;
- решетки на окна;
- ограды и заборы;
- мебель для дома – столы, стулья, кровати;
- элементы, которые используются в дизайне дома: обрешетки каминов, треноги для цветов.
При обработке большой партии однотипных изделий своими руками все можно сделать при помощи трафаретов и чертежа. Так удается значительно уменьшить трудозатраты и сократить время изготовления. Иногда детали необходимо нагреть, прогревание делают на участках стыков, чтобы не было кривизны. Новичкам рекомендуется перед выполнением работ тщательно продумать план изготовления, нелишним будет видео урок и выполнить чертеж будущего изделия.
Гнутики, фонарики, волны и другие станки
Как видите, все остальные виды станков для холодной ковки мы собрали в одном маленьком разделе. Откуда к ним такое неуважение в отличие от улитки и торсиона, о которых мы рассказывали в отдельных разделах? Ответ будет честным в виде совета:
Если вы решили сделать кузнечный станок своими руками, остановите свой выбор на двух станках: улитке и торсионе. Во-первых, они абсолютно необходимы с функциональной точки зрения, во-вторых, они достаточно просты для самостоятельного исполнения.
Виды холодной ковки.
Остальные станки типа фонарика или волны можно соорудить намного позже, когда вы поймете, что холодная ковка – это ваше, и когда у вас в голове появятся конкретные творческие планы.
Гибочный станок не нужно делать своими руками, его лучше купить в готовом виде по двум важным причинам:
- Клинья и ролики, с помощью которых меняются размеры изготавливаемых элементов, должны быть выточены с соблюдением идеальных размеров.
В домашних условиях это сделать практически невозможно.
- Гибочные станки стоят совсем недорого, так что требование экономии бюджета будет выполняться.
Имея в своем распоряжении три самых нужных станка – самостоятельно сделанные улитки и торсион и купленный гибочный станок – можно приступать к холодной ковке практически любой сложности. Осталось решить еще один небольшой вопрос.
Приспособление «Улитка»
Инструмент «Улитка» предназначен для получения завитков (или спиралей) и «валют» (S-образных деталей). Встречаются различные конструкции.
Один из вариантов конструкции: 1 — лемех улитки; 2 — основа станка; 3 — прижимной валик; 4 — рычаг для управления прижимным валиком; 5 — крепление основы; 6 — палец для фиксации лемехов; 7 — паз для прижиного валика; 8 — ось рычага управления; 9 — пружина для прижатия валика; 10 — фиксатор для заготовки; 11 — ведущий лемех улитки; 12 — основная ось; 13 — рычаги
В результате должно получиться такое приспособление:
Ещё одна лёгкая конструкция, чтобы гнуть прокат сечением до 12 мм:
1 — сегмент улитки; 2 — эксцентрик; 3 — ручка; 4 — основание; 5 — направляющие полозья; 6 — ось; 7 — ползун; 8 — гайка оси; 9 — ось крепления ролика; 10 — ролик; 11 — приводная ось; 12 — направляющая эксцентрика; 13 — центральный сегмент улитки; 14 — барашек эксцентрика; 15 — основная ножка; 16 — соединительный штифт сегментов улитки; 17 — корректирующий винт; 18 — соединительное ухо сегментов улитки
Часто приспособление «Улитка» делают на опоре, особенно если гнуть нужно толстый прокат.
Несколько полезных видеоматериалов по самодельных станкам «Улиткам».
Вариант с массивным основанием на опоре:
https://youtube.com/watch?v=seLFHFY0acA
Видео 2. Изготовление основания
Видео 3. Изготовление улитки
https://youtube.com/watch?v=rUTdr5Cb9SE
Видео 4. Работа станка
Вариант настольного приспособления:
https://youtube.com/watch?v=NFBf7cF_Ggs
Видео 5. Часть 1
https://youtube.com/watch?v=UCQtMsI56JU
Видео 5. Часть 2
Подробнее о таких конструкциях мы поговорим ниже.
Технология изготовления приспособления «Улитка»
Упрощенно технологический процесс изготовления станка «Улитка» своими руками можно представить в виде ряда последовательных операций.
На листе бумаги вычерчивается профиль изделия, который требуется изготовить. При вычерчивании выдерживаются размеры изделия. Чертеж нужен только для получения профиля самой детали
Внимание! При проработке учитываются толщина заготовки. Нужен зазор не менее 3…4 мм, тогда изделия можно снять после его изгибания в приспособлении.
Для большинства станков изготавливают центральный упор
В нем будет фиксироваться начало.
Разные мастера используют свои приемы фиксации, поэтому изделия у них можно отличить по почерку.
Из стального листа вырезается опорная пластина. К ней будет привариваться центр, а также спираль. Толщина пластины должна быть не менее 3 мм, так как будут прилагаться значительные усилия. Размер пластины в будущем определит и параметры завитка.
Пользуясь чертежом спирали, изгибается из полосы заготовка. При ее гибке контролируются параметры. Чем точнее будет изготовлен этот элемент, тем проще будет выполнять изготовление элементов для кузнечных изделий. Внимание! При необходимости изготовления завитков с количеством витков более одного нужно срезать полосу спирали по диагонали. Поэтому используют полосу значительно ширины. Минимальный размер соответствует высоте профиля, который собираются гнуть на станке.
Приспособление размещают на специальной стойке, чтобы легче формировать готовые изделия. Для небольших по размеру деталей удобно размещать на вертикальной стойке.
Чтобы проще выполнять работу приваривают ручку. Ее устанавливают с обратной стороны, чтобы не мешала устанавливать и снимать заготовки.
Изготовление «Улитки» с приводом
«Улитка» с электроприводом облегчает изготовление завитков и «валют». Особенно это ценно, когда работа не «для души», а для изготовления большого количества однотипных изделий на потоке при работе на заказ.
Ниже приведены этапы сборки станка для гиба прута максимальным сечением 10х10 мм. Двигатель мощностью 0,5 КВт/1000 об/мин работает при этом на пределе своих возможностей. Выполняет 6 оборотов вала в минуту. Сегменты улитки выточены из круглой болванки Ст.45 без термообработки высотой 25 мм и толщиной 20 мм. Улитка насажена на вал на подшипниках от заднего колеса мотоцикла — 7204. Поддерживающий ролик закреплён жёстко в пазу. Между двигателем и редуктором установлены шкивы.
Ниже приведены чертежи сегментов улитки.
Элемент улитки 1
Элемент улитки 2
Элемент улитки 3
Центральный элемент улитки
Для более массивного прута (от 12 мм) мощность двигателя должна составлять более киловатта. На фотографиях ниже представлен станок с двигателем мощностью 2,2 кВт, 1000 об/мин, дающий выход на валу около 10 об/мин. Это уже станок для профессионального использования. Применён бывший в употреблении редуктор, матрица вырезана из заготовки толщиной 30 мм — самый трудоёмкий процесс.
Для холодной ковки ещё понадобятся наковальня и молот. Горн не нужен, он требуется только для горячей ковки.
Совет! Перед началом работ начертите эскиз будущей конструкции в натуральную величину. Это поможет корректировать элементы и не запутаться при сборке.
рмнт.ру
Холодная ковка
Таких недостатков горячей ковки, как:
- большая трудоемкость,
- высокие требования к квалификации мастера,
- низкая повторяемость изделий.
Холодная ковка
Недостатков лишен метод холодной ковки. Он основан на свойстве металлов изменять в определенных пределах свою форму под воздействием механического усилия. Технология применима к пруткам круглого и квадратного сечения, металлической полосе, трубам и прокату различного профиля. Несколько базовых операций, таких, как
- изгиб заготовки под заданным углом и по заданному радиусу,
- формирование завитков и спиралей,
- скручивание одной или нескольких заготовок по продольной оси
и комбинация получившихся деталей позволяет создавать кружевные ограды, беседки, скамейки, элементы декора и домашней утвари в разумные сроки и по приемлемой цене, в разы, а то и в десятки раз ниже, чем при использовании горячей ковки.
https://youtube.com/watch?v=8_YpUI6vqww
Для получения основных элементов используют специальные станки.
- Гнутик — один из самых популярных. Он позволяет сгибать пруток под заданным углом и по заданному радиусу, в том числе и в виде волны.
- Улитка служит для закручивания конца прутка или трубы в спираль
- Торсион предназначен для скручивания прутка вдоль его продольной оси.
Если планируется выпуск больших серий изделий — то понадобится станок промышленного производства. Он обладает высокой производительностью, достаточным ресурсом, снабжен электроприводом достаточной мощности, совмещая в себе гнутик, улитку и торсион. Передовые производители оснащают свои агрегаты полуавтоматическими приставками, и роль работника сводится к установке нужной оправки, закреплению заготовки и запуску программы. Система сама регулирует скорость подачи, силу прижима формующего ролика, начало и окончание формовки.
Станки для ковки
цена этого оборудования довольно большая
Если домашний умелец сделает какое-то изделие на самостоятельно изготовленном кондукторе, то вещь будет уникальной, хотя по некоторым параметрам и будет уступать той, которая сделана в заводских условиях. Если планируется делать большое количество деталей с помощью холодной ковки, то лучше всего сделать кондуктор с электромотором. Так вы облегчите себе рабочий процесс.
Полезным будет предусмотреть изготовление на станке основных видов работ – вытяжки, гибки и закручиваний. Эти устройства можно объединить во время создания кондуктора своими руками.
Во время вытяжки изделию придается определенная форма. Для чего ее нужно пропустить через валики или пресс, причем сечение исходного сырья уменьшится.
Процесс гибки состоит в том, что деталь гнут под требуемым углом. Выполнить эту операцию можно с помощью шаблонов. Они делаются таким образом: подготавливается чертеж изделия, по которому после делается шаблон. На стальную пластину приварите завитушку, после этот лист крепится на станке в держателе. Окончание заготовки устанавливают в прорезь, второй конец фиксируется. С помощью рычага происходит воздействие на один конец изделия, которое нужно протащить по всем изгибам пластины, используемой в роли шаблона.
Часто мастера сами собирают простые устройства, с помощью которых можно изготавливать довольно оригинальные изделия. Тут все зависит от опыта мастера. Рассмотрим одну из таких самодельных моделей, чтобы понять сам принцип.
Станок для холодной ковки своими руками: чертежи и инструкции
Известными, благодаря наружному виду, считаются металлические изделия, которые сделаны методом ковки. Такой декор отличается ценой, поэтому не каждый может заказать их себе. Однако, помимо горячей технологии ковки, необходимой для изготовления деталей из металла, существует и холодная. Последний вариант есть возможность сделать самому, для этих целей потребуется изготовить станок для холодной ковки собственноручно.
Устройство станков для ковки по холодному типу
Конструкция станковЛюбой прибор для проведения ковки холодным способом обладает характерными чертами и качествами. Чтобы сделать качественный станок для холодной ковки своими руками, важно выяснить, как он устроен.
- Гибочные. Изменяя положение роликов и клиньев, изменяются габариты волн и изгибов. Из-за этого изгибаются прутья до 1,6 см. Единственным недостатком применяемого механизма станет невозможность изготовления его самому.
- Твистер. Снабжен спецшаблоном, к нему придавливают используемую металлическую часть. Сохранность шаблона обеспечивается упорным рогом.
- Основание с проставками. Прибор помогает делать любые узоры.
Конструкция отличается простотой, основой является пластиной из материала высокого качества, куда вкручиваются проставки на определенной дистанции. Этот тип прибора эффективен для металла в толщину 0,6 см.
- Улитки. Изделие является пластинкой-основой, где расположен спецвиток. Его применяют как шаблон для обрабатываемой детали. Характерной чертой станет то, что «улитка»-шаблон разделена на фрагменты, закрепленные друг с другом с помощью соединительных спецэлементов. Это даст возможность при работе шаблону менять форму, ввиду чего будут созданы разнообразные волны и изгибы. Для изготовления такого станка потребуется выбирать крайне надежный материал, которой не будет гнуться по прошествии времени.
- Торсионный станок. Подобное приспособление эффективно для винтового скручивания прута. Устройство делают из цилиндрического металлического каркаса и 2 фиксирующих элементов. Принцип работы заключается в том, что прутья помещают в крепежные элементы. С одной стороны их зажимают, а с другой закручивают до необходимых размеров винтовой волны.
Важно! До того, как создать устройство, необходимо ознакомиться с чертежами станка для холодной ковки.
Разновидности и назначение станков для ковки
*
Механизм облегчит работы вручную и создать уникальные изделия. Для ковки холодным методом мастера применяют различное оборудование, которое минимизирует физ. усилия человека и позволяет провести такие основные действия:
- согнуть профиль под необходимым углом;
- изготовить спирали либо завитки;
- скрутить детали вдоль.
Различные механизмы помогают создавать уникальные конструкции, художественное полотно для беседки, декор для скамьи в парке, прочие предметы разнообразного предназначения.
Виды приборовДекор-станки дают возможность создавать схожие по форме и параметрам детали за короткий временной интервал, помогают уменьшить их себестоимость и сроки изготовления.
Такие станки бывают профильными (выполняют лишь одно действие) и универсальными. Выделяют такие спецстанки:
- гнутики;
- улитки;
- торсионы;
- штамповочные.
Универсальные модели состоят из компонентов спецтехники в разных комбинациях.
Станок «улитка»
«Улитка»*
Алгоритм сборки станка для холодной ковки своими руками не вызовет сложностей. Во время создания улитки вероятны 3 типа конструкции, и то относительные. Каждый специалист делает завиток, спираль и изгиб изделия по-своему.
По виду исполнения механизмы бывают 3 видов:
- монолитные с фиксированным шаблоном изгиба;
- со съемным изгибом, дающим возможность делать различные завитки;
- с разборными составляющими завитка и крутящейся столешницей, чтобы получать сложные профили изгиба.
Монтаж станка начинают с конструирования основных узлов приспособления:
- Каркас. Механизм должен быть изготовлен из металла. Древесина совсем непригодна для сборки прибора: продолжительные и чрезмерные нагрузки разрушают дерево за несколько использований. Как основной материал используется уголок, трубы с толстой стенкой либо швеллер.
- Столешница. Ее изготавливают из плиты из металла, которая вырезана в форме окружности, по толщине 0,4 см. Из такой плиты вырезают вторую столешницу, которая повторит по форме первую. На последней располагаются составляющие, производят изгибы заготовок. При холодной ковке столешница будет принимать большую нагрузку, потому не требуется экономить и создавать ее из тонколистового железа.
- Главный вал и рычаг. Вал расположен посередине, его окружают столешницы. Фиксируется к каркасу 4 треугольниками. Механизм сделан из трубы с толстой стенкой нужного диаметра. Рычаг крепят к валу посредством кольца и вращают вокруг его оси. Вспомогательно на него устанавливают ролик, чтобы сгибать прутья.
Станок торсионный
*
Обыкновенное скручивание ряд пользователей осуществляют, не используя станок. Зажимается одно окончание детали в тисках, а второе обращается благодаря стандартному вороту. При такой методике обрабатываемая заготовка скручивается, однако иногда и вытягивается. Во избежание этого, сооружается направляющая конструкция в качестве желоба. Необходимо учитывать:
- протяженность желобка – он не может быть длиннее детали, уменьшаемой во время деформации;
- ширину желобка – требуется, чтобы он вдвое был шире изделия, поскольку в процессе деформации оно увеличится.
Возможно достичь ожидаемых результатов без оборудования – в таких целях потребуется приложить усилия и потратить большое количество времени. Те, кто предпочитает собрать необходимое устройство, должны спроектировать такую спецтехнику.
Торсионный станокСборка такого станка собственноручно возможна в 2 вариациях: стандартная и универсальная. Первая станет улучшенным способом работ с тисками, а вторая предоставит шанс создавать уникальные детали.
Главное рабочее усилие, которое требуется, чтобы деформировать материал, принимает опора, потому основание создаваемого устройства должно отличаться высокой прочностью. В таких целях используется двутавр либо 2 швеллера, которые сварены друг с другом. Устойчивости для каркаса добавляют лапы, которые приварены к устройству. Затем возможно изготавливать остальные элементы – заднюю бабку и шпиндель.
В узлах механизма из профильной трубы своими руками находятся патроны, назначением которых станет их размещение внутри заготовки. Они должны обладать прочными фиксаторами (для надежного крепления). Ввиду уменьшения длины используемого изделия во время скручивания заднюю бабку выполняют скользящей. Допустимо сооружать ее из тисков, закрепляя на основании посредством болтов.
Подвижный элемент шпинделя проворачивают при помощи ручки, которая предусматривает наличие нескольких рычажков, имеющих необходимую длину для гашения прилагаемых усилий.
Сборка торсионного прибораВажно! Возможно добавить втулки из резины, чтобы защитить руки от скольжения.
*
Основным различием в алгоритме монтажа универсального прибора станет устройство подвижного элемента. Он предполагает винтовую подачу при изготовлении фонарей, фиксируется с помощью стандартного скручивания. Потому активный элемент снабжается 2 шпинделями. В этом варианте для скользящей бабки требуется фиксирующий винт.
Когда нужно сделать деталь, которая скручена лишь на конкретном фрагменте, к прибору добавляют ограничители. Их изготавливают по принципу задней бабки – присутствуют спецзажимы и есть опция скольжения.
Работы в такой ситуации крайне утомительны, получение изделий высокого качества представляет собой трудоемкий процесс. Потому оснащение электрическим приводом изделия станет наилучшим решением.
Станок «гнутик»
Приспособление отличается эффективностью, массивностью, простотой монтажа. Но существенным минусом станет то, что сложно отыскать и подогнать детали. Назначением устройства станет сгибание под различными углами детали, потому понадобится прикладывать значительные усилия на, следовательно, требования к монтажу станут выше.
Для каркаса приспособления подбирают толстую раму из стали. Следует учитывать, что устройство крепится к столу. В основном делается крепеж с помощью болтового соединения, к примеру, как в тисках. В середине рамы есть направляющая, отличающаяся подвижностью. Ее приводят в действие с помощью эксцентрикового механизма, фиксируемого на раме-каркасе. Вспомогательно устанавливаются 3 упора, которые создают необычную «вилку» – это рабочие составляющие устройства. С учетом профиля сгиба они меняются: круглые валы – чтобы выполнить волну, «молоток» – чтобы формировать углы.
«Гнутик»Рабочие комплектующие изготавливаются лишь из особой стали. Они будут отвечать за прочность всей конструкции. Чтобы обрабатывать и подгонять изделия, понадобятся непосредственно спецнавыки и соответствующие инструменты. Потому, когда присутствуют трудности в заказе, при покупке либо изготовлении главных узлов, то рекомендуется приобрести устройство в магазине. Его цена не слишком высока, однако он может дополнительно использоваться, чтобы сгибать трубы.
Станок «волна»
Более логично называть рассматриваемое изделие управляемой волной. Устройство оснащается 2 стальными дисками в диаметре 14 см. Они фиксируются посредством болтов к столешнице. На основном диске закрепляется ось, которая вращает универсальный вороток.
Управлять рассматриваемым приспособлением нужно, меняя дистанцию меж дисков. Во время обкатывания воротом прута формируется узор. Когда прут снимают с кондуктора, образуется узор со второй стороны.
«Волна»Станок — пресс
*
Чтобы формировать наконечники прутьев, потребуется воспользоваться прессом. Рассматриваемое устройство функционирует аналогично маховику: изначально вращается штанга с грузиками, отводится винтовой боек до конца назад. Затем вставляется внутрь гнезда другой штамп и ставится обрабатываемое изделие. После, штанга быстро раскрутится в противоположный бок. Боек будет бить по хвостовой части штампа, вследствие чего образуется усилие необходимое в целях штамповки.
Детали, которые изготовлены методом холодной ковки, соединяют 2 методами:
- Сварка — изделия приваривают, окалину стачивают «болгаркой» либо иным оборудованием.
- Хомуты — подобный тип соединения выглядит значительно ярче.
Окрашивают заготовки, применяя спецэмали либо краски из акрила.
ПрессКак сделать своими руками станок для холодной ковки
Для монтажа станка для холодной ковки своими руками потребуется осуществить следующие действия:
- Сначала собирается стойка, выступающая в качестве опоры. В этих целях каждый элемент (фрагменты трубы аналогичных размеров и сочленения с верхней и нижней стороны) соединяются в одно целое. Устройство снаружи напоминает табуретку. Монтажные работы производят, используя сварочный аппарат, нарезку — применяя пилу.
- Теперь требуется нарезать металлические листы. Получатся круги одинакового диаметра и 4 треугольника, которые имеют одинаковые стороны. Треугольные составляющие привариваются к нижней части конструкции так, чтобы вышло что-то схожее с пирамидой. Основание с более широкой площадью приваривается к центру вырезанного круга.
- 4 планки, расположенные по горизонтали, присоединяются к окружности с приваренным элементом. Подобное осуществляется, применяя болты (используют дрель для сверления отверстий).
- Последующим действием станет изготовление рукоятки. Требуется использовать 2 прута разной длины. Определяются их габариты методом соотношения с диаметра и окружности. Первый прут долен совпасть по размерам, второй несколько превышать его параметры. Во время сгибания первого прута требуется соблюсти необходимый угол. После этого углы привариваются между собой, затем вниз вваривается третий прут. Должна присутствовать перемычка меж начальных двух отрезков, к ним присоединяют спецрычаг.
- Подшипник для разнообразия направлений в приспособлении прикрепляется к окончанию приваренного рычага, к отрезку, который находится в нижней половине устройства. Верхний отрез играет роль крепления для металлической катушки (монтируется по горизонтали, помогает сгибать металл). Снизу отрезка, где находится свободное окончание, проделывается отверстие.
- Завершающим шагом изготовления станет монтаж изготовленной рукоятки с элементом, который напоминает «пирамиду». Фиксируются такие детали после одевания рукоятки механизма с помощью гайки большого диаметра. На нее заранее приваривается круг из металла, дающий возможность закрепить шаблон. Затем «улитку» необходимо присоединить, используя сварочный аппарат. Теперь механизм будет готов к эксплуатации.
Соблюдая несложный алгоритм действий, домашний специалист или мастер сможет создать устройство высокого качества.
Для создания механизма самому требуется быть внимательным в процессе проектирования чертежей и произведения необходимых расчетов. В других моментах алгоритм изготовления простой. Установив принцип работы прибора, возможно придумать ему оригинальные вариации, способствующие улучшению обрабатываемых заготовок.
Кондуктор для холодной ковки своими руками видео
Холодная ковка невозможна без специального кузнечного оборудования.
Если вы только собираетесь организовать мастерскую холодной ковки и хотите избежать больших расходов, то самостоятельное изготовление станков и приспособлений поможет создать свой маленький бизнес без чрезмерных затрат.
Основные приспособления и станки
Станки для холодной ковки предназначены в основном для гибки по дуге или углом, а также для скручивания. Они могут быть ручные или с электрическим приводом.
Основные виды станков и приспособлений для холодной ковки:
Приспособление «Гнутик»
Покупной или сделанный самостоятельно «Гнутик» — универсальное приспособление, позволяющее получить дугу или угол из прута. Он представляет собой основание с ползуном, на котором закреплен упор с углом (90° или другим по необходимости) и двумя цилиндрическими неподвижными упорами. Перемещая ползун и угловой упор, прут сгибается под углом. Для получения дуги предусмотрен третий цилиндр, вращающийся на противоположной от углового упора стороне.
Приспособление может быть выполнено на горизонтальной или вертикальной платформе.
Аксонометрия приспособления «Гнутик» — вертикальное расположение
Чтобы смасштабировать размеры, приводим чертёж нижней планки этого «Гнутика».
Это приспособление — универсальное. С помощью насадок на нем можно не только гнуть, но и резать, и пробивать отверстия. Но это уже будет следующим шагом.
Получение дуги на «Гнутике»
Получение угла на «Гнутике»
Так выглядит самодельный «Гнутик»:
Приспособление «Твистер»
«Твистер» — инструмент для скручивания прутков, в основном квадратного сечения, вдоль продольной оси. Это несложное приспособление может быть ручным и с электроприводом. Принцип действия: закрепляются оба конца прута, потом одно крепление начинает проворачиваться, скручивая металл до необходимой формы.
Внешний вид покупного ручного «Твистера»
Посмотрите фото самодельного «Твистера» с электроприводом, собранного с использованием электрооборудования бывшего в употреблении:
Для изготовления «Фонариков» и «Шишек» существует специальный станок, но для начала можно использовать и «Твистер», как это показано на видео (англоязычное, но всё предельно понятно).
Видео 1. Как сделать заготовку под «Фонарик» на «Твистере»
Приспособление «Улитка»
Инструмент «Улитка» предназначен для получения завитков (или спиралей) и «валют» (S-образных деталей). Встречаются различные конструкции.
Один из вариантов конструкции: 1 — лемех улитки; 2 — основа станка; 3 — прижимной валик; 4 — рычаг для управления прижимным валиком; 5 — крепление основы; 6 — палец для фиксации лемехов; 7 — паз для прижиного валика; 8 — ось рычага управления; 9 — пружина для прижатия валика; 10 — фиксатор для заготовки; 11 — ведущий лемех улитки; 12 — основная ось; 13 — рычаги
В результате должно получиться такое приспособление:
Ещё одна лёгкая конструкция, чтобы гнуть прокат сечением до 12 мм:
1 — сегмент улитки; 2 — эксцентрик; 3 — ручка; 4 — основание; 5 — направляющие полозья; 6 — ось; 7 — ползун; 8 — гайка оси; 9 — ось крепления ролика; 10 — ролик; 11 — приводная ось; 12 — направляющая эксцентрика; 13 — центральный сегмент улитки; 14 — барашек эксцентрика; 15 — основная ножка; 16 — соединительный штифт сегментов улитки; 17 — корректирующий винт; 18 — соединительное ухо сегментов улитки
Часто приспособление «Улитка» делают на опоре, особенно если гнуть нужно толстый прокат.
Несколько полезных видеоматериалов по самодельных станкам «Улиткам».
Вариант с массивным основанием на опоре:
Видео 2. Изготовление основания
Видео 3. Изготовление улитки
Видео 4. Работа станка
Вариант настольного приспособления:
Видео 5. Часть 1
Видео 5. Часть 2
Подробнее о таких конструкциях мы поговорим ниже.
Приспособление «Глобус»
Такое устройство внешне похоже на школьный транспортир и предназначено для изготовления дуг с большим радиусом изгиба из полосы, квадрата, круга или шестигранника. Сначала загибом фиксируется один конец заготовки, потом она изгибается по всей длине по шаблону. Принцип действия чем-то похож на работу закаточной машинки для консервации.
Внешний вид приспособления
Видео 6. Работа на «Глобусе»
Пользуясь исключительно мускульной силой, дугу большого диаметра можно изготовить на шаблоне, прикрученном или приваренном к верстаку. На нём хорошо гнуть полосу, трубу тонкостенную и т. д.
Приспособление «Волна»
Получить волнообразные изделия из заготовки круглого, квадратного, шестигранного сечения или трубки можно на приспособлении «Волна». Деформация заготовки происходит между вертикальными валками прокручиванием.
Приспособление волна и полученные изделия
Видео 7. Приспособление в действии
Приспособление «Фонарик»
На этом станке изготавливают заготовки элементов «Фонарики» или «Шишки», которые могут состоять из 4-х, 6-ти, 8-ми и более прутков. По принципу действия станок похож на «Твистер», но тут заготовки изгибаются вокруг направляющего вала, что формирует более правильную и точную конфигурацию изделия.
Видео 8. Работа приспособления для изготовления «Фонарик»
Приспособление для холодной ковки элемента «Хомут»
Элемент холодной ковки «Хомут» предназначен для фиксирования между собой других элементов конструкции.
Приспособление для гибки «Хомута» можно выполнить по прилагаемым чертежам.
Приспособления для выполнения «гусиной лапки»
«Гусиная лапка» — расплющивание с нанесением красивых насечек концов заготовок для придания большей изящности конструкции или с целью уменьшения толщины для различных соединений.
Концы элементов оформлены «гусиной лапкой»
Эту операцию можно выполнить при помощи станка с матрицей или приспособлением и тяжелым кузнечным молотом на наковальне. Оба варианта мы даем в виде видеоматериалов.
Видео 9. Станок для изготовления «гусиной лапки»
Видео 10. Приспособления для ковки «гусиных лапок»
Видео 11. Подробный процесс изготовления штампа
Ниже прокатный станок для выполнения той же операции.
Станок для прокатки «гусиной лапки» (расстояние между вальцами регулируется). Материалы для прокатного станка: шестерни и валы — запчасти от комбайна б/у
Изготовление «Улитки» с приводом
«Улитка» с электроприводом облегчает изготовление завитков и «валют». Особенно это ценно, когда работа не «для души», а для изготовления большого количества однотипных изделий на потоке при работе на заказ.
Ниже приведены этапы сборки станка для гиба прута максимальным сечением 10х10 мм. Двигатель мощностью 0,5 КВт/1000 об/мин работает при этом на пределе своих возможностей. Выполняет 6 оборотов вала в минуту. Сегменты улитки выточены из круглой болванки Ст.45 без термообработки высотой 25 мм и толщиной 20 мм. Улитка насажена на вал на подшипниках от заднего колеса мотоцикла — 7204. Поддерживающий ролик закреплён жёстко в пазу. Между двигателем и редуктором установлены шкивы.
Ниже приведены чертежи сегментов улитки.
Элемент улитки 1
Элемент улитки 2
Элемент улитки 3
Центральный элемент улитки
Для более массивного прута (от 12 мм) мощность двигателя должна составлять более киловатта. На фотографиях ниже представлен станок с двигателем мощностью 2,2 кВт, 1000 об/мин, дающий выход на валу около 10 об/мин. Это уже станок для профессионального использования. Применён бывший в употреблении редуктор, матрица вырезана из заготовки толщиной 30 мм — самый трудоёмкий процесс.
Для холодной ковки ещё понадобятся наковальня и молот. Горн не нужен, он требуется только для горячей ковки.
Совет! Перед началом работ начертите эскиз будущей конструкции в натуральную величину. Это поможет корректировать элементы и не запутаться при сборке.
Очень популярными благодаря своей красоте и изысканности давно стали изделия из металла, сделанные при помощи ковки. Такие декоративные элементы достаточно дорогостоящие и не всегда есть возможность заказать себе все желаемые украшения в интерьер или загородный дом. Но, помимо горячего вида ковки, которая нужна для того, чтобы создавать металлические декоративные конструкции, есть холодная ее разновидность. Последний вариант можно реализовать самостоятельно, для этого понадобиться соорудить станок для холодной ковки своими руками, после чего можно будет приступить к реализации всех задумок и идей.
Станок для ходолной ковки своими руками
Разновидности станков
В основном все приспособления, которые предназначены для изготовления деталей из металла при помощи ковки холодного типа характеризуются ручным приводом. По принципу электропривода работают немногие из них, хотя соорудить такую конструкцию можно с каждым из приспособлений. Единственный вопрос относительно привода – это целесообразность, потому как затраты на энергоресурс, который питает агрегат и сложность процесса установки механизма могут не оправдывать себя, если соотносить их с количеством выполняемой работы и ее регулярностью.
В таблице указаны все приспособления, которые работают за счет привода ручного типа, относящиеся к процессу холодной ковки.
Устройство | Краткое описание |
Твистер | При помощи такого устройства происходит закручивание металла, формирование спиралей и завитков, имеющих узкую сердцевину. |
Станки торсионного типа | При помощи такого станка происходит закручивание прутов винтового типа, а также возможно изготовление спиралей большой величины и филаментов (корзинок, фонариков и луковиц). |
Инерционно-штамповочные станки | Предназначаются для того, чтобы изготавливать соединительные части меду декоративными составляющими, делать узорные наконечники и различный мелкий рисунок и рельеф. |
Станки для гибки | Существует несколько разновидностей таких станков: нажимного, протяжного и комбинированного типов. Первая разновидность нужна для того, чтобы получать волнообразные изгибы или зигзагообразно изогнуть прут. Протяжная разновидность востребована, когда необходимо изготовить кольцо, завиток или спираль, имеющую широкую сердцевину. Используя комбинированную разновидность можно соорудить любой из перечисленных элементов. |
Справка: очень часто в некоторых источниках можно встретить название станков, предназначенных для кручения также как и для станков, которые делают навивку — твистеры. Однако это не совсем верно, станки, которые закручивают металл – это станки торсионного типа.
Видео по изготовлению станока для холодной ковки своими руками.
Отличия холодной ковки
Существует такое понятие как «штамповка», которое иногда путают с холодным типом ковки. Сама же холодная ковка имеет 2 принципа, по которому может происходить этот процесс. В таблице указаны различия процессов.
Процесс | Описание |
Штамповка | Процесс штамповки можно описать как выдавливание определенных фигур при помощи пуансона, который работает при высоком уровне давления. Примером процесса штамповки служит алюминиевая банка. Нагрев металла при этом не используется. Возможность применить такую технологию дома вряд ли возможно, поскольку невозможно создать для этого необходимые условия. |
Холодный тип ковки (наклепывание) | Такая разновидность холодной ковки, по сути, есть наклеп, а именно проводится в процессе определенное число ударов очень большой силы, что позволяет структуре металл изменяться и становиться необходимых параметров по размеру и форме. Такая манипуляция проводится при помощи молота, который также можно соорудить своими руками. |
Холодный тип ковки (гнутье) | Иная разновидность – это гнутье. При такой технологии металл по структуре остается прежний, не меняя своих характеристик. Этот тип ковки возможен для использования дома, для него лишь нужно заняться созданием станка для холодной ковки своими руками. |
Ковкой холодного типа, которая проводится по принципу гнутья заниматься довольно просто, особенно если имеется специальное оборудование стационарного типа, которое облегчает существенно процесс. Преимуществом такой разновидности является и то, что собрать практически любой станок для холодной ковки своими руками можно без больших затрат на это.
Видео обзор ручного станка для ковки металла
Устройство станков для ковки по холодному типу
Каждое приспособление для того, чтобы можно было заниматься холодной ковкой, имеет свои особенности и параметры. Чтобы беспрепятственно можно было сделать станок для холодной ковки своими руками, необходимо разобраться, что представляет собой каждый из них.
Станок | Устройство | |
Гибочные станки | Конструция этого устройсвта такова, что при помощи изменения роликов и клиньев меняется размер волн и изгибов. Им возможно изгибать прутья до 16 мм. Единственный нюанс этого устройства- его нельзя сделать самостоятельно, потому как требуется обрабатывать и вытачивать много деталей точного размера. Стоимость такого приспособления невелика. | |
Твистер | Работает агрегат благодаря оснащению его специальным шаблоном, к которому придавливается обрабатываемый кусок металла. Давление при этом должно быть очень большим, поэтому те, кто работают на твистере, должны обладать достаточной силой для этого. Кроме этого, сохранность самого шаблона обеспечена наличием упорного рога (концевого). Что касается серединного рога, который иначе назван обводящим, то его следует делать таким образом, чтобы он мог менять свое положение и быть в нем зафиксирован. От этого зависит эффективность работы, особенно для тех, кто приступает к процессу впервые. | |
Основание с проставками | Такой агрегат позволит сделать узоры абсолютно любых вариаций. Сама по себе конструкция очень проста и представляет собой пластину из прочного и надежного материала, в которую вкручены проставки на определенном расстоянии. Для таких целей можно использовать болты с размерами от м8 до м24. Толщина металла при этом зависит только от мастерства того, кто работает на станке. В основном такое приспособление хорошо подходит для металла с толщиной 6 мм. | |
Улитки Станок-твистер | С воротом | Такая установка представляет собой пластину-основу, на которой находится специальный виток. Такой виток используется в качестве шаблона для будущего изделия. Особенность станка в том, что «улитка»-шаблон разделена на несколько частей, которые закреплены между собой при помощи специальных соединительных элементов, что позволяет во время работы шаблону варьировать по форме, чем и создаются различного рода волны и изгибы. Минусы в такой конструкции тоже есть, поскольку для того, чтобы изготовить такой станок для холодной ковки своими руками необходимо подбирать очень прочный материал, которой не согнется со временем. Также продумывать соединительные петли, которые достаточно уязвимы, учитывая величину силы, с которой происходит весь процесс сгибания металла. |
Рычажного типа | В таком типе станка «улитка» шаблон прикреплен очень прочно к основанию. Производительность у него за счет такого факта меньше, однако, надежность больше. при помощи специального рычага осуществляется прижим металлической пластины к шаблону, одновременно в процессе необходимо перемещать передвижной ролик. Чтобы сделать такой станок для холодной ковки своими руками можно использовать стальной материал, который отличен свей прочностью, а ролик можно выполнить из обычного роликового подшипника. В целом конструкция схожа с трубогибом. | |
Торсионный станок | Такое устройство хорошо поможет в винтовом скручивании прутьев. Такой станок делается из основы цилиндрической формы из металла и двух крепежных и одновременно скручивающихся элементов. Желательно оснастить такую конструкцию специальной парой лап, которые не будут давать обрабатываемому металлу гнуться не так как необходимо. Принцип работы на станке таков, что прут помещается в удерживающие его элементы, с одного конца зажимается, а с другого конца с помощью вращающегося шпинделя закручивается до нужного размера винтовой волны. |
Оснащение электроприводом торсионного станка для холодной ковки
Для того, чтобы повысить не только эффективность работы на агрегате для холодной ковки, закручивая в винтовую волну прутья, но и увеличить скорость, а также обеспечить стабильность и не подвергаться переутомлению, можно установить привод электрического типа.
Работая вручную достаточно непросто сделать все элементы декорирования из металлических прутьев одинаковыми, поскольку равномерность вращательного момента при такой ситуации будет сильно варьировать. Для того чтобы избежать ошибок при изготовлении изделий можно воспользоваться:
- полуосью от автомобиля, которая установлена на ведущем мосту;
- также понадобится зубчатая пара дифференциала;
- для защиты стоит воспользоваться кожухом.
Из перечисленных приспособлений можно соорудить электрический привод к торсионному станку. Такой двигатель лучше чтобы не превышал показатели мощности в 900 об/мин и 3 кВт.
Построение завитка для станка своими руками
Прежде чем приступать к созданию станка для холодной ковки своими руками необходимо уметь рассчитывать параметры шаблонной спирали, потому как специальных программ для таких целей практически нет. Такой шаблон должен быть не только грамотен со стороны технической, но еще и иметь привлекательный вид.
В основе расчетов такого шаблона положена логарифмическая спираль. Некоторые нюансы при построении можно выделить в следующий список:
- начало построения берется в точке R0;
- радиус поворота будет равен фиксированному углу;
- показатель длины такого угла должен быть умножен на расхождение витка;
- расхождение в стандартном варианте в основном берется равное 1,2;
- для простоты расчетов, а также сохранения точности угол изгиба лучше всего брать угол в 45 градусов;
- если есть необходимость построить шаблон, который будет иметь более плотную спирать, то следует прибавлять к величине радиуса 8ую часть (s) единичного расстояния от спирали;
- что касается r0, то он должен быть равен по величине поперечного сечения размера диаметра, которым обладает заготовка для спирали.
Важно: r0 может принимать любое значение, все зависит от того, каких характеристик для заготовки металл используется, а именно от его плотности.
Учитывая все нюансы можно приступать к изготовлению «улитки»-шаблона, для этого лучше всего уметь решать уравнения, имеющие кубическую степень и выше. Точной формулы для расчетов такого устройства не имеется, но то, которое позволяет добиться оптимального результата, есть. Последовательность при построении спирального шаблона может быть такой:
- первостепенно определяется начальная точка r0;
- витки, которыми будет обладать шаблон, берутся произвольно, их количество может быть любым;
- используя табличные данные, следует произвести расчет поперечника (b), при этом следить за тем, чтобы он был меньшим по ширине в проеме под шаблон;
- пользуясь формулой, проводится расчет радиуса R;
- последний шаг – это перенос всех полученных точек в соответствии с масштабом, после чего можно приступать непосредственно к построению. В процессе допустим подгонять пользуясь аналогичной формулой радиус R в окончательном варианте.
Справка: если появится необходимость провести расчеты промежуточных значений, то делается это в соответствии с геометрической пропорцией.
Сооружение станка для холодной ковки
При составлении чертежа для дальнейшего создания шаблона для станка лучше всего позаботиться о том, чтобы он имел максимальное количество различных вариаций касаемо изгибов и волн. Имея такие заготовки можно создать станок для холодной ковки с множеством сменных насадок, что будет давать возможность изготавливать различные узоры и вензеля.
Последовательность действий при создании устройства:
- Изначально понадобиться металлическое полотно, размер которого будет зависеть от количества узоров, размещаемых на нем. Размещать сами шаблоны следует таким образом, чтобы было место для изготовления изделий, потому как в процессе материал с насадок может смещаться из-за нехватки места. Также при недостаточном удалении друг от друга шаблонов, могут возникнуть осложнения в работе.
- Что касается самих вариаций шаблонов, то они могут быть как простыми, так и содержать не один поворот вензеля. Можно сделать подобную улитку лемешного типа и продумать конструкцию изгибов в разобранном и собранном состоянии. При этом стоит быть внимательными при подборе материала для фиксации раздвигающихся частей – он должен быть максимально прочным.
- Смену насадок можно обеспечить, сделав прорезь прямоугольной формы, в нее можно будет вставлять сменные шаблоны для ковки. Прикреплены они все должны быть к металлическим пластинам, имеющим форму прямоугольника. Крепление таких насадок обеспечено будет при помощи болтов.
Видео инструкция
Сборка устройства
Такой вариант станка используется для примера по причине его простоты. Зная основные принципы и последовательность конструирования оборудования, его можно модернизировать по своему желанию. Чтобы собрать все части оборудования в единое целое, необходимо будет воспользоваться:
- дрелью с твердосплавным типом сверл;
- аппаратом для сварки;
- пилой, разрезающей металл, либо ножовкой;
- металлическим полотном выбранного размера;
- круглой трубой из металла;
- прутом металлическим;
- разной величины подшипниками;
- болтами размером м8.
Чтобы собрать станок для холодной ковки своими руками необходимо воспользоваться проверенной последовательностью действий:
- Изначально необходимо собрать стойку, которая будет служить опорой. Для этого все ее составляющие (отрезы трубы одинакового размера и сочленения между ними с верхнего и нижнего краев) необходимо соединить в единое целое. Конструкция по внешнему виду может напомнить табуретку. Соединение проводить при помощи аппарата для сварки, а нарезаются отрезки пилой.
- Следующим шагом является нарезка листов из металла. Должны получиться круги равных диаметров и четыре треугольника, имеющих равные стороны. Элементы треугольной формы необходимо приварить на низ соединенной конструкции труб таким образом, чтобы подучилось нечто подобное пирамиде. Основание, которое имеет более широкую площадь необходимо приварить в центральной точке вырезанной окружности.
- Четыре планки, которые расположены горизонтально необходимо присоединить к кругу с уже приваренным элементом. Произвести это следует, используя болты, для этого понадобится дрель, чтобы проделать отверстия.
- Следующий шаг – сооружение рукояти. Чтобы это сделать нужно воспользоваться двумя прутьями различной длины. Определить их размеры можно, соотнеся их с диаметром круга. Один прут должен быть соизмерим с диаметром, другой немного превышать его размер. Сгибая первый прут, следует соблюдать угол в 30 градусов при этом. Оба прута после этого приварить друг к другу, после чего в нижнюю часть вварить еще один прут. Также должна быть перемычка между первыми двумя отрезками, к которой присоединяется сваркой рычаг, который должен сохранять направление в сторону сооружения из прутьев.
Подшипник для будущей вариабельности направлений в устройстве необходимо прикрепить к концу присоединенного рычага, а также к отрезку, находящемуся внизу конструкции. Верхний отрез служит креплением для катушки из металла, устанавливать которую необходимо горизонтально – она дает возможность загибать металл. С нижней стороны отрезка, где имеется свободный конец, следует проделать отверстие, равное по диаметру размеру сечения трубы.
Кто решил всерьез заняться ковкой и сделать станок для холодной ковки своими руками, следует быть очень скрупулезными на этапе создания чертежей и расчетов. В остальном процесс создания достаточно прост, а разобравшись в принципе конструкции оборудования, можно придумывать ему различного рода вариации, которые помогут совершенствовать изделия.
Один из способов украшения участков — использовать кованные изделия. Очень декоративно смотрятся заборы, скамейки, беседки, перила для лестницы и другие подобные сооружения. Причем в большинстве случаев данные изделия не есть ковка в ее традиционном понимании. Чаще всего это сделано не в кузне и не при помощи молотка и наковальни, а при помощи некоторых устройств, которые позволяют создавать из металлических полос и квадратных прутков самые различные узоры и изделия. Для изготовления подобных изделий потребуются станки для холодной ковки. Часть из них можно сделать своими руками другую проще купить.
Какие вообще устройства используются
Для холодной ковки характерны различные завитки, изгибы, витые прутки и т.п. Почти под каждый вид делают на отдельном приспособлении — определенном станке. Привод у них может быть ручной, а может — электрический. Для небольших объемов «для себя» применяют ручные станки для холодной ковки. Они хоть и не особо производительны, но намного проще в изготовлении. Если необходимо ставить изготовление «на поток» делают аналогичные устройства, но уже с электромоторами. В этом случае работать физически почти не нужно, но сложность изготовления приспособления возрастает в разы. В нашем материале поговорим о ручных станках для холодной ковки.
Какие же устройства используют:
- Торсионные. С их помощью четырехгранные прутки или полосы металла скручивают в продольном направлении. Получается витые столбики, которые называют еще торсионами.
Так выглядит торсион и одноименный станок
Так делают «фонарик»
Приспособление для холодной ковки улитка — для формирования завитков
Для изгиба в любом месте и на любой угол — гнутики (гибочные станки)
Станок «Волна» — для формирования соответствующего рельефа
Станки для оформления концов прутков. В данном случае — гусиная лапка
Для начинающего мастера наиболее актуальный станок для холодной ковки — улитка. Только с его помощью можно сделать множество интересных вещей — начиная от забора и калитки и заканчивая скамейкой и другими подобными изделиями. На втором месте по степени необходимости торсионный станок. Он добавляет разнообразия в детали. Все остальные можно приобретать или делать по мере совершенствования и набора мастерства.
Самодельные «Улитки»
По сути это модернизированный гибочный станок (трубогиб), но эти усовершенствования позволяют легко делать завитки из довольно толстых прутков (сечением до 10-12 мм) и повторять их с высокой степенью точности.
Один из самодельных станков для холодной ковки
Конструкций эти станки для холодной ковки имеют несколько, но проще всего в реализации вариант с круглым столом, имеющем центральную ножку. К ножке подвижно закреплен рычаг с роликами на подшипниках на конце. Они облегчают процесс гибки.
Поверхность стола можно сделать из стального листа толщиной от 10 мм и больше. Для ножки можно использовать любую толстостенную круглую трубу. Важно сделать конструкцию устойчивой, так как будут прилагаться боковые усилия, потому нужны боковые стойки, распорки, а также устойчивое основание.
Чертеж станка для холодной ковки «Улитка»
Рычаг проще делать из квадратной трубы с толстой стенкой — не меньше 2-3 мм. Сечение трубы 25*40 мм или около того. Крепление рычага к ножке можно сделать на подшипнике, а можно просто взять небольшой кусок толстостенной трубы большего диаметра, надеть ее на ножку, а снизу приварить полосу-упор — чтобы рычаг вниз не падал. Вариант с подшипником дает более легкое движение, но при наличии смазки и второй вариант рабочий.
Вариант крепления рычага
Важна еще форма рычага. Рычаг двойной, верхняя часть — рабочая, нижняя — опорная. Везде где есть соединения желательно доварить усиление, так как усилия значительные.
Рычаг должен быть надежным, с усилением
На столе закрепляется оправка или кондуктор — форма, по которой сгибаются завитки. Делают их разного диаметра — чтобы можно было делать разные по диаметру завитки. Такие оправки могут быть сборными — для формирования большего количества изгибов. В каждом таком образце должны быть стержни, которые устанавливаются в отверстия в столе. Так этот шаблон фиксируется. Также его форма должна быть разработана с таким учетом, чтобы конец прутка в ней хорошо фиксировался.
Вариант кондукторов для улитки
Часто оправки вытачивают из металлического круга подходящего диаметра при помощи болгарки, но есть варианты из металла с наваренными на него стальными пластинами, изогнутыми соответствующим образом.
Как сделать подобный станок для холодной ковки — в следующем видео. Там же неплохо описан способ доведения концов заготовки до приличного состояния — обычные необработанные края смотрятся очень грубо. Для их обработки есть специальное оборудование, но, как оказалось, можно справится и без него.
Торсионный станок
Как уже говорили эти станки для холодной ковки позволяют сделать на прутке продольные изгибы. Это относительно несложная конструкция. Основная задача — закрепить неподвижно один конец прутка, ко второму приделать рычаг, при помощи которого можно будет скручивать заготовку.
В качестве основы подойдет обрезок профилированной трубы с толстой стенкой (не менее 3 мм). Фиксатор можно сварить из тех же прутков, оставив квадратный просвет нужного диаметра. Можно использовать зажим для троса подходящего размера (можно найти в магазине такелажа). Любой из этих упоров приваривается к основанию.
Держатель для троса — отличный фиксатор для прутка
Далее надо каким-то образом обеспечить захват и кручение второй части заготовки. Можно это сделать при помощи двух подшипниковых узлов. Внутрь вставляется труба подходящего диаметра, с одной стороны к ней приваривается ручка — конструкция напоминает букву «Т». С другой стороны в трубе делают фиксатор: сверлят четыре отверстия, в них вваривают гайки под 12 или 14 болты. В результате получается неплохой фиксатор — болты закручивают после того, как вставили пруток.
Дальше — дело техники — рычагом наворачиваем нужное количество витков. Нельзя сказать, что эта работа для слабаков, но при большом рычаге все не так уж и сложно.
Еще более простой станок для изготовления торсионов методом холодной ковки в следующем видео.
Видео про самодельные приспособления и станки для холодной ковки
Приспособление для ковки чертежей своими руками. Как сделать улитку из холодной ковки своими руками? Холодная штамповка
Элементы Curl из стержней широко используются в оформлении прилегающих территорий и интерьера жилых помещений. Для их изготовления используются специальные приспособления … Одно из них — улитка. Часто мастерицы сами конструируют это приспособление из подручных материалов. Если вы тоже хотите узнать, как изготавливается улитка методом холодной ковки вручную, то эта статья для вас. Из него вы узнаете принцип работы этого устройства, его преимущества и разновидности, простейшие чертежи и технологию самостоятельной сборки.
Улитка для холодной ковки — устройство для создания узоров в виде завитков из металлических стержней путем их деформации по контуру шаблона. Деформация происходит из-за жесткой фиксации рабочего бруса к шаблону. Для этого нужно приложить силу. Это обеспечивается ручным усилием или электрическим приводом. При самостоятельном изготовлении устройства целесообразность использования электропривода должен определять сам мастер. Это необходимо при большом объеме работы. В основном используется ручное усилие.
Улитка (кондуктор) может иметь разную конструкцию … Это можно сделать:
- в виде шаблона, стабильно приваренного к рабочему основанию;
- в виде разборно-съемных частей, которые крепятся к основанию.
Ручной привод также может быть организован по-разному.
В самом примитивном исполнении планка наматывается на шаблон простым усилием рук или с помощью любого подходящего приспособления в качестве рычага.
Кроме того, рычаг может входить в конструкцию станка и прикрепляться к ножке станины и приводиться в движение с помощью подвижного подшипника, перемещающегося по основанию спиральной камеры.
В более сложных устройствах вращается сам кондуктор, который прикреплен к оси вала. Он приводится в движение тремя рычагами.
Необходимо заранее определиться с конструкцией машины, исходя из целесообразности и удобства использования.
Монолитное приспособление имеет определенную форму шаблона, которая служит единственным вариантом скручивания. Это недостаток такой конструкции, но сделать его самостоятельно несложно.
Съемный вид конструкции удобен тем, что на таком станке можно делать фигурные завитки разных размеров и форм.Но конструкция самой машины более сложная. Кроме того, у съемного устройства надежность крепления частей шаблона хуже, чем у монолитного вида. Вам потребуются постоянные перекручивания резьбовых соединений, так как они могут расшататься в процессе эксплуатации.
Изготовление простой улитки своими руками
Если вы остановились на упрощенной монолитной конструкции, то знаете, что в этом устройстве используется простая накрутка планки усилием рук или с помощью рычага на форму жестко приваривается к рабочей поверхности.Такой станок можно использовать для создания завитков на брусьях с небольшим сечением (менее 12 мм).
Монолитная неразборная улитка
Делается так:
- Сначала на листе бумаги будущего шаблона строится схема с необходимыми размерами (иногда схему шаблона наносят прямо на основание шаблона). дирижер). К этому нужно подойти ответственно, ведь после сварки готовой формы исправить ошибки не удастся. Толщина очертаний формы на чертеже должна быть такой же, как толщина металлической полосы, использованной для ее изготовления.Он должен быть не менее 3 мм. Катушки необходимо разместить на расстоянии 12-13 мм друг от друга, чтобы в паз между ними вошел 10-миллиметровый деформируемый брус.
- Основа улитки (желательно круглой) вырезается из стального листа толщиной не менее 4 мм, размер диаметра которого определяется пропорционально размеру спирали шаблона и должен быть больше размера улитки. . Обычно диаметр основания находится в пределах 70 см.
- Завиток желаемой формы изготавливается из металлической полосы толщиной 3 мм в соответствии с чертежом.Для этого заготовку лучше отжечь, чтобы ее было легче обрабатывать. После изготовления формы лишний конец полоски срезается, а края улитки обрезаются до конуса и очищаются.
- Готовую форму приваривают к основанию, которое крепится к станине. Иногда шаблон, приваренный к основе, закрепляют на станине с помощью установленных на нее тисов. Для этого к тыльной стороне основы формы привариваются к брусу для захвата тисом.
С возможностью фиксации кондуктора в тисовом зажиме можно легко менять шаблоны и получать завитки различной формы, если сделать несколько типов, монолитно приваренных к основанию устройства.
Съемная конструкция- На рабочей базе сначала наносится контур улитки с отметкой по контуру расположения отверстий для крепления шаблона.
- По эскизу из толстой стальной полосы изготавливается шаблон и в нем просверливаются отверстия. Он прикручен к основанию.
Ковку скрученной формы нужно начинать от центрального завитка. Конец заготовки вставляется в паз первого завитка формы и плотно прижимается к нему.Для надежной фиксации можно использовать небольшой зажимной инструмент. Свободная часть планки с усилием навинчивается на форму шаблона с помощью приспособления — рычага. В усовершенствованных конструкциях используется рычаг, который приводится в движение прикрепленным к нему подвижным подшипником. Рычаг сделан из стержня диаметром 20 мм.
Изготовление такого устройства Вы можете посмотреть на видео:
Улитка разборная с вращением
Шаблон улитки может состоять из нескольких частей, а деформация планки происходит за счет вращения кондуктора.Такая машина состоит из следующих элементов:
- толстая металлическая основа в виде диска или квадрата;
- разборный шаблон, закрепленный на базовой платформе;
- вал вращения;
- рычаг привода вала.
Рабочая база изготовлена из металла толщиной от 4 до 10 мм.
Сборный шаблон может состоять из нескольких частей, которые соединяются между собой шарнирными штифтами, вставленными в отверстия проушин, приваренных к концам элементов.Вместе они образуют контур улитки.
Чтобы прикрепить такую улитку к рабочему основанию, в ней необходимо просверлить отверстия, чтобы зафиксировать ее на поверхности в определенном положении. Изменяя положение сборных деталей на основе, можно получить разную кривизну локонов и их форму. Размер дуги формы регулируется специальными винтами, закрепленными на соединительных петлях.
Самостоятельно изготовить композитную улитку на шарнирных соединениях довольно сложно. Обычно мастера приобретают штамп промышленного производства и прикрепляют его к кровати.
Вы можете сами сделать более простое разборное шаблонное устройство без использования петель. Для этого нужно сделать набросок сборных частей улитки с местами отверстий. Если подготовить несколько эскизов и в соответствии с их контурами просверлить отверстия в основе в разных местах, то на одной основе можно закрепить шаблоны с разным радиусом. Для этого нужно прикрутить отрезки контура в точках совпадения отверстий шаблона и основания.
Например, можно сделать такой вариант:
Устройство с съемными частями спирали и вращающимся цилиндрическим валом, приводимое в действие рычагом, показано на видео:
Чертежи ковки улитки
Начинающие мастера часто обходятся без рисунок, прорисовывающий контуры улитки по самому основанию без каких-либо расчетов. На первое время это приемлемо, но если вы хотите сделать качественный станок-улитку для холодной ковки, то все равно нужно использовать чертежи, в которых рассчитаны все параметры.В зависимости от типа выбранной конструкции у улиток существуют разные варианты их рисунков, по которым изготавливаются эти устройства. Например, схема устройства-улитки, представленная на фото, представлена ниже.
На схеме также описан принцип работы такой машины, в которой используется привод с помощью трех рычагов, которые вращают вал и спиральную камеру.
Гибка осуществляется после жесткой фиксации конца заготовки на первый виток формы шаблона с помощью фиксатора и последующего наматывания стержня на вращающийся спиральный шаблон при вращении вала.
Кованые изделия, изготовленные методом горячей и холодной обработки. Последний метод не требует специальных навыков, но для его реализации нужны специальные приспособления. Существуют различные чертежи станков для холодной ковки, многие из которых подходят для самостоятельного создания инструмента.
Технологические особенности
Металлические кованые элементы в результате деформации, при этом в процессе работы следует учитывать эксплуатационные характеристики материала.
Структура кристаллической решетки металла состоит из зерен неправильной формы.Инструмент, используемый для ковки, воздействует на нее и изменяет внешний вид детали. Особое значение имеет подбор чертежей станков, так как заготовка должна сохранять прежние свойства.
Самодельный станок для холодной ковки: правила изготовления
Существуют определенные правила, соблюдение которых обеспечивает получение необходимого результата:
- Создание подходящей конфигурации возможно с помощью нескольких инструментов.
- Перед началом изготовления рассчитываются параметры формованных изделий.
- Прутки, используемые для заготовок, могут иметь различный диаметр, который выбирается с учетом степени сложности технологии и последующей эксплуатации.
- Подлежит только обработке, т. К. Другие виды не обладают необходимой пластичностью.
«Гнутик»
Для холодной ковки можно сделать самому, достаточно разобраться в тонкостях использования инструмента и выбрать подходящий чертеж … «Гнутик» требуется для создания углов различной конфигурации.Его основные конструктивные элементы — подвижный упор и два вала, размещенные на стальной пластине.
Самодельная холодная ковка такого типа должна быть создана по некоторым характеристикам. Например, изначально необходимо определить угол отклонения. Также можно добавить дополнительный изгибающий элемент, в случае его использования устанавливается третий вращающийся вал.
Инструмент изготовлен из специальной стали, так как в процессе работы подвергается большим нагрузкам. Стоит отметить возможность сбора различных деталей, в том числе волнистых.
«Твистер» и «Улитка»
Сегодня художественная ковка не обходится без винтовых деталей. Для их создания предусмотрены ручные станки для холодной штамповки под названием «Твистер». У них есть характерная особенность, заключающаяся в прокрутке стержня по оси. Инструмент состоит из подвижной и фиксирующей части. Поворотная ручка деформирует заготовку, которая закреплена между основными частями конструкции. Стоит отметить, что спираль образуется со стороны крепления изделия, и прилагаемые силы можно уменьшить при правильном расчете прижимного рычага.Это устройство позволяет изготавливать детали для металлических заборов и оконных решеток.
«Улитка» — это простая самодельная машина для холодной ковки, обеспечивающая формирование спиралей с необходимым количеством витков. Он наиболее популярен и может быть адаптирован для изготовления желаемого продукта. Инструмент комплектуется ручным или электроприводом, тип которого выбирается в соответствии с интенсивностью использования.
Самодельный станок для холодной ковки: подготовка материалов
Для начала нужно нарисовать спираль с одинаковым шагом всех витков.В этом случае нужно начинать с используемых заготовок, так как ширина хода обычно находится в пределах 15 мм, тогда как инструмент предназначен для прутков сечением 10 мм. Для маневра необходимо свободное пространство, так как при полном сжатии заготовки изгиб станет невозможным.
Далее нужно вырезать из стального листа пластину 20х20 см. Несмотря на небольшой размер, он обеспечит оптимальную производительность рабочего процесса. В соответствии с длиной намеченной «улитки» из стали делается пропил.Полоску необходимо согнуть плоскогубцами, положить на тарелку и обвести ярким маркером со всех сторон.
Далее отрезается часть стержня длиной, равной ширине стальной полосы. Главное, чтобы он не превышал этот параметр, так как это может привести к травмам в процессе сгибания. Стержень необходим для закрепления материала на первом этапе создания изделия, чтобы предотвратить свободное движение в одной точке.
Отрезается часть длиной 10 см.Он объединит лист и основу, на которой будет производиться фиксация. из-за высоких степеней нагрузок следует использовать только толстостенные материалы. После того, как все основные элементы подготовлены, можно собрать самодельный станок для холодной ковки, чертеж которого представлен ниже.
Сборка конструкции
Стальная «улитка» разделена на витки, первый из которых будет удерживать заготовку, а на остальных — витки стержня. Центральная часть приваривается к основе, при этом полученный шов должен быть без малейших изъянов.К основной части планки приваривают куски стержня, расстояние между ними должно быть 3 см. Необходимо соблюдать осторожность при формировании швов, а затем сбивать их молотком.
Затем участки полосы устанавливаются в необходимых местах и обводятся маркером. Получившиеся кружочки нужны для образования дырок. Они должны точно соответствовать диаметру ножек, чтобы обеспечить простоту установки и снятия.
Завершающим этапом является приварка профильной трубы в нижней части, а также фиксирующего элемента рядом с «спиралью».Фото самодельных станков для холодной ковки, изготовленных аналогичным способом, представлено выше.
Комментарии:
Ковка металла — это процесс его обработки под давлением. В ходе этого процесса металлическая заготовка часто подвергается воздействию инструмента (молотка, наковальни и т. Д.). От этого он деформируется таким образом, что приобретает нужную форму и размер.
Фото 3. Аппарат «Гнутик» используется для изготовления различных дуговых изделий.
Виды ковки металла
Ковка металла бывает холодной или горячей.Для проведения процесса горячей обработки требуется специализированное оборудование, которое можно установить только в цехе, оборудованном как кузница.
Холодную ковку можно сделать своими руками в домашних условиях и превратить это занятие в личное хобби.
Фото 1. Аппарат «Волна» предназначен для отделки профильных и круглых труб.
В процессе обработки металла холодным способом заготовку подвергают одновременно прессованию и гибке.Таким образом можно придать изделию желаемую форму с необходимым изгибом. Но важно помнить, что при подобном способе отделки материала все должно быть рассчитано правильно, ведь провести такую процедуру повторно на одной и той же заготовке будет невозможно.
Холодная ковка металлического изделия позволяет придать ему индивидуальность и необычность. Такая металлическая деталь всегда будет изготовлена в одном экземпляре. Очень часто такая металлическая отделка используется для изготовления заборов, решеток для окон, элементов украшения каминов.Также из него можно создавать предметы мебели (столы, стулья, различные табуреты, полки и т. Д.).
Фото 2. С помощью устройства «Твистер» можно крутить металлический стержень вдоль его оси.
Для обработки продукта существует несколько основных типов инструментов, в том числе следующие:
- «Волна».
- «Твистер».
- «Гнутик».
- «Улитка».
- «Фонарь».
С помощью адаптации данных и умения работать с ними можно добиться художественной ковки… Они помогут создать множество оригинальных изделий, форма которых будет зависеть от личных вкусовых предпочтений.
Вернуться к содержанию
Привязка инструментов к заготовкам
Фото 4. Устройство «Улитка» используется для художественной ковки детали и изготовления ее в виде спирали.
С помощью прибора для измерения волн вы можете создавать различные изогнутые элементы, напоминающие форму волны. Если пропустить через этот инструмент металлическую заготовку (квадрат или пруток), то получится ровное волнистое изделие в форме синусоиды.Этот инструмент также может использоваться для чистовой обработки фасонных и круглых труб, шестигранных заготовок и труб с малым диаметром поперечного сечения (Фото 1).
Устройство «Твистер» в некоторых случаях называют «фонариком». С помощью «твистера» можно крутить металлический брус вдоль своей оси. Эту операцию можно выполнить с помощью обычного бруска, квадратного бруска и металлической полосы. Размер обрабатываемого круглого бруса составляет 30-35 мм, квадратного бруса — 16-20 мм. И ширина полосы не должна быть больше 30 мм (Фото 2).
Фото 5. Устройство «Фонарик» используется для изготовления переплетенных изделий.
Gnutik — это фундаментальный инструмент в этом процессе. С его помощью можно гнуть пруток, квадрат, шестиугольник и полосу. Вы можете выбрать любой угол изгиба. Также его можно использовать для изготовления различных дуговых изделий. Радиус этих изделий можно установить на любой (Фото 3).
Из подручных материалов можно изготовить станки для холодной ковки.
Поскольку универсальные устройства от производителей имеют довольно высокую стоимость, самодельный станок для холодной ковки металла станет отличным решением для людей, занимающихся изготовлением кованых изделий.
Сегодня металлические конструкции уникального дизайна и смелых архитектурных форм используются для обустройства домов в коттеджных поселках.
Изогнутые кованые элементы ворот, заборов и калиток придают необычный вид ландшафтному дизайну усадьбы.
На предложенных фото видно, как необычный художественный вид создают металлические конструкции.
Какие детали можно изготовить на станке холодной ковки
Холодная штамповка, в отличие от горячей технологии, проста и безопасна.Этот процесс не требует использования горячего металла и точного соблюдения рабочей температуры.
Станок холодной ковки можно сделать своими руками специально для изготовления определенного вида деталей.
Также самодельный станок позволит решать самые разные задачи, поэтому будет просто универсальным.
Благодаря самодельному станку можно будет добиться идеальной геометрии металлических элементов по индивидуальной дизайнерской задумке и сделать своими руками оригинальные детали с рисунком.
В процессе холодной декоративной ковки, как правило, используется мягкий металл — это могут быть никелевые и магниевые сплавы, сталь, медь или латунь.
Остальной ассортимент выпускаемой на станке продукции будет ограничиваться только фантазией и способностями мастера.
При желании можно сделать ажурные элементы для лестниц, ворот и заборов своими руками.
Использование декоративных деталей позволит украсить камины и мангалы, красиво украсить внешние стены дома и беседки, сделать оригинальные треноги для цветов, как на фото.
Типы оборудования для холодной ковки
Существующие типы станков могут эксплуатироваться с участием электродвигателя или ручного усилия.
Первая версия устройства позволяет выполнять работы быстрее ручных, но при этом требует определенных навыков от мастера.
Ковочные станки делятся на типы:
- улитка — станок с отдельными съемными деталями или цельнолитой — применяется при изготовлении спиральных отдельных деталей;
- универсальное приспособление — используется для резки, клепки и придания объёма изделию;
- связка — с его помощью можно производить дуговую гибку металла или гибку деталей под определенным углом;
- устройство для формирования колец;
- твистер — позволяет гнуть изделие по оси;
- пресс — для формирования матричного оттиска на изделии;
- волна — для извлечения металлических стержней волнообразных элементов.
Изготовление станка-улитки
Используя список инструментов и металлических деталей, приведенный ниже, вы можете собрать цельный станок со спиральным корпусом.
Для работы вам потребуются:
- металлических стержней;
- листов и полос стальных;
- труба стальная профильная;
- сварка, плоскогубцы, болгарка.
Рисунки и пошаговая схема, а также просмотр тематического видео позволят получить качественный светильник с необходимыми параметрами:
- С помощью бумажки нарисуйте на нем трехвитковую спираль.Далее проверяем размеры, чтобы в результате в резьбу вошел армированный стержень диаметром 10 мм;
- С помощью болгарки вырежьте две пластины из стального листа. Первый должен иметь параметры 100х100 мм, второй — 130х130 мм;
- Возьмите стержень диаметром 3 см и три стальных полосы. Края участков всех используемых деталей необходимо отшлифовать, чтобы избавиться от заусенцев;
- С помощью плоскогубцев согните стальные полосы по шаблону, в результате вы получите три спиральные части разной длины;
- С помощью сварки свариваются все элементы станка по схеме, сварочные работы рекомендуется проводить качественно, так как именно от них будет зависеть срок службы инструмента;
- Стальная труба приваривается последней снизу по центру машины.
В результате проведенных работ должно получиться оборудование для холодной ковки металла, как на фото.
Если при отделке каких-либо элементов интерьера обрезкой профильных труб никто не испытывает затруднений, то при необходимости выполнить их гибку, наоборот, все усложняется.
Качественно и быстро эти работы выполнят специальные трубогибочные станки, которые можно сделать заранее своими руками.
Чертежи для изготовления данного вида оборудования могут использоваться по-разному, в зависимости от того, какие материалы будут использоваться в работе.
Собрать станок производственного типа для холодной штамповки металла, как на фото, сложно на первый взгляд.
Но если мастер, работающий с металлом, уже набрался опыта, для него нет ничего невозможного. Главное — выбрать прочный, устойчивый фундамент для будущего сооружения.
Например, это может быть массивный металлический стол на основе труб или профиля.
Поскольку изгиб металла будет происходить за счет присутствующих в конструкции валов, необходимо выбрать три таких элемента.
Каждый из них представляет собой металлический цилиндр с толстыми стенками и осью вращения. Два цилиндра закреплены немного над столом, а третий, центральный, расположен над ними.
Расстояние между двумя крайними цилиндрами определяет угол, на который будет изгибаться труба.
Для того, чтобы можно было при необходимости изменить положение цилиндров, необходимо внести в конструкторские чертежи дополнения в виде стопоров и роликов, которые сделают эту деталь регулируемой.
После закрепления цилиндров необходимо организовать для них систему передачи вращения.
Для этого используют цепной механизм от старого автомобиля, который можно найти на вторичном рынке.
Лучше, если механизм будет укомплектован шестернями, если нет, то их придется покупать отдельно.
Шестерни установлены на двух крайних цилиндрах, а натяжитель расположен под валами в центре. Затем один из внешних цилиндров снабжен ручкой для создания вращающей силы.
Станок для холодной штамповки металлических изделий готов. Следующее видео поможет дополнить приведенный выше материал деталями.
Как изготовить торсион
Станок для холодной штамповки торсионных изделий предназначен для скручивания металлических спиралей в виде змейки.
С таким устройством сложно работать вручную, поэтому чаще всего чертежи с электрическими опциями станков.
Для того, чтобы правильно собрать торсион, предлагаем посмотреть видео и ознакомиться с приведенной ниже инструкцией.
Инструменты и материалы для сборки станка:
- лист стальной;
- Балка двутавровая;
- тиски и застежки;
- коробка передач, электродвигатель, цепь;
- болгарский;
- сварка.
Схема:
- Основой будет двутавр, к одной стороне которого нужно приварить стальной лист;
- Затем к стали прикрепляют тиски, приваривают и фиксируют болтами и гайками;
- Чтобы при вытягивании металлическое изделие не выскакивало из станка, снизу и сверху к тискам прикреплены пластины;
- Двутавровая балка с другой стороны с роликами, на которые впоследствии устанавливается платформа;
- К поверхности полученной конструкции прикрепляют другие тиски с подвижными основными элементами.При этом обе конструкции, расположенные по краям двутавра, должны располагаться на одном уровне;
- Далее конструкция оснащена стальной ручкой из стержня; за счет его вращения изделие будет гнуться;
- Соедините болтами редуктор и двигатель. Обод колеса снабжен цепью;
- Конструкция закрыта стальным кожухом.
В результате проведенных действий получается станок с двумя блоками — подвижным и неподвижным.
Любой мастер, обустраивая домашнюю кузницу, приобретает минимальный набор инструментов и аксессуаров. Но, как правило, простейшие технологические операции с металлическими заготовками производятся только на первом этапе.
С приобретением опыта работы с «железом» появляется и желание, и необходимость заниматься художественной ковкой — это и украшение дома, и дополнительный заработок. К сожалению, улитки-машинки для формования образцов в продаже практически нет. Так или иначе, но домашние мастера, как правило, изготавливают его своими руками.Особенности самостоятельной конструкции и сборки улитки для холодной ковки — тема данной статьи.
Характеристики улитки
Автор специально решил обратить внимание читателя на ряд моментов. Это поможет избежать ошибок в будущем. Например, разобравшись в устройстве улитки и принципе ее функционирования, кто-то захочет собрать собственное устройство, отличное от тех, чертежи которого будут представлены ниже.
Такой прибор вполне себе (если говорить об оборудовании, сделанном вручную), он позволит изгибать образцы с поперечным сечением (стороной квадрата) не более 10 — 12 мм.Имеется в виду «ручная» модель улитки. Практически никто не имеет дела с более крупными образцами в повседневной жизни. Машину также можно улучшить, установив привод и электродвигатель.
Но насколько это рационально для небольшой домашней кузницы?
- Холодная штамповка выполняется на малых скоростях. Резкое изменение геометрии металла приводит к появлению трещин (разрывов).
- Вам нужно будет выбрать не только мощность электродвигателя, но и передаточное число коробки передач.Плюс к этому — смонтировать схему автоматики с установкой соответствующих элементов (кнопки, стартер и так далее). Все это существенно усложняет изготовление станка.
Вывод — для домашней кузницы достаточно улитки, с помощью которой можно гнуть изделия из металла вручную. Любой, кто разбирается во всех нюансах его конструкции и разбирается хоть что-то в электротехнике, может самостоятельно установить на него электропривод.
Делаем улитку
На рисунке показано несколько устройств.Примерно так (в основе) должно работать.
Сборка улитки своими руками — один из вариантов самостоятельного проектирования, когда давать рекомендации с указанием точных параметров всех комплектующих не имеет смысла. Здесь нужно ориентироваться на собственное представление о том, что и как будет гнуться (радиусы, количество витков спирали и так далее). Но если станет ясна суть процесса изготовления, то сама сборка затруднений не вызовет.
Настольное устройство
Процесс холодной штамповки требует больших усилий. Если у вас уже есть готовый верстак, возможно, вам потребуется его усилить. При изготовлении улитки с нуля каркас стола делается только из металла — швеллер, уголок, толстостенная труба.
Понятно, что столешница тоже должна быть металлической. В процессе эксплуатации улитка будет подвергаться как статическим, так и динамическим нагрузкам. Поэтому обычный железный лист не подходит.Только пластина, и не менее 4 мм.
Макет и установка «насадок»
Пожалуй, самый творческий этап работы. Все можно сделать своими руками. Но как с учетом перспектив или ограничиться выпуском однотипных образцов?
Вариант 1. Самый простой. Суть операции в том, что на столешнице рисуется контур спирали.
По сути, это набросок будущих фигурных деталей, например, из бруса.После этого достаточно вырезать из толстой полосы железа, согнутой по радиусу, несколько отрезков. Их приваривают к столешнице, и механизм гибки в основном готов.
Кому-то такое исполнение покажется более привлекательным — с цельной полосой.
Но практика показывает, что с такой улиткой труднее работать. Например, при снятии с него готового изделия возникнут определенные трудности.
Вариант 2. То же, но нарисовано несколько контуров.Вдоль каждого просверливаются отверстия, в которых нарезаются резьбы. Осталось только подготовить шаблоны для отрезков остановки. Их делают своими руками, как правило, из плотного картона или фанеры.
На них делаются накладки из металла, в которых после очередной разметки также просверливаются отверстия, совпадающие с посадочными «гнездами» в плите. Такая конструкция позволит организовать производство спиральных заготовок разного радиуса на одном столе. Необходимо только, в зависимости от формы изгиба, установить соответствующие сегменты в определенных местах.Их крепление к основанию — болтовое. Вы можете действовать по-другому. Вместо таких упоров ставьте цилиндрические.
Для фиксации они притягиваются болтами (снизу пластины) или изготавливаются сразу с ножками (+ резьба) и вкручиваются в столешницу. С ними намного удобнее. А если есть, то вырезать своими руками — дело пары часов.
Вариант 3. Подготовьте несколько съемных модулей, которые можно менять по мере необходимости.
Сборка улитки
Установлен лемех, прикреплены рычаги, боковой упор. Все это хорошо видно на рисунках.
Будет использовано все, что есть в сарае (гараж, чердак) — обрезные трубы, брус, угол и т. Д. Если вы понимаете, как работает улитка, то подсказки больше не нужны.
Функциональная проверка
Это всегда подразумевается, поэтому без комментариев.
В принципе сделать улитку для холодной ковки не так уж и сложно.Тем более, что на такие устройства нет единого стандарта. Кто-то скажет — не проще ли купить заводскую модель? Во-первых, как уже было сказано, придется долго искать. Во-вторых, не факт, что его возможности совпадут с фантазиями мастера. В-третьих, облегчить кошелек придется как минимум примерно на 19 000 (ручная) и 62 000 (электрическая модель) рублей.
Удачи в изготовлении улитки своими руками!
Руководство по типам ковки — холодная штамповка и горячая штамповка
Горячая штамповка и холодная штамповка — это два разных процесса обработки металлов давлением, дающие схожие результаты.Ковка — это процесс деформирования металла до заданной формы с использованием определенных инструментов и оборудования — деформация выполняется с использованием процессов горячей, холодной или даже горячей ковки. В конечном итоге производитель будет рассматривать ряд критериев, прежде чем выбрать, какой тип ковки лучше всего подходит для конкретного применения. Ковка используется там, где расположение зернистой структуры придает детали направляющие свойства, выравнивая зерно так, чтобы оно выдерживало самое высокое напряжение, с которым может столкнуться деталь.Для сравнения, литье и механическая обработка обычно имеют меньший контроль над расположением зернистой структуры.
Ковочные процессы
Ковка определяется как формовка или деформирование металла в твердом состоянии. Большая часть ковки осуществляется в процессе осадки, когда молот или плунжер перемещаются горизонтально, чтобы прижаться к концу стержня или стержня, чтобы расшириться и изменить форму конца. Деталь обычно проходит через последовательные станции, прежде чем достигнет своей окончательной формы. Таким образом, высокопрочные болты имеют «холодную головку».Клапаны двигателя также сформированы высаженной поковкой.
При штамповке методом капельной ковки деталь выковывается в штампе в соответствии с формой готовых деталей, что очень похоже на кузнечную ковку с открытым штампом, когда металл забивается молотком по наковальне для придания желаемой формы. Различают ковку в открытых и закрытых штампах. При открытой штамповке металл никогда полностью не ограничивается штампом. В закрытом штампе или штампе ковка металла ограничена между половинами штампа. Повторяющиеся удары молотка по матрице заставляют металл принимать форму матрицы, и в конечном итоге половинки матрицы встречаются.Энергия для молота может подаваться паром или пневматически, механически или гидравлически. При истинной ковке с падением только сила тяжести толкает молот вниз, но многие системы используют усилитель мощности в сочетании с силой тяжести. Молоток наносит серию относительно высокоскоростных ударов небольшой силы, чтобы закрыть матрицу.
При ковке на прессе высокое давление заменяется высокой скоростью, и половины штампа закрываются за один ход, обычно обеспечиваемый силовым винтом или гидроцилиндрами. Молотковая ковка часто используется для производства небольших объемов деталей, в то время как ковка на прессе обычно предназначена для больших тиражей и автоматизации.Медленное применение ковки на прессе имеет тенденцию обрабатывать внутреннюю часть детали лучше, чем удар молотком, и часто применяется к большим высококачественным деталям (например, титановым переборкам самолетов). Другие специализированные методы ковки различаются по этим основным темам: обоймы подшипников и большие зубчатые колеса изготавливаются с помощью процесса, называемого, например, ковкой катаного кольца, при котором производятся бесшовные круглые детали.
Горячая штамповка
При горячей штамповке кусок металла должен быть значительно нагрет. Средняя температура ковки, необходимая для горячей штамповки различных металлов:
Во время горячей ковки заготовку или блюм нагревают либо индуктивно, либо в кузнечной печи или печи до температуры выше точки рекристаллизации металла.Этот вид экстремального нагрева необходим для предотвращения деформационного упрочнения металла во время деформации. Поскольку металл находится в пластичном состоянии, можно изготавливать довольно сложные формы. Металл остается пластичным и податливым.
Для ковки некоторых металлов, таких как суперсплавы, используется метод горячей ковки, называемый изотермической ковкой. Здесь штамп нагревается примерно до температуры заготовки, чтобы избежать охлаждения поверхности детали во время ковки. Ковка также иногда выполняется в контролируемой атмосфере, чтобы минимизировать образование накипи.
Традиционно производители выбирают горячую ковку для изготовления деталей, поскольку она позволяет деформировать материал в его пластическом состоянии, при котором с металлом легче работать. Горячая ковка также рекомендуется для деформации металла с высоким коэффициентом деформируемости — мерой того, какой степени деформации металл может претерпеть без развития дефектов. Другие рекомендации по горячей штамповке включают:
- Производство отдельных деталей
- Точность от низкой до средней
- Низкие напряжения или низкое деформационное упрочнение
- Гомогенизированная зернистость
- Повышенная пластичность
- Устранение химических несоответствий и пористости
К числу возможных недостатков горячей штамповки можно отнести:
- Менее точные допуски
- Возможное коробление материала в процессе охлаждения
- Различная структура зерна металла
- Возможные реакции между окружающей атмосферой и металлом (образование накипи)
Холодная штамповка (или холодная штамповка)
Холодная штамповка деформирует металл, когда он находится ниже точки рекристаллизации.Холодная ковка несколько увеличивает предел прочности на разрыв и существенно снижает пластичность. Холодная ковка обычно происходит при комнатной температуре. Наиболее распространенными металлами при холодной ковке обычно являются стандартные стали или углеродистые легированные стали. Холодная штамповка обычно представляет собой процесс с закрытой штамповкой.
Холодная ковка обычно предпочтительна, если металл уже является мягким, например, алюминием. Этот процесс обычно менее затратен, чем горячая штамповка, и конечный продукт требует небольших отделочных работ, если они вообще требуются.Иногда при холодной штамповке металла до желаемой формы его подвергают термообработке для снятия остаточных поверхностных напряжений. Из-за улучшений, которые холодная ковка вносит в прочность металла, иногда могут использоваться материалы меньших сортов для производства обслуживаемых деталей, которые не могут быть изготовлены из того же материала механической обработкой или горячей штамповкой.
Производители могут предпочесть холодную штамповку горячей штамповке по ряду причин — поскольку холодные штампованные детали требуют очень мало или совсем не требуют отделочной обработки, этот этап процесса изготовления часто является необязательным, что позволяет сэкономить деньги.Холодная ковка также менее подвержена проблемам загрязнения, а конечный компонент имеет лучшую общую поверхность. Другие преимущества холодной ковки:
- Проще придать свойства направленности
- Повышенная воспроизводимость
- Повышенный размерный контроль
- Выдерживает высокие нагрузки и высокие нагрузки на матрицу
- Производит детали чистой или почти чистой формы
Некоторые возможные недостатки включают:
- Перед ковкой металлические поверхности должны быть чистыми и свободными от окалины
- Металл менее пластичный
- Возможно остаточное напряжение
- Требуется более тяжелое и мощное оборудование
- Требуется более прочный инструмент
Теплая поковка
Горячая ковка происходит при температуре ниже температуры рекристаллизации, но выше комнатной температуры, чтобы преодолеть недостатки и получить преимущества как горячей, так и холодной ковки.Образование окалины представляет меньшую проблему, и допуски могут быть соблюдены ближе, чем при горячей ковке. Затраты на инструмент меньше, и для производства требуются меньшие усилия по сравнению с холодной штамповкой. Уменьшается деформационное упрочнение и улучшается пластичность по сравнению с холодной обработкой.
Приложения
В автомобильной промышленности ковка используется для изготовления компонентов подвески, таких как натяжные рычаги и шпиндели колес, а также компонентов трансмиссии, таких как шатуны и шестерни трансмиссии.Поковки часто используются для стержней, корпусов и фланцев трубопроводной арматуры, иногда из медного сплава для повышения коррозионной стойкости. Ручные инструменты, такие как гаечные ключи, обычно кованые, как и многие детали для троса, такие как розетки и талрепы. Поковки широко используются в судостроении, авиакосмических компонентах, в сельскохозяйственной технике и внедорожной технике. В компонентах электропередачи, таких как зажимы подвески и крышки опор, используются поковки из медного сплава для повышения устойчивости к атмосферным воздействиям.
Ковочные стали, используемые для осей, шатунов, пальцев и т. Д., Обычно содержат 0,30–0,40% углерода для повышения формуемости. Термическая обработка после ковки позволяет деталям развивать лучшие механические свойства, чем у низкоуглеродистой стали. В тяжелых коленчатых валах и высокопрочных зубчатых передачах иногда повышают содержание углерода до 0,50% с добавлением других легирующих элементов для улучшения прокаливаемости.
Сводка
В этой статье кратко обсуждается горячая и холодная штамповка.Для получения дополнительной информации о других продуктах обратитесь к другим нашим руководствам или посетите платформу Thomas Supplier Discovery Platform, чтобы найти потенциальные источники поставок или просмотреть подробную информацию о конкретных продуктах. Дополнительную информацию о процессах ковки можно найти на веб-сайте Ассоциации кузнечной промышленности.
Прочие изделия из металла
Прочие «виды» изделий
Больше от Custom Manufacturing & Fabricating
приспособлений для прокрутки — Инструменты, общее обсуждение
Я уже делаю слишком много листьев! Листья на стержнях для бумажных полотенец, листья на стержнях туалетной бумаги, листья на стержнях для полотенец, листья на костре…… я понял! Не поймите меня неправильно, мне нравятся листья, и я думаю, что у меня есть отличный метод их изготовления (если я сам так говорю), но моя будка становится слишком похожей на лес!У меня есть несколько идей, которые я попытаюсь выбить из последнего ведра угля, которое у меня есть … Я дам вам знать, как это происходит!
Привет, Дэйв! Если ты собираешься купить эти или похожие предметы, давай на газ, ты не сможешь угнаться за собой, Сужайся и сначала прокручивай прокрутку до конца (ты должен указывать на нее, это было бы по-прежнему выглядит круто, как конец ленты) затем вы можете согнуть углы в холодном состоянии с помощью гаечных ключей,
На этом изображении показан держатель для стакана, который можно втыкать в землю, но он даст вам представление о том, как будет выглядеть свиток на конце ленты например, вместе с использованием спиральных гаечных ключей / вилок для гибки
Или пары простых губок, установленных в зазоре, подходящем для металла, затем поворотную ручку / рычаг с шарниром, примыкающим к задней направляющей / губке, и потяните до установленный угол также подойдет
Еще один метод сгибания стержня в холодном состоянии — это иметь пластину с тремя штифтами, стратегически расположенную в треугольной конфигурации для получения требуемой формы, и ручку, которая может опускаться над штифтами, чтобы использовать гибочный рычаг
Рукоятка для просверливания отверстия e конец, и штифт, приваренный так, чтобы расстояние от края отверстия до края штифта было немного больше диаметра стержня, который вы используете,
Поместите свой прокрученный конец до первого штифта, который будет действовать как ограничитель длины до первого изгиба,
Опустите ручку на первый штифт вдоль и потяните, чтобы привести штангу в соприкосновение со следующим штифтом
Снимите ручку и установите на место следующий штифт, снова потяните до тех пор, пока свободный конец не окажется внутри положение регулируется (вы можете вставить здесь стопорный штифт)
Если это не понравится, я уверен, что вы найдете что-то подходящее Отредактировано автор John B
Техника зимней джиггинга для каякеров — Джефф Литтл рассказывает, как распознать тяжелые поклевки на джиг
Терпение — не клише, когда дело касается зимней джиговой рыбы.Не торопитесь и следуя правильной технике зимней джиггинга, вы сможете добыть самую крупную рыбу года. Фото Джефф ЛиттлДжефф Литтл
Все любят мощное удилище, вырвавшее удилище из рук, сокрушительное джиг-хит. Держите линию натянутой, сосредоточьтесь на презентации, и у вас обычно не возникает проблем с ощущением укуса. Однако по мере того, как температура воды падает к югу от 40 градусов, эти удары по костям, кажется, исчезают.
Вместо этого леска просто становится мягкой, или, если вам повезет, леска смещается в сторону, давая вам понять, что пора закопать крючок.Честно говоря, большинство рыболовов никогда не чувствуют ударов и после похода без рыбы предполагают, что окунь просто не клюет в холодной воде. Зимняя поклевка на джигу — сложнее всего, но те, у кого есть подходящее снаряжение и хорошее настроение, могут справиться с ней и даже поймать своего самого большого окуня в году. Вот как это сделать:
Механика передачи вибрации вверх по леске
Прежде всего, любое отклонение от идеально прямой линии от джига до конца удилища — ваш враг. Ветер изгибает вашу линию.Current делает то же самое. Забросьте ветку, и этот тупой угол практически уничтожит все ваши шансы почувствовать укус. Чем длиннее ваш заброс, тем больше вероятность того, что что-то натянет ваш лук на леску.
Прошлой зимой, ловя рыбу в водоеме на корню, я стал больше ценить короткие забросы. Мой обычный промысел — река с небольшим устьем, которая редко бывает глубже 12 футов, — требует более длительных забросов, чтобы быть незаметным. Но для глубокого резервуара требовался другой набор углов.Я узнал, что совершать длинный заброс, накинувшись на множество старых стоящих под водой деревьев в 30 футах воды, равносильно отсутствию укусов. Пришлось расположиться над ними и выполнить джиг почти вертикально. Забросы, при которых ловилась рыба, были короткими, потому что я мог чувствовать поклевку на вертикально прямой натянутой леске. Зимой нужны как большие, так и маленькие джиговые приманки. Делайте большие, когда ловите рыбу на глубине и в плотном укрытии, и делайте маленькие, когда укрытие для рыбалки не является проблемой, но получить клев. Photo Jeff Little
Один из способов, чтобы леска оставалась как можно более прямой, при этом удерживая приспособление в неподвижном состоянии, — это привязать более тяжелое приспособление.В ветреные дни, когда я ловлю рыбу в водохранилище, я использую 3/8 унции до 1/2 унции. На реке, когда поток усиливается, я прыгаю с 1/8 унции до 1/4 или 3/8 унции. Ловлю воду на глубине более 30 футов на водохранилище с стоящей древесиной, и я пойду до джига на 1 унцию. Соедините эти тяжелые веса с короткими забросами, и мягкий кусочек станет четким.
Еще одна переменная, требующая внимания, — это дрейф вашего каяка. Когда мы видим вероятную цель, мы приближаемся к ней и делаем заброс.Важнейший шаг, который упускают из виду многие рыболовы на каяках, — это остановка поступательного движения. Если ваша каяк все еще движется в том направлении, в котором вы только что сделали заброс, на вашей леске всегда будет лук, чтобы вы не почувствовали поклевку во время или вскоре после первого спуска с джига. Выберите свою цель, двигайтесь к ней, отбейте гребешок от нее, чтобы убить вашу инерцию, а затем сделайте бросок. Этот медленный обратный дрейф будет поддерживать постоянное натяжение вашей лески.
Правильная удочка может дать вам преимущество, но для этого нужно учитывать такие факторы, как правильный вес джиг-приманки, углы заброса и простота нахождения в точке, готовой к установке крючка в любое время.Удилище, которое я использую, соответствует весу ловушки, которую я забрасываю. Все мои джиг-удилища либо быстрые, либо сверхбыстрые. Это помогает эффективно загнать крючок в исходное положение.
Леска должна быть как можно более низкой, чтобы почувствовать разницу между тем, как ваша джиг врезается в следующий камень на своем пути, и когда джиг бьет крышу по рту. Меньше всего тянется плетеная леска, затем фторуглерод, затем сополимеры и моноволокно.
Увеличьте время удержания приманки
Увеличив вес приманки, вы почувствуете больше поклевок, но компромисс в том, что они не будут удерживать приманку так долго.Добавьте мягкий пластиковый трейлер, и они продержат его немного дольше. Намажьте джигу ароматом, и окно возможности установить крючок значительно расширится. Удержание приманки также зависит от давления на рыбу. Если их ловили много раз, они настроены более скептически, поэтому вам лучше быть на месте, когда они попадут в интенсивно выловленные воды.
Если вы считаете, что поклевки слишком тонкие, чтобы вы когда-либо почувствовали их, попробуйте использовать крючок из тонкой проволоки. Это была тактика, которую я использовал в течение многих лет в зимнем устье реки с температурой воды ниже 30 градусов.Но он никогда не полетел бы на тех стоячих лесных водоемах большеротых. Они выпрямляли крюк задолго до того, как я вытаскивал их из лабиринта затопленного дерева.
На одном конце диапазона размеров находится приспособление для щетки с толстым, но острым откидным крючком 5/0 и защитой от щетины. На другом конце находится микротрубка, закрепленная на джиг-головке на 1/8 унции с крючком размера 2, который вонзается в плоть, как только касается ее. Для одного требуется мощный набор крючков с полным поворотом, а для другого крючки ловят рыбу, которая просто заглатывает приманку и поворачивается, устанавливая крючок на себя.Один идет в самые глубокие и густые джунгли из бревен, а другой достаточно легкий, чтобы катиться по дну реки и не зацепиться. Если у вас не так много укрытий, подумайте о том, чтобы использовать крючок как можно более тонкого диаметра. Зимой речной малоротый окунь лучше всего ловить на тонкие проволочные крючки, которые настолько липкие, что и сам рыболовный крючок. Фото Джефф Литтл
Получите свою голову прямо
Сосредоточение внимания на каком-то событии, которое, как вы надеетесь, произойдет, но не прошло в течение нескольких часов, оставляет дверь открытой для мучительных сомнений: «Я нахожусь в правильном месте?» «Стоит ли мне идти к первой точке, где я поймал одну четыре часа назад?» «Может, мне нужно сменить цвета.«Выпить чашку горячего кофе прямо сейчас — лучше, чем сидеть здесь и не кусаться!» У всех рыболовов время от времени случаются спады, и начинаются они с подобных мыслей. Негатив и неуверенность необходимо активно устранять с помощью визуализации и позитивного психологического отношения.
Визуализация идет рука об руку с позитивным умственным настроем. Это сфабрикованное укрепление доверия, и оно работает. Попробуйте в следующий раз, когда будете забрасывать джигу. Сделайте короткий заброс, закройте глаза и медленно проведите джигом по дну.Попробуйте угадать нижнюю подложку. Это кусок камня, гравий, песок или куча разлагающихся листьев? Теперь подойдите к месту и посмотрите, были ли вы правы. Вы правильно угадали?
Теперь перейдите на следующий уровень. Если вы проделали это несколько раз, то поймете, как должно выглядеть дно. Представьте, что ваша джига медленно волочится по нижнему субстрату. Затем представьте, что рыба увидела, как джиг плескался и спускался на дно. Вода холодная, поэтому из-за замедленного метаболизма большому окуну потребуется время, чтобы ее исследовать.Она пропускает приспособление на изнаночную сторону бревна и еще не видит его. Вы снимаете джигу с черной юбкой весом 1 унцию с камня, на котором она опирается, и она подпрыгивает на небольшое расстояние, врезаясь в следующий камень. Шум столкновения привлекает внимание рыбы, и она вспыхивает грудными плавниками, чтобы повернуться и изменить направление. Ароматный след проходит в двух футах от нее. Она ловит его, отслеживает до приманки и поворачивает свой рот к приманке. Юбка джига распахнулась, как цветок на солнце.Отдельные пряди юбки дрожат от воды, стекающей с плеч парящего в нескольких сантиметрах от большого окуня. В момент, слишком короткий, чтобы это могло произойти, она раздувает свои жабры и засасывает тяжелую джигу в рот. Четкая вибрация проходит по 25-фунтовой фторуглеродной леске к наконечнику удилища.
Чувствовали ли вы это, или вас отвлекали мысли об изменении цвета джига или уходе за чашкой горячего кофе? Если вы визуализируете последовательность событий, которые должны произойти, вы будете на месте, чтобы установить крючок, когда дело пойдет не так.Кстати, по вопросу о цвете кондуктора черный всегда работает. Бросьте черный и тихий этот мысленный шум.
Каково это, когда они бьют?
Как новичок в зимней речной малоротой рыбалке много сезонов назад, я задал этот вопрос. С тех пор мне много раз задавали тот же вопрос. Описания ощущений варьируются от «тик» до «стук», «пульсация» и «смешно». В процессе обучения познанию того, что это такое, есть много разочаровывающих моментов осознания того, что странный колчан, который вы почувствовали мгновение назад и не поставили на крючок, действительно был рыбой.Временами это просто сводит с ума.
Мои советы начинающим зимним рыболовам с годами менялись. Я имел обыкновение перечислять все различные ощущения и вибрации, которые могли бы пройти по вашей линии. Многим из моих учеников это не принесло особой пользы. Это сбивает с толку. Последующий совет: «Со временем вы поймете, на воде», тоже не очень удовлетворил. Прорывный совет на самом деле был противоположным вопросом: «Каково это, когда они бьют?» Вместо того, чтобы задавать этот вопрос, спросите себя: «Что чувствует дно, когда они не бьют?»
Сосредоточение внимания на том статическом жестком давлении, которое вы ощущаете, удерживая кончик удилища, натянутую леску и неподвижно сидящую на дне джигу, — это именно то, как вы понимаете, «каково это, когда они ударяют».Сосредоточьтесь на ритме толчков и скрежетов джига, протаскиваемого по дну. Знайте, что такое «нормальное» ощущение, когда джиг лежит на нижней подложке или ее тащат по ней. Резкое отсутствие этого «нормального» часто является единственным признаком того, что приманка находится во рту рыбы. Крючки бесплатны, и если вы ждете этого фирменного «удара», вы легко упустите 80% своих шансов нацепить рыбу этой зимой.
Как медленно я должен ловить джиг-приманку?
Несмотря на то, что рыболовы обычно называют терпеливыми, мы им не являемся.Большинство из нас явно недостаточно терпеливы, когда дело касается того, насколько медленно нам нужно ловить джиг зимой. Вот способ понять необходимую презентацию джиг-приманки в 34-градусной воде. Переверните камни и найдите раков. Как только вы это сделаете, вы можете подумать, что он мертв. Он не сможет быстро развернуть хвост, чтобы убежать. Он вообще не сдвинется с места, пока вы не поместите его в другое место. Переместите его на мелкую гравийную площадку, сядьте рядом и отметьте время. Через пять минут измерьте, сколько земли он покрыл.Я записал медленное движение речных раков Саскуэханна в феврале для своего DVD на тему Winter River Smallmouth Patterns. Раки, вытащенные из воды с температурой 34 градуса, действительно двигались, но расстояние, которое они преодолели за время, которое я потратил на рассказ, было меньше 3 дюймов.
Итак, если ваша джиг прыгает, как попкорн, насколько вероятно, что рыба поверит, что то, что они видят, является раком? Движение, которое имеют настоящие раки, очень тонкое. Животное может не продвигаться в нужном положении, но усики раскачиваются, лапы медленно раскачиваются, а когти очень медленно колеблются на месте.Джиг с короткой юбкой, особенно с круглым резиновым корпусом, смешанным с юбкой, который сидит на одном месте, идеально имитирует это.
Но то, что я говорю вам, как медленно вам нужно ловить рыбу, не придаст вам уверенности, необходимой для того, чтобы просто позволить рыбе сидеть здесь несколько минут за раз. В этом вас убедит только время, проведенное на воде с последующей ловлей рыбы в конце 10-минутной паузы. Имейте веру, и если у вас еще нет этого, заставьте его отсчитывать или установить секундомер на две минуты, прежде чем вы сможете даже перевернуть джигу еще на три дюйма к следующему месту, и вы дадите ему отдохнуть еще две минуты.
Успешная зимняя ловля на джиг — значит иметь правильные снасти. Это означает, что вы можете сохранять концентрацию и держать голову в хорошем состоянии, пока ничего не происходит. Но за его освоение есть награды, выходящие далеко за рамки зимнего сезона. Вы разовьете набор навыков обнаружения ударов, которые сделают вас лучшим рыболовом на джигу в любое время года. Когда, наконец, наступает удар, нет ничего лучше, даже если на улице так холодно, что вы потеряли чувствительность в пальцах ног.
Статья изначально была опубликована на Kayak Fish
Чтобы получить доступ к эксклюзивным видео о снаряжении, интервью со знаменитостями и многому другому, подпишитесь на YouTube!
Цех по производству ступиц колес — Холодная штамповка, ЧПУ и культура завода по производству велосипедных компонентов
Производство компонентов для велосипедов — это то место, где начинается путь к созданию велосипеда в сборе.Бренд может собирать единицы, которые в конечном итоге катятся по шоссе и проселочным дорогам. Но сердце и душа велосипеда выкованы в мастерских, разбросанных по ландшафту, от Тайнаня на юге до Тайбэя на севере.
Таким образом, этот пост является первым из двух иллюстрированных статей, дающих представление о большей части того, что происходит в мастерской производителя ступиц округа Тайчжун. Компания, о работе которой я рассказываю здесь, в течение довольно долгого времени занимала себе рыночное пространство, производя высокопроизводительные концентраторы.Скорее всего, там были изготовлены ступицы на вашей собственной колесной базе.
В этом первом посте я рассмотрю создание оболочки концентратора. Следующий будет посвящен сборке ступицы и позволит проверить очень интересную ступицу, результат недавнего сотрудничества ODM между производителем ступицы и европейским клиентом.
Больше, чем просто описание технических процессов, этот пост посвящен идее, о которой я хочу начать говорить, о чем я еще вернусь в будущем, обсуждая другие вещи: взаимосвязь серийно производимых или обрабатываемых деталей или компонентов. на изделия ручной работы / ручной работы.
То, над чем я размышлял уже некоторое время, в последнее время это стало немного более предметным. Если вы еще этого не сделали, я рекомендую послушать выступление Иэна Боала в Копенгагенском музее, записанное Copenhagenize.com. В нем он обрисовывает некоторые идеи, входящие в его книгу The Green Machine (которая скоро будет опубликована) (это еще не все, что вы думаете — у «зеленой машины» не такая уж зеленая история).
Один из многих важных моментов, которые он сделал в этом замечательном выступлении, касается того, на что ему потребовались десятилетия.«Великий разрыв» в истории велоспорта произошел между кузнецом как мастером-одиночкой и культурой фабрики. «Культура Смита и новая культура фабрики» с ее «взаимозаменяемыми частями, точными допусками, новым образом мышления».
В истории производства велосипедов, последовавшей за этим культурным изменением, наряду с этим была также культура отдельных мастеров (Бианки, Кольнаго, Пегоретти и многие другие). Проведя так много времени на заводах по производству компонентов, я задаюсь вопросом, насколько далеки друг от друга культуры фабрики и ремесленника-одиночки.
Холодная штамповка или ЧПУ? (Формирование процессов для энтузиастов и энтузиастов / профессионалов). Для крупных производств лучше всего подходит холодная штамповка с более низкой стоимостью единицы продукции по сравнению с ЧПУ.
Холодная кузница
Пресс холодной штамповки. Оператор обрабатывает партию сплавов ступиц-оболочек. Оболочка в фокусе здесь — средняя картинка, верхняя треть.
Ступица обрабатывается в два движения. Здесь оператор готовится ко второму прессу. Сжатие Несколько секунд, два движения — рождается ступица-оболочкаМешок ступиц:
Результат холодной ковки за один сеансКорпус формируется в соответствии с применяемым приспособлением.На все случаи жизни найдется приспособление. Или, в любом случае, может быть приспособлением для любого случая.
Станки для холодной штамповки с корпусом ступицыCNC
Отсюда мы направляемся в секцию ЧПУ.
Участок обработки с ЧПУКорпус ступицы перед входом в станок:
Корпус ступицы перед обработкойПосле обработки он утоплен. Это когда нити обрезаются.
Обработка оболочки ступицы на станке с ЧПУ Панель управления оператораОчистка при подготовке к установке другой оболочки ступицы.
Очистка Готово Удаление корпуса ступицыдо:
Дои после. . .
ПослеИли как насчет этого. Какая трансформация от этого. . .
Сырье до. . . на это:
Замечательная трансформацияСледующая особенно интересна. Оболочка ступицы, изначально состоящая из 3 отдельных частей, превращается в одну.
Обработано 3 штуки. . … . в одинПервоначальная концепция заключалась в том, что обработка 3 в 1 будет дешевле, чем резка «неотрезанного блока».На самом деле оказалось так же. Поэтому заказчик решил вернуться к простой обработке «неотрезанного блока» из-за отсутствия технической или коммерческой выгоды от этой стратегии.
Основная проблема здесь в том, что обработка небольшого количества на ЧПУ дешевле, чем холодная штамповка. ЧПУ дороже в расчете на единицу, но рентабельно, если у вас небольшое количество. Чтобы пойти по пути холодной штамповки, вам необходимо иметь собственное приспособление (что создает проблему амортизации) для конкретной формы или конструкции ступицы, которую вы хотите.Вы можете получить желаемый дизайн с помощью акробатического станка с ЧПУ.
Еще одним важным процессом является добавление отверстий для спиц в корпус ступицы. Есть две машины, на каждой по оператору.
Дырокол для спиц Оператор №2Отверстия добавлены сверху; корпус ступицы удерживается на месте внизу. И вот результат.
BeforeAfterЕсли вы внимательно посмотрите на это, вы увидите «замочные скважины», а не круглые отверстия. Они выполняются снаружи, а не на месте.
Лоток со ступицами для сборочного цехаПоследние мысли
Итак, это краткий обзор основных процессов, лежащих в основе производства корпусов ступиц в колесной паре вашего велосипеда.
Компоненты велосипеда изготавливаются специалистами. Многие из них являются специалистами благодаря имеющимся в их распоряжении точным машинам и инструментам, например, те немногие, работу которых мы рассмотрели выше. Другие привносят более высокий уровень мастерства в изделия, которые они создают, что мы увидим в сборочном цехе в продолжение этого поста.
Другие по-прежнему, особенно при нанесении декалей в малярной мастерской, демонстрируют чрезвычайно высокий уровень мастерства. Это также видно по индивидуальному вниманию, которое уделяется каждой рамке на фабрике производителя рам.
По сути, я считаю, что если внимательно присмотреться к разнообразным рукам и разнообразным процессам, которые приводят к завершенному функционированию велосипеда, любая граница между индивидуальным ремесленным производством ручной работы и массовым производством для массового рынка становится менее четкой. Как я упоминал ранее, я еще вернусь к этому.
Что касается описанного здесь производства ступиц, то как только это будет сделано, оно будет отправлено на сборочную линию, о которой будет рассказано в будущем фото-посте.
ДОМАШНЯЯ КЛИНИКА; «ПРИГОТОВЛЕНИЕ» И ДРУГИЕ СПОСОБЫ ПРИВЕДЕНИЯ ДРЕВЕСИНЫ ИЗГИБНОЙ ФОРМЫ
Единственный способ определить расстояние между пропилами или пропилами и глубину каждого пропила — это заранее поэкспериментировать с некоторыми кусками той же древесины.Как правило, пропилы должны проходить от половины до трех четвертей пути сквозь панель или доску и должны располагаться на расстоянии примерно от четверти дюйма до целого дюйма, в зависимости от толщины древесины и толщины древесины. радиус изгиба. Чем круче изгиб, тем теснее и уже должны быть пропилы.
Для выбора правильной комбинации может потребоваться несколько тестов. В идеале пропилы должны быть расположены так, чтобы деталь плавно изгибалась при сгибании, и они должны быть достаточно глубокими и достаточно широкими, чтобы каждый пропил закрывался на поверхности, когда деталь полностью согнута в нужное положение.
Чтобы создать отдельно стоящий изогнутый кусок фанеры, который не будет опираться на основу или каркас, вы можете склеить несколько тонких листов вместе, чтобы получить необходимую толщину, изгибая их по ходу движения.
Это делается путем сборки временной гибочной формы. К нему зажимается первый тонкий лист и покрывается клеем; затем сверху зажимается второй тонкий лист. Это продолжается с последовательными листами, каждый из которых приклеивается к предыдущему и зажимается в изогнутой изогнутой форме, чтобы удерживать его на месте.
Когда клей высохнет, изогнутую панель можно вынуть из формы, и она сохранит свою форму.
Ответ на почту
В. В потолке нашей гостиной есть трещина, которая проходит по всей длине комнаты (18 футов) и простирается до верхней части оконной рамы. Трещина была залита шпаклевочной массой, но она расшаталась и выпала, так что теперь трещина снова открыта. Есть ли лучшее средство? — F.N., Danbury, Conn.
A. Для действительно устойчивых трещин, которые продолжают открываться, лучше всего подходит один из герметиков, предназначенный для использования со специальной лентой из стекловолокна.В отличие от штукатурки и обычных шпаклевочных составов, эти составы не сильно сохнут; они остаются немного гибкими, и при нанесении в соответствии с указаниями на упаковке они предназначены для перекрытия трещины, а не ее заполнения. Таким образом, когда штукатурка расширяется или сжимается, или перемещается из-за структурных «давлений» ямочный материал не будет выдавлен; он также будет «давать» и останется на месте. Вы можете купить эти материалы для ремонта (в виде комплекта или по отдельности) во многих магазинах красок и хозяйственных товаров, а также в домашних центрах.(Krack-Kote и Tuff-patch — две марки, широко доступные в этой области).
Reader Story: Изготовление нестандартной велосипедной рамы дома
Последние пять лет я конструировал свои собственные велосипедные рамы, и больше всего меня спрашивают о процессе. Оказывается, есть много людей, которые всегда хотели попробовать построить фреймворк, но не знают, с чего начать. Итак, когда я собираюсь приступить к другой сборке фрейма, я подумал, что найду время, чтобы задокументировать этот процесс; от дизайна до изготовления.
Раскрытие информации: это действительно не пошаговое руководство, и я ни в коем случае не профессионал. План состоит в том, чтобы просто понять, что нужно для создания собственного каркаса, и, возможно, добавить несколько полезных советов по пути.
Прежде чем мы начнем, вот несколько фотографий рам, которые я делал в прошлом:
МАТЕРИАЛЫ: Что вам понадобится
Я покупаю все свои трубки у Саймона на сайте www.ceeway.com, но есть гораздо больше вариантов (например, Рейнольдс).Я предпочитаю, чтобы все было проще и использую трубки прямого калибра просто потому, что с ними легче работать, и вы также можете получить более длинные трубы — и это намного более рентабельно. Если вы хотите пофантазировать и немного сбросить вес, вы могли бы пойти с набором трубок с двойным баттингом, но двойное баттинг примерно в два раза дороже, чем прямой калибр.
Трубки Columbus Gara изготовлены из стандартной хромомолибденовой стали 4130 и не самый надежный вариант, но, как уже говорилось, с ними легко работать и они экономичны для такого любителя, как я.У меня вышла из строя только одна рама, и это была верхняя труба, где стыковалась косынка, это могло быть связано с небольшим количеством грязи в сварном шве, неисправной трубкой, самой косынкой или многими другими причинами. При этом потребовалось два года гонок по всей Шотландии, и он заработал несколько подиумов, прежде чем отказался от призрака.
Нижняя труба:
Columbus Gara, прямой калибр 35×0,9 мм 4130 из хромированной стали
Верхняя труба:
Columbus 31,8×1,0 мм, прямой калибр 4130 из хрома
Подседельная труба:
Columbus Gara 35×0.9 мм, прямой калибр 4130, хром
Хомут подседельной трубы:
Обработка на заказ, низкоуглеродистая сталь 100x35x2,0 мм (в идеале нержавеющая, но у меня уже было немного мягкой стали)
Цепные перья:
Columbus Gara Прямые перья 19×0,9 мм 4130 из хрома
Сиденья:
Columbus Gara Прямой калибр 16×0,9 мм 4130 из хромированной стали
Корпус нижнего кронштейна:
Английская резьба 40×73 мм низкоуглеродистая сталь
Головная труба:
HT44 110 мм x 44 мм ID 4130 Головная труба из хрома
Отводы:
Обработанная на заказ нержавеющая сталь
Крепления для кабелей:
3 x 170B — двойной кабель Stop
3 x 170A — Одиночный ограничитель троса
6 x 478INOX — Бобышка для бутылок M5 Нержавеющая сталь
6 x 200 — Направляющая троса с застежкой-молнией
КОНСТРУКЦИЯ: CAD не требуется
Материалы отсортированы, пора приступить к проектированию рамы .Я создаю все свои кадры 2D в Adobe Illustrator (по сути, ручка и бумага). Это не лучшая программа для работы, но, поскольку я использую ее ежедневно (графический дизайнер), я ее очень хорошо знаю. В остальном Bikecad — лучший вариант, в нем есть множество замечательных функций, таких как крепление для велосипеда, и встроенный производитель шаблонов колпачков для труб. Однако, как строитель-любитель, я не могу оправдать такую цену.
Начнем с вилки. Эта рама будет 29er и будет оснащена вилкой с ходом 130 мм (2018 Rockshox Recon RL Solo Air со смещением 51 мм).Я лично предпочитаю хардтейл-рамы с вилкой с коротким ходом. Это связано с тем, что чем больше длина хода, тем больше будет изменяться геометрия в течение указанного хода. Я считаю, что это приводит к тому, что ваш вес переносится вперед, вылет эффективно увеличивается, а угол наклона головы увеличивается. Даже с 130-миллиметровой вилкой угол наклона головы и вылет варьируются от 63º / 440 мм до 64,5º / 450 мм между статичностью и провисанием.
Чтобы прочитать более подробную статью о хардтейлах, ходе вилки и геометрии, перейдите в блог BTR здесь.
ГЕОМЕТРИЯ: статическая или прогиб?
Я начинаю с разработки базовой рамы с числами, которые я хочу статичными (без нагрузки), а затем выясняю, какой будет рама с желаемым прогибом, в моем случае 25%. Затем я настраиваю эти числа (округляя в большую или меньшую сторону) и проектирую полный велосипед со всеми деталями. Я считаю, что работа с проседшими числами помогает мне понять, каким будет мотоцикл, когда я на нем буду ездить.
Угол головки: 64,5º
Угол подседельной трубы: 76º
Длина нижнего перья: 428 мм
Падение BB: 70 мм
Вылет: 450 мм
Ось: 148×12 мм Boost
УСТАНОВКА РАМЫ: Купить или построить?
После завершения этапа проектирования рамы мне теперь нужно иметь возможность удерживать трубы под правильным углом.Здесь в игру вступает ваша джиг-приманка. Есть много вариантов для покупки. Инструменты Академии, вероятно, являются одними из самых рентабельных (в конечном итоге я сам получу один). Я решил построить свою собственную из алюминиевого профиля и различных других алюминиевых деталей. Ниже представлен мой дизайн:
Это не самое сложное приспособление, но его можно разбить на более мелкие приспособления для изготовления отдельных частей рамы, например, переднего треугольника. Алюминиевый профиль — это, по сути, большой набор Meccano.Один зажим подходит для крепления каретки к подседельной трубе. Второй крепит нижний кронштейн к рулевой трубе. Я считаю, что использование как можно более коротких секций помогает при выравнивании, так как короткие отрезки помогают уменьшить изгиб экструзии. К сожалению, у меня нет фотографий сборки моей джиг-приманки, поскольку я сделал ее несколько лет назад.
Прежде чем я перейду к сборке, я рисую секции рамы / рамы в каждом приспособлении, так как это помогает как отрезать трубы до нужной длины, так и как можно точнее настраивать приспособление позже.
ИЗГОТОВЛЕНИЕ: меньшие шаги обеспечивают точность
Попытка задокументировать полный процесс изготовления рамы оказалась несколько труднее, чем я ожидал, но я полагаю, что ее можно разбить на пять шагов; Нарезка труб по длине, колпачок / стыковка труб, прихваточная сварка, проверка соосности и чистовая сварка с последующей проверкой соосности.
Я начинаю с соединения подседельной трубы с кареткой, затем строю передний треугольник, а затем нижние перья и перья сиденья.Как только я доволен всем этим, я делаю такие неудобные детали, как направляющие для кабеля, крепление для диска, подвеска заднего механизма и значок на голове …
СОКРАЩЕНИЕ ТРУБЫ: Я использую старый токарный станок
Сглаживание трубы — это наверное, первое, что вам нужно будет освоить, если вы планируете делать свою собственную раму. Есть несколько способов сделать это: опилить вручную (на самом деле не так сложно), использовать токарный станок (я предпочитаю) или фрезерный станок или купить специальный инструмент для надрезания труб. Заполнение бумажных шаблонов вручную — это лучший способ начать.Это помогает использовать онлайн-инструмент, такой как — Калькулятор копировальной трубки Metal geek. (способ показан ниже на странице).
Когда вы только начинаете, лучше всего отрезать несколько отрезков трубок, чтобы попрактиковаться в митре. Это также предоставит вам некоторые практические соединения для последующей сварки. Чтобы увидеть отличное видео, показывающее процесс ручной резки под углом с файлами, посмотрите видео Cobra frames здесь.
У меня есть приспособление, которое я сделал для своего токарного станка, используя трубный блок от Rä Bike, старые вертикальные суппорты, сделанные моим папой много лет назад, и специальную опорную плиту, изготовленную по размеру моего токарного станка.Это позволяет мне быстро и легко настроить пропил с правильным углом и смещением, если это необходимо, но я все еще использую ручные файлы для точной настройки посадки или очистки пропила, если это необходимо.
ПОСТРОЕНИЕ ПЕРЕДНЕГО ТРЕУГОЛЬНИКА: время показа
Построение переднего треугольника — одна из моих любимых частей каркасного строительства. Это довольно просто, и вы можете быстро получить что-то, напоминающее раму велосипеда.
Как упоминалось ранее, я всегда начинаю с соединения подседельной трубы с кареткой.Я считаю, что это самый простой способ убедиться, что подседельная труба правильно выровнена с кареткой. Используя мое приспособление для токарного станка, это простой и довольно быстрый процесс установки угла, выбора фрезы подходящего размера, резки трубы, очистки напильником и загрузки в специальный зажим для bb / подседельной трубы. Отверстие в BB предназначено для того, чтобы вся вода, которая проходит через подседельную трубу, стекала в нижний кронштейн и из рамы, есть также дополнительное преимущество в виде экономии нескольких граммов.Также есть отверстие под всеми соединениями труб, чтобы рама могла дышать, что помогает с конденсацией и снижает давление во время стадии сварки.
Подседельная труба / нижний кронштейн в сборе — это простая отправная точка: вырезание под углом 90 градусов кольцевой пилой. Две проставки на нижнем правом изображении центрируют подседельную трубу на корпусе каретки.
Когда я доволен подгонкой, можно приступить к закреплению трубки на месте с помощью сварочного аппарата. После прихватывания трубки ее можно снять с зажимного приспособления и полностью сварить. Мне нравится сваривать короткими отрезками, чередуя одну сторону трубы с другой, позволяя остыть между ними, это необходимо для сохранения тепла и в качестве В результате минимизируйте ЗТВ (зону термического влияния).
Во время процесса сварки я все время вставляю трубку обратно в зажимное приспособление, чтобы проверить наличие какого-либо движения, если что-то сместилось, вы можете исправить это с помощью приваривания на противоположной стороне механизма, чтобы оттянуть его назад, но плотный угол наклона для начала уменьшает риск смещения — если во время сварки есть зазор, он попытается закрыть, что приведет к плохой центровке.
Прихваточные швы позволяют расположить трубы так, чтобы можно было сваривать за пределами зажимного приспособления. Продолжайте проверять соосность и сваривайте небольшими сегментами.
Тот же самый процесс используется для изготовления нижней и верхней трубы с использованием измерений из моих предыдущих рисунков.Единственное различие заключается в том, что нижняя и верхняя трубы имеют два разреза, которые должны быть параллельны друг другу, это достигается за счет использования двух блоков труб, один для крепления к приспособлению для колпачка трубы на токарном станке, а другой используется как уровень. Поместив цифровой угловой искатель на верхнюю часть второго блока трубки, вы можете снять / повернуть трубку и узнать, находится ли она на уровне.
Чтобы убедиться, что митры на каждом конце выровнены, я зажимаю трубный блок в центре трубки (внизу слева) и проверяю это с помощью уровня перед каждым разрезом.
ХОМУТ СИДЕНЬЯ ТРУБКИ: Вы также можете купить один уже готовый
Мне еще предстоит найти специальную велосипедную трубку для подседельных трубок 30,9 мм, в прошлом я обрабатывал алюминиевые втулки, чтобы они вставлялись в трубки 34,9 мм x 0,9 мм, но они вскоре либо повредился, либо застрял в рамах. В поисках лучших решений я обнаружил, что другие производители рам использовали хомуты подседельной трубы и приваривали их к подседельной трубе. В идеале я хотел бы использовать трубки из нержавеющей стали 316 размером 35 мм x 2 мм, но у меня уже было немного мягкой стали подходящего размера.
Я начинаю обрезать трубу до приблизительного размера, а затем обрабатывать края на токарном станке, пока она не станет длиной 100 мм. Затем половина воротника обрабатывается до размера 33,1 мм, чтобы соответствовать подседельной трубе. Если посадка слишком тугая, я вставляю ее обратно в токарный станок и полирую наждачной бумагой до нужной посадки.
GUSSET: Стальные рамы, подобные этим
Даже со специальными приспособлениями для соединения труб всегда будет время, когда понадобится старый добрый метод бумажных шаблонов.Это хороший навык, которому нужно научиться, начиная с каркасного строительства. Некоторое программное обеспечение для дизайна имеет встроенный конструктор шаблонов, но я использую онлайн-инструмент под названием «Калькулятор преодоления трубки Metal Geek». Используя свой исходный рисунок, я ввожу углы и диаметры в калькулятор и позволяю ему делать свое дело, а затем вы выбираете формат, в котором хотите загрузить.
Для косынки я сделал два шаблона, а затем использовал Adobe Illustrator, чтобы объединить их в один (см. Второй рисунок для шаблона). Затем я вырезал его и использовал немного клея, чтобы приклеить шаблон к трубке.Резка как можно ближе к шаблону с помощью угловой шлифовальной машины, а затем точная подгонка с помощью напильника. При выборе файла вы хотите выбрать тот, радиус которого максимально приближен к радиусу родительской трубы. Если это невозможно, вы можете использовать дуговое движение из стороны в сторону при заполнении трубки. Продолжайте проверять прилегание к раме или основной трубе. Выделите все выступы маркером и продолжайте подпиливать, пока не будете довольны результатом. Это довольно утомительная работа (мне она действительно нравится).но, как упоминалось ранее, при сварке все зависит от плотной посадки под углом.
ВЫПЛАТЫВАНИЯ: Вы также можете купить их
Прежде чем я смогу надеть перья для цепи / сиденья, мне нужно сделать отсевы, самый простой вариант — купить готовый комплект со сменной подвеской для мехов, но как Мне нравится делать из велосипеда как можно больше, я начал обрабатывать некоторые из 25-миллиметровых нержавеющих стержней. Это относительно простой (но отнимающий много времени) процесс резки до грубой длины, обращенной к каждой стороне на токарном станке, просверливания 12-миллиметрового отверстия через центр, расточки остального до тех пор, пока толщина стенки не станет 2 мм, а затем обработать обратную сторону, чтобы сделать защелка для колеса, которая помогает при установке / снятии колеса.Раньше я просто обрабатывал его ровно, но установка колеса в этом случае может оказаться затруднительной.
ЦЕПИ И СИДЕНЬЯ: Почти готово
Отсев завершен, я могу перейти к моей нелюбимой части сборки хардтейла, сиденье / цепные перья. Я мог бы облегчить жизнь, купив предварительно изогнутые / формованные перья, но мне нравится свобода старта с 19-миллиметровой прямой хромомолибденовой стали и для этой сборки. 16 мм для перьев сиденья. Как и в большинстве других шагов, я начинаю с макбука и рисую нижние перья и перья, чтобы упростить определение углов и длины, а также упростить настройку приспособления.
Теперь, когда все измерения были сделаны, пришло время установить приспособление в его полную конфигурацию. Именно в этот момент я вспомнил, что урезал самую большую длину экструзии до 1200 мм, что означало, что мне нужно было немного сообразить, как я устанавливаю приспособление. Итак, снова пришлось вернуться к Macbook, чтобы составить план.
Я считаю, что цепь и перья сиденья делают или ломают раму, поэтому стоит уделить им время. Это тот же процесс, что и для остальной части рамы, но с дополнительным усложнением изгиба и формирования трубок.С помощью приспособления для токарного станка я отрезаю каждую стойку немного длиннее, а затем вырезаю оставшуюся часть вручную напильником. Постоянно проверяйте приспособление, пока оно не будет подходящим. Слишком туго или слишком ослаблено, и после сварки перья могут тянуться в разные стороны. В будущем я планирую создать специальный прибор, который поможет улучшить и ускорить этот процесс.
Больше деталей означает, что при сборке заднего треугольника будет еще много ошибок. Хорошая посадка гарантирует правильное выравнивание.
После того, как перья цепи и сиденья готовы, пора сварить прихваточным швом всю раму вместе и собрать ее, чтобы проверить соосность, а также убедиться, что все подходит.Затем я полностью свариваю и выполняю окончательное выравнивание.
Довольный тем, как выглядит рама, он вернулся в мастерскую, чтобы полностью сварить всю раму. После полной сварки настало время для последней проверки соосности и холодной установки рамы. В идеале у меня был бы специальный стол для выравнивания, но вместо этого это случай большого количества измерений, а затем скручивания, вытягивания и толкания в разных направлениях с помощью больших рычагов (металлический столб). Без специальной таблицы выравнивания это немного проб и ошибок, пока я не получу то, что мне нравится.Эта рама, заднее колесо немного наклонено в одну сторону вверху, но вы едва можете заметить это на глаз и не почувствуете, как он едет, так что для меня это достаточно хорошо.
Для крепления тормоза и подвески механизма у меня есть специальные приспособления, чтобы удерживать их в правильном положении, а затем просто приваривать их, опять же, не торопясь, чтобы снизить температуру и проверять выравнивание по ходу движения.
ВРЕМЯ СТРОИТЕЛЬСТВА
План с самого начала заключался в том, чтобы сохранить эту сборку как можно более низкой стоимости, поэтому, если у меня еще не было детали, я просмотрел все ведра со скидкой в Интернете в поисках лучших предложений или пошел по маршруту альтернативы без торговой марки от ebay, такой как пост-дроппер Satori, который, кажется, представляет собой ребрендированный RSP с небольшими изменениями. Что касается трансмиссии, я решил вернуться в прошлое к девятиступенчатой SRAM в сочетании с кассетой 11-42t. Это потому, что я не использую все десять передач на других своих байках — но в основном это чертовски дешевле.
Комплект колес: Superstar EX23 Boost 75 фунтов стерлингов пара
Шины: Maxxis Ardent / Crossmark 50 фунтов стерлингов
Вилка: Rockshox Recon RL 140 фунтов стерлингов
Шатуны: Sr Suntour Zeron 60 фунтов стерлингов
Трансмиссия: 9 Speed Sram x7 15 фунтов стерлингов
Кассета: Sunshine 11 -42t 9 скоростей 25 фунтов стерлингов
Тормоза: Magura mt2 60 фунтов стерлингов пара
Капельница: Satori 30.9 мм 70 фунтов стерлингов
рули: Raceface 25 фунтов стерлингов
педали: Promend 8 фунтов стерлингов
И все! Я закончил, пока. Я собираюсь кататься на велосипеде в течение следующих нескольких недель в необработанном состоянии, пробуя несколько разных положений кабеля (отсюда и изолента), и как только я буду счастлив, мне просто нужно приварить оставшиеся крепления кабеля, добавить скоба между пером и перетяжкой сиденья, чтобы помочь распределить силы от торможения, а затем выбрать цвет (всегда одно из самых трудных решений).